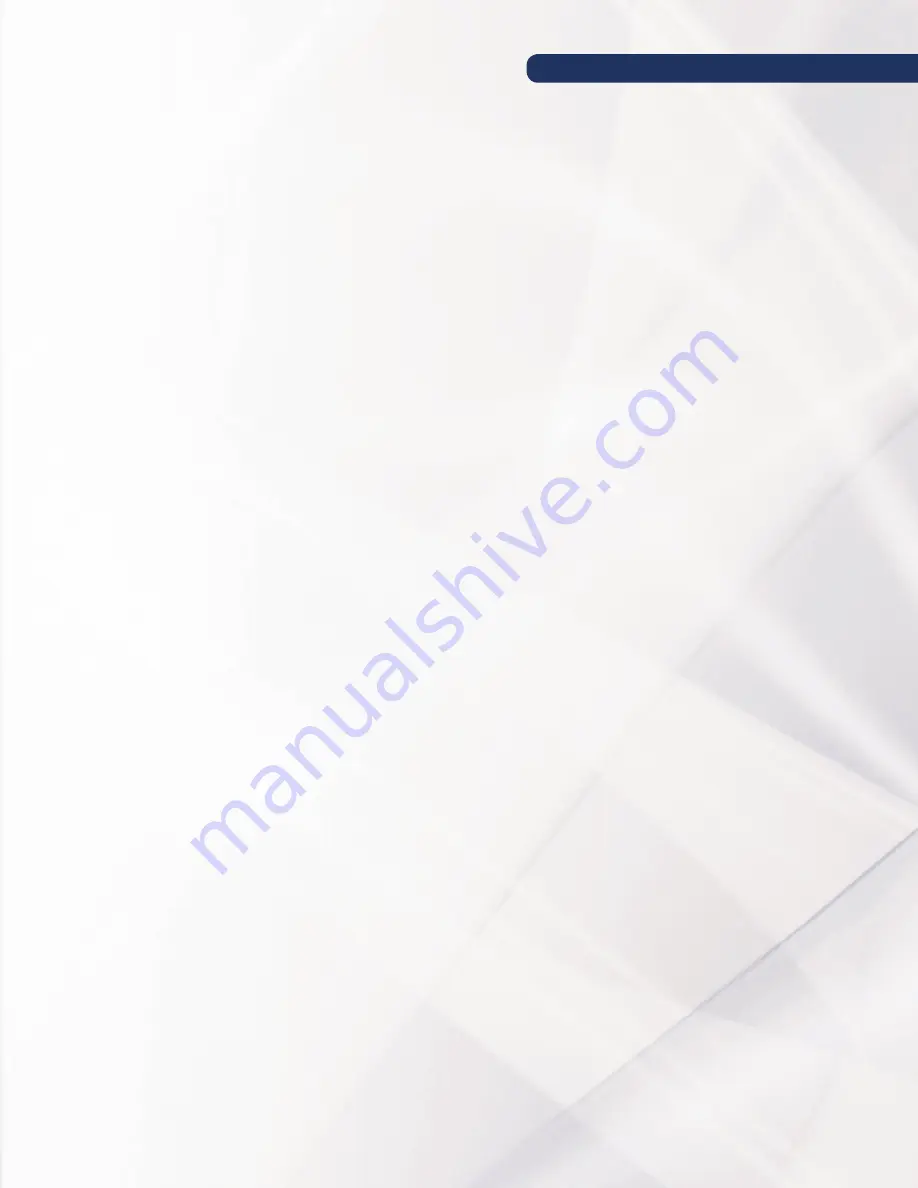
19
VersaTemp™ Water-to-Water Heat Pumps
Guide Specifications
7. OPTIONAL: Interoperability
The chiller shall be capable of interfacing to a building automation system. Interface shall be accomplished using an Interoperability Web portal
and shall be capable of communication over BACNet, Modbus or LON.
I. Chiller shall have external inputs and outputs to be compatible with the building management system to include remote start/stop capability
and cooling alarm output.
