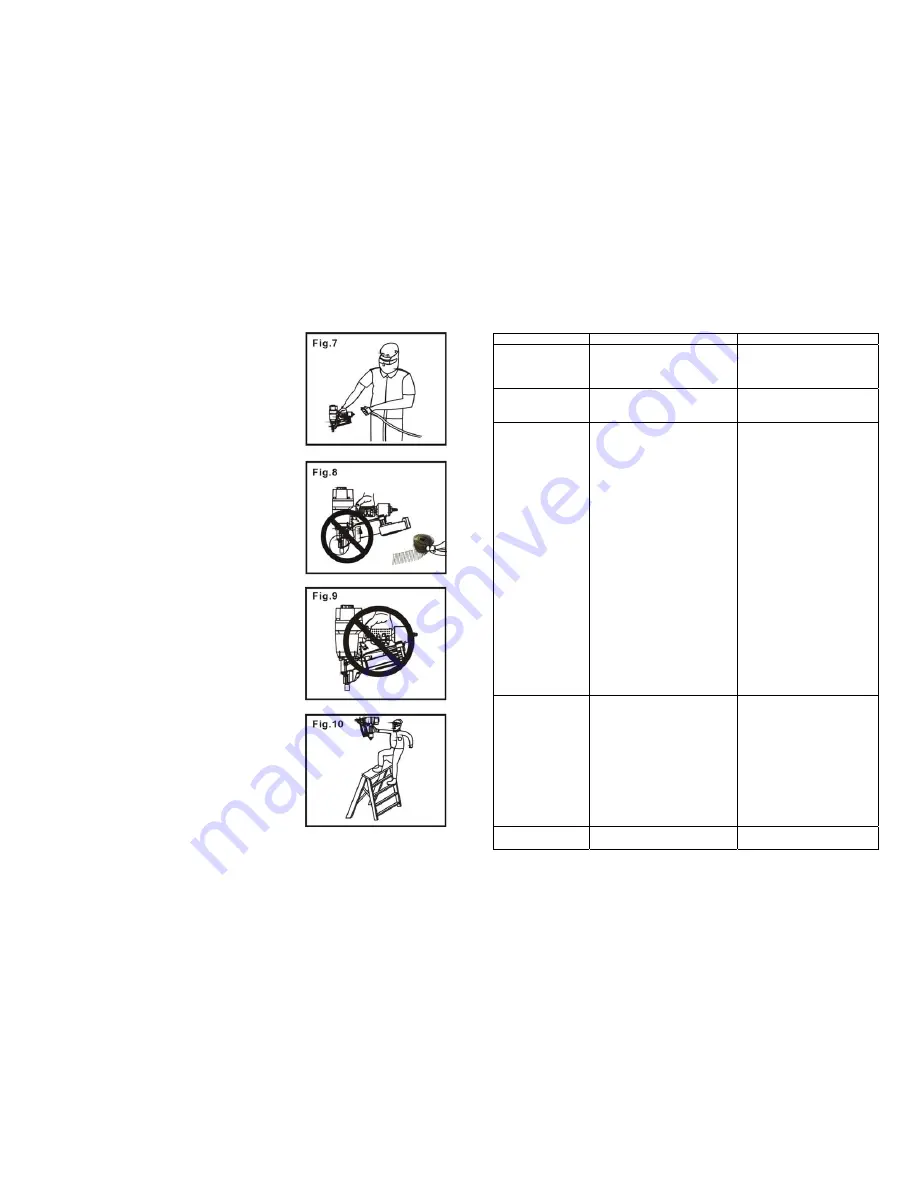
- 4 -
14. BEFORE USING TOOL
, carefully check if
there is any part damaged to obtain ideal results. Do
not use the tool if the tool has any air leaks,
uncompleted, damaged parts and needs repairing.
15. NEVER USE TOOL
if safety, trigger or spring is
inoperable, missing or damaged. Do not alter or
remove safety, trigger or springs Make daily
inspections for free movement of trigger and safety
mechanism.
16.ONLY USE PARTS AND FASTENERS
recommended by us.
17. CONNECT TOOL TO AIR SUPPLY BEFORE
loading fasteners to prevent
fastener from being fired
during
connection. The tool driving mechanism
may cycle when tool is connected to the air supply.
When not in use remove all fasteners from the nail
housing.
18. ALWAYS ASSUME THE TOOL CONTAINS
FASTENERS
. Keep the tool
pointed away from
yourself and others
at all times. No horseplay. Respect
the tool as a working implement.
19. DO NOT LOAD FASTENERS
with trigger or
safety depressed to prevent unintentional firing of a
fastener.
20. REMOVE FINGER FROM TRIGGER
when
not driving fasteners. Never carry
tool with finger on
trigger: tool will fire a
fastener if safety is bumped
while trigger
is depressed.
21. DON'T OVER REACH.
Keep proper footing
and balance at all times when using or handling the
tool.
22. FIRE FASTENERS INTO WORK SURFACE
ONLY:
NEVER into materials
too hard to penetrate.
PROBLEM CAUSE
SOLUTION
Failure to start tool.
1. Tool dry, lacks lubrication.
2. The spring in the cylinder cap is
damaged.
3. Valve sticks with cylinder cap.
1. Use pneumatic tool oil
2.Replace the spring in the
cylinder cap.
3.Disassemble/check/lubricate
Blade driving fasteners
too deeply
1. Safe bracket poison is not correct.
2. Air pressure is too high.
1. Rotate knob of the adjuster to
move safe bracket down.
2. Decrease air pressure.
Skipping
fasteners/ feeding
intermittently
1. Having foreign matters between the
small piston and small cylinder.
2. O-ring on the small piston is worn
and damaged.
3. Tool dry and lacks lubrication.
4. The spring on the small piston is
damaged.
5. Air pressure is lower.
6. Connecting screw of nose and body
is loose.
7. Stopped hook can't stop the
fasteners.
8. Bent fasteners.
9. Wrong size fasteners.
10. Gasket is damaged.
11.Dry small piston
12. Small piston bumper is worn and
damaged.
13. Feed hook is binding.
14. Nail length is not correct with
loading space of nail housing.
15. Weld wires in nail coilare broken.
1. Disassemble/ clean/lubricate.
2.Check/replaceO-ring/ lubricate
3. Use pneumatic ic tool oil.
4. Replace small piston the spring.
5. Increase the air pressure, but don't
exceed 120 PSI (8.3 bar).
6. Tighten al l screws.
7.Replace taper spring of the
stopped hook.
8. Use recommended fasteners.
9.Use recommended fasteners
10. Replace gasket/t tighten screw.
11. Open nai l housing, place several
drops of pneumatic tool oil into end
cover hole of the small piston.
12.Replace bumper and lubricate
small piston.
13. Clean feed hook and torsion
spring.
14.Adjust adjusting nut at the nail
housing tail portion according to the
recommended nail length to make
arrow on the nail housing tail point
to correct direction.
15. Stop using.
Runs slowly or has
power loss
1. Tool dry, lacks lubricate ion
2. The spring in the cylinder cap is
damaged.
3. Having foreign matters between
piston assembly and cylinder.
4. Have not assembled the cylinder to
home posit ion.
5. O-ring on the valve is dry after
disassembly.
6. Air pressure is too low.
7.Driver is worn (sort)
8. Inner diameter of hose is small.
1. Use pneumatic tool oil.
2. Replace the spring in the cylinder
cap.
3. Disassemble/clean/lubricate.
4. Reassemble after disassembling.
5.Reassemble after lubricating
6. Increase the air pressure, but don't
exceed 120 PSI (8.3 bar).
7. Replace piston assembly.
8. Use bigger inner diameter of the
hose.
Fasteners are jammed
1. Fasteners are wrong size.
2. Weld wires in nail coil are broken.
1. Use recommended fasteners.
2. Stop using.