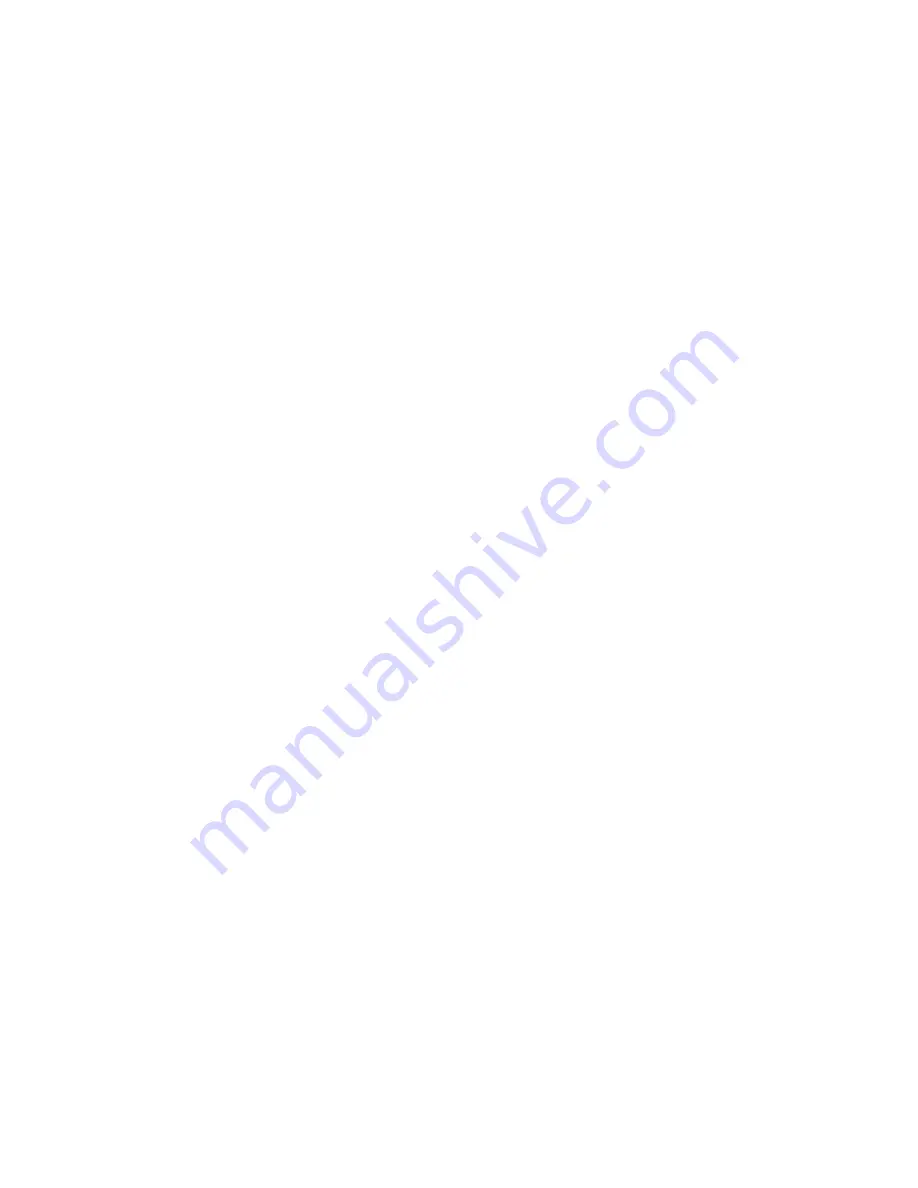
35
Strainer Cleaning, Heat Exchanger Cleaning
All Multistack modules have a 30-mesh filter strainer in the condenser and evaporator inlet headers. The purpose of the strainer is to prevent debris from
entering the heat exchanger. An external “Y” or basket type system strainer should also be installed as a pre-filter to the Multistack strainers. There is
no pre-determined time for cleaning the strainer cartridges. The frequency of this process is dependant on the water quality in the condenser and/or
evaporator loop. Normally, debris in a water loop is takes the path of least resistance and accumulates in the last modules to receive water.
Multistack modules include the Multiflush automatic blow down system installed on the condenser side of the last module in the chiller array. The
Multiflush system is controlled by a timer in the Master Control and opens once a day to remove debris from the loop. Multiflush does not eliminate the
need to pull and clean the strainers, but reduces the frequency.
The effect of debris buildup in the condenser water inlet filter cartridge will create nuisance HP (high pressure) faults. By checking the pressure differential
between the inlet and outlet of the condensers, it can be determined if the strainers are contaminated. Refer to the MS 010-085X Product Data Catalog for
correct pressure drop of your model. For an MS070X module with a 10° F Delta T, the condenser side pressure drop should be 17’ / 7.4 psi; for chilled water
16’ / 7 psi. To keep HP faults from repeating, the strainers will need to be pulled and cleaned. If HP faults still occur after cleaning the strainer cartridges
the condenser pump should be checked for proper flow. If flow is not a problem the heat exchangers may need to be cleaned. Refer to Multistack Heat
Exchanger Cleaning Bulletin (MAINT-003-0416). Use this procedure to remove and clean the filter cartridges on the condenser side.
1. Turn off the chiller, shut down the condenser pump, and close the butterfly/gate valves to the condenser.
2. Drain the water remaining in the condensers and header pipes by opening the drain valve in the pipe stubs or by removing the end grooved fitting cap
on the Multiflush system.
3. Remove the first filter in the Multiflush and remove all remaining filters in the bottom condenser header pipes.
4. Slowly open the top butterfly / gate valve, allowing water to flow through the condensers and onto the floor for approximately 30 seconds. This will
push out any debris trapped in the bottom of the heat exchanger as the filters are removed.
5. Clean the filters with a hose, power washer, or wire brush as needed and re-install. Slide filters in until contacting the filter stop ring on the first
module. Keep an extra set of strainers for quick re-installation. These filters are available for purchase through Multistack representatives.
6. Close the system by installing any grooved fitting clamps previously removed.
7. Open the 1/4-inch petcock bleed valves on the pipe stubs.
8. Fill the system by opening the bottom butterfly/gate valve and filling from the bottom up. Close the 1/4-inch petcock valves and open the top
butterfly/gate valve after air has been bled from the system.
9. Start the condenser pump. Bleed any remaining air in the system once the pump has started and start the chiller.
If circuits trip out on Low Suction Temperature, or Low Chilled Water Temperature, check the chilled water inlet filter cartridge. The strainers are located
in the top header on the chilled water side. The previous instructions on condenser strainer removal do not need to be exactly followed. If the strainers
are clean the fault may be caused by a low flow condition or a low set point in the Master Control. If these possibilities are eliminated the evaporator heat
exchangers may need cleaning.
Compressor Oil Level
All compressors on water-cooled modules have an oil level sight glass on each compressor. Each module is run tested and the oil level is set at the factory.
R-410A scroll compressors are single stage and oil level is set at 1/8 – 1/4 full sight glass. The compressor uses POE oil. Use Copeland type 998-E022 or Nu
Calgon 32-3MA. Call Multistack service at (608)366-2400 for factory oil charge for each compressor.
Refrigerant Charge / Evacuation
All water-cooled modules are factory charged to recommended refrigerant volumes. Prior to charging, each circuit is evacuated to 150 microns and held
15 minutes. The proper refrigerant charge for each module can be found on the module data plate. For proper charge on water-cooled modules, the circuit
should be charged until the sight glass clears.
Model
Refrigerant Lbs. Per Circuit Oil Charge Per Circuit (in Pints)*
MS010X 8
3.5
MS015X 8
6.9
MS020X 8
6.9
MS030X 12
6.9
MS040X 15 9.5
MS050X 18
9.5
MS070X 24
13.3
MS085X 28
13.3
* Based on Copeland compressors