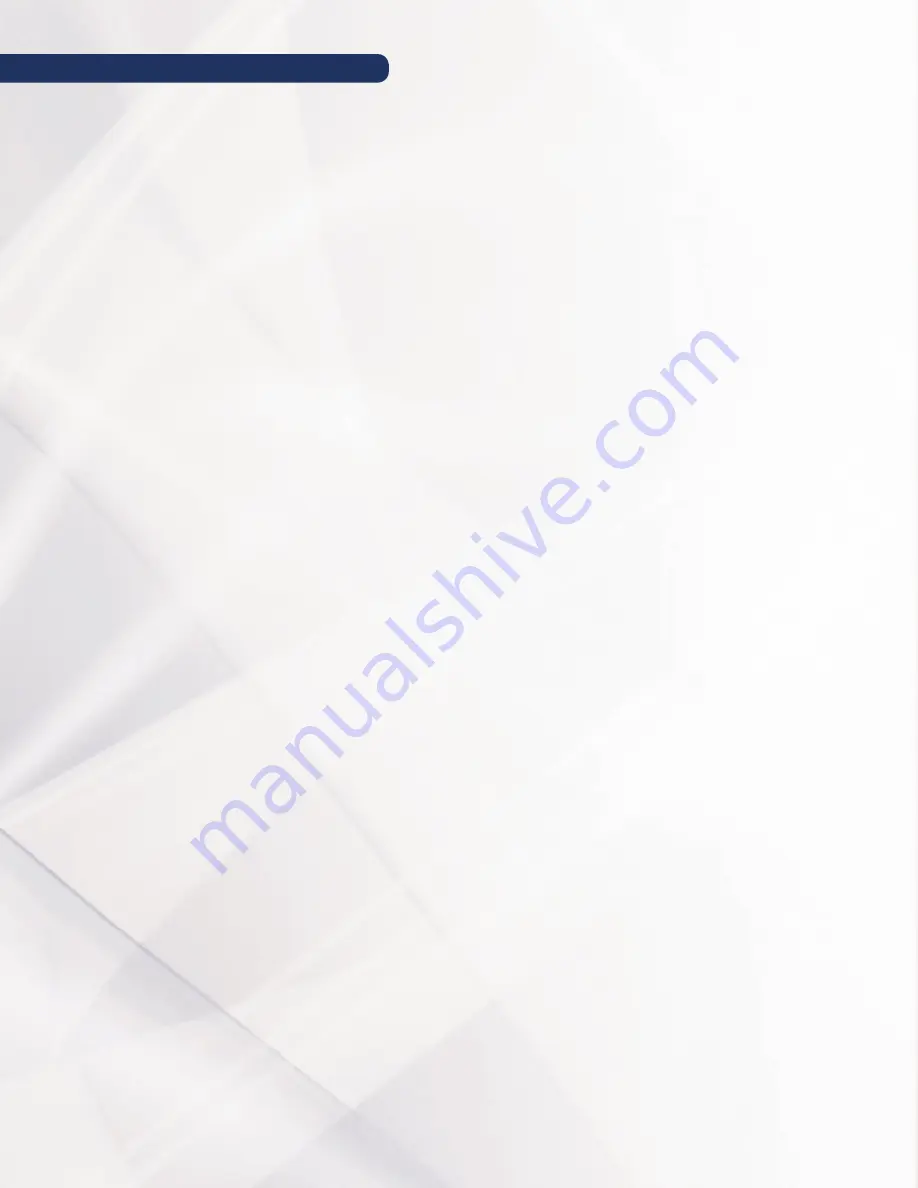
18
VersaTemp™ Water-to-Water Heat Pumps
C. General
1. Chiller Modules shall be ETL listed in accordance with UL Standard 1995, CSA certified per Standard C22.2#236.
2. Modules shall ship wired and charged with refrigerant. All modules shall be factory run tested before shipment on an AHRI certified or third-party
verified test stand.
3. Compressors, heat exchangers, fans, piping and controls shall be mounted on a heavy gauge, powder coated steel frame. Electrical controls,
contactors, and relays for each module shall be mounted within that module. Module shall be provided within a steel enclosure suitable for
outdoor use. Exposed steel surfaces shall be provided with a powder coat paint finish.
D. Piping:
1. Chilled Water Mains: Each module shall include supply and return mains for chilled water. Cut grooved end connections are provided for inter-
connection to six- or eight-inch standard (6.625 inch, 8.625 inch) outside diameter piping with grooved type couplings. Rolled grooved shall be
unacceptable.
2. Hot Water Mains: Each module shall include supply and return mains for hot water. Cut grooved end connections are provided for interconnection
to six- or eight-inch standard (6.625 inch, 8.625 inch) outside diameter piping with grooved type couplings. Rolled grooved shall be unacceptable.
E. Heat Exchangers:
1. Evaporator shall be a brazed plate heat exchanger constructed of 316 stainless steel; designed, tested, and stamped in accordance with UL 1995
code for 650 psig working pressure. The evaporator heat exchanger shall not be mounted above the compressor to eliminate liquid refