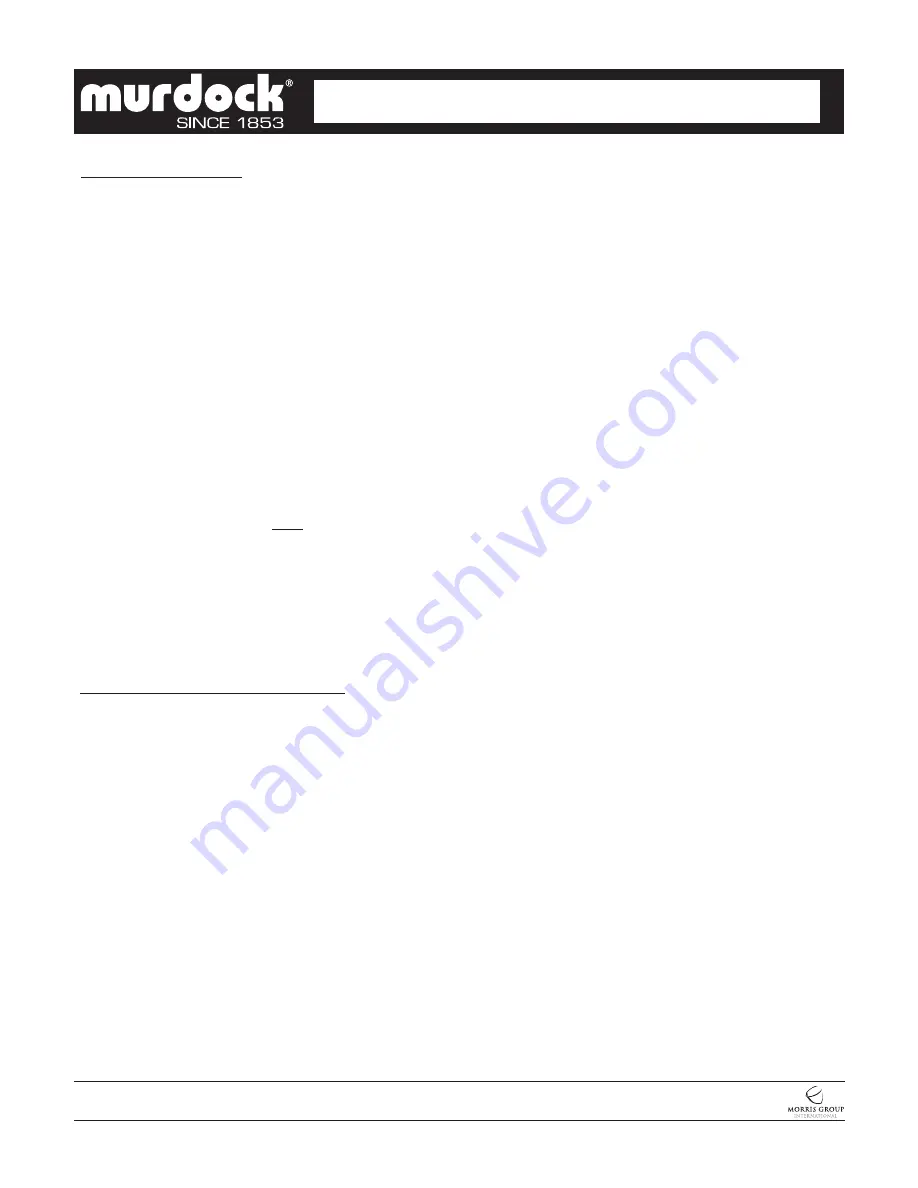
a. Ensure water supply service stop valve is fully open.
c. Check for twists or kinks in outlet tubing.
a. Cartridge – The water flow can be adjusted using a slotted narrow blade screwdriver and turning
clockwise to increase flow and counterclockwise to decrease flow.
TROUBLE SHOOTING:
b. Cold Water Thermostat – The water temperature can be adjusted using a slotted screwdriver and turning
clockwise to make colder and counterclockwise to make warmer.
c. Bubbler Stream - Bubbler can be rotated slightly to direct the stream backwards or forwards. Adjust the
stream to minimize splashing. Splashing may occur from bubbler stream if the unit is not level. Shim lower
mounting point, if necessary, to level chiller.
1. ADJUSTMENTS:
2. RESTRICTED OR NO WATER FLOW:
b. Verify minimum 20 psig supply line flow pressure.
3. WATER DRIPS OR WILL NOT SHUT OFF:
f. Check flow adjustment. See start up note #3.
h. No power to transformer connections, loose or wires cut.
b. Replace valve cartridge.
e. The cartridge valve located in the water control assembly or bubbler can also become clogged with
foreign material. The cartridge valve can only be replaced and not repaired.
d. Check the water inlet “Y” strainer. Sediment from the main supply can get trapped in the screen along
with installation materials such as pipe dope and flux. The screen should be cleaned and checked on a
regular basis and replace if needed.
g. Flow control in solenoid valve outlet elbow clogged remove & clean.
a. Open fixture. Loosen nuts holding valve bracket assembly to bottom of fixture but, do not remove. Move
complete valve bracket assembly further back from the front push pad and tighten to lock in place.
A131-VR
Page 9 of 12
New: 10/28/2020
7021-012-001
MURDOCK MFG. •
15125 Proctor Avenue • City of Industry, CA 91746 USA
Phone 800-453-7465 or 626-333-2543 • Fax 626-855-4860 • www.murdockmfg.com
Member of
2. If there are stubborn spots or if you wish to treat a scratch, synthetic abrasive general purpose pads such as
scotch brite are recommended.
1. To Remove water spots or rust spots, stainless steel cleaner/polish on a cloth is recommended.
3.
Periodically remove fountain top and clean out in-line strainer.
3. Stainless steel should be kept clean at all times. If a coating of stainless steel cleaner/polish is maintained,
stainless steel surfaces will retain their new, clean, polished appearance indefinitely.
2.
Excess dirt or poor ventilation will cause the compressor overload protector to turn the compressor off and it
will cycle on and off with no cold water coming out of bubbler. Periodically clean with vacuum cleaner, air
hose or brush the condenser fins and cabinet ventilation louvers. In environments where dirt and dust is
more prevalent, clean more frequently.
4.
Periodically remove access panel of cooler and clean out inline “Y’’ strainer
1.
Motors have lifetime lubrication and do not require scheduled maintenance.
CLEANING & MAINTENANCE GUIDE:
For Powder coated units:
Units should be cleaned using a mild soap solution with a sponge or cotton cloth.
Wipe down surfaces then rinse with clean water.
For Stainless steel units:
CONTEMPORARY WATER COOLERS
I N S TA L L AT I O N / M A I N T E N A N C E I N S T R U C T I O N S
DRINKING FOUNTAINS