J. Each refrigerant circuit shall include all refrigerant specialties including a properly sized dynamic receiver to provide reliable operation down to
40 F ambient.
K. OPTIONAL: Single Point Power Connection
Chiller shall be provided with a single point power connection at a 5,000 amp SCCR. This will include pre-engineered wiring for field
installation and connection to a factory mounted chiller junction box. Junction box shall include branch circuit protection for each module
and provide a single connection point to building power.
a. OPTIONAL—SCCR greater than 5,000 amps: Contact factory. Depending on voltage and module size SCCR up to 85,000 may be available.
Some higher SCCR will require fused protection as opposed to the standard isolation circuit breakers.
L.
OPTIONAL:
Variable Flow Operation – Chilled Water
Butterfly type isolation valves shall incorporate appropriate accessories and controls to allow the chiller to operate efficiently in a variable primary flow
system. Motorized valve per module shall operate for variable flow.
M.
OPTIONAL:
Pump Module
Provide a pump module of size and capacity indicated on the drawings and schedules. The pump module shall be interconnected though the common
chiller header system and require no additional water connections. Pump module will become an integral part of the chiller system. The pump module
shall incorporate dual in-line centrifugal pumps in a primary/standby pumping arrangement. Pump starters and controls shall be provided to enable
manual selection of lead pump. In addition, in the event of a loss-of-flow failure of the chilled water system, the pump module controls shall disable the
lead pump and automatically start the standby pump. The module shall be completely factory assembled and tested prior to shipment.
N.
OPTIONAL:
Lifting Frame
Optional six-inch I-beam painted steel frame will be provided with all modules mounted upon it. Typically, all water and wiring connections will be made
between the modules at the factory. Depending on chiller length or customer requests, larger I-beams can be furnished.
2.03 SAFETIES, CONTROLS AND OPERATION
A. The chiller safety controls shall be provided (minimum) as follows:
1. Low evaporator refrigerant pressure
2. Loss of water flow through the evaporator
3. High condenser refrigerant pressure
4. High compressor motor temperature
5. Low suction gas temperature
6. Low leaving evaporator water temperature
B. Failure of chiller to start or chiller shutdown due to any of the above safety cutouts shall be annunciated by display of the appropriate diagnostic
description at the unit control panel. This annunciation will be in plain English. Alphanumeric codes shall be unacceptable.
C. The chiller shall be furnished with a master controller as an integral portion of the chiller control circuitry to provide the following functions:
1. Provide automatic chiller shutdown during periods when the load level decreases below the normal operating requirements of the chiller. Upon
an increase in load, the chiller shall automatically restart.
2. Provisions for connection to automatically enable the chiller from a remote energy management system.
3. The control panel shall provide alphanumeric display showing all system parameters in the English language with numeric data in English units.
D. Normal Chiller Operation
1. When chiller is enabled, the factory supplied master controller modulates the chiller capacity from minimum to maximum as required by
building load.
2. The chiller control system shall respond to entering water temperature and will have an integral reset based on entering water temperature to
provide for efficient operation at part-load conditions.
PART 3 INSTALLATION
3.01 PIPING SYSTEM FLUSHING PROCEDURE
A. Prior to connecting the chiller to the building chilled water loop, the piping shall be flushed with a detergent and hot water (110-130° F) mixture
to remove previously accumulated dirt and other organic residue. In old piping systems with heavy encrustation of inorganic materials consult a
water treatment specialist for proper passivation and/or removal of these contaminants.
B. During the flushing a 30 mesh (max.) Y-strainers (or acceptable equivalent) shall be in place in the system piping and examined periodically as
necessary to remove collected residue. The use of on board chiller strainers shall not be acceptable. The flushing process shall take no less than six
hours or until the strainers, when examined after each flushing, are clean. Old systems with heavy encrustation shall be flushed for a minimum of
24 hours and may take as long as 48 hours before the filters run clean. Detergent and acid concentrations shall be used in strict accordance with
the respective chemical manufacturers instructions. After flushing with the detergent and/or dilute acid concentrations the system loop shall be
purged with clean water for at least one hour to ensure that all residual cleaning chemicals have been flushed out.
C. Before supplying water to the chiller the Water Treatment Specification shall be consulted for requirements regarding the water quality during
chiller operation. The appropriate chiller manufacturer’s service literature shall be available to the operator and/or service contractor and
consulted for guidelines concerning preventative maintenance and off-season shutdown procedures.
Continued on next page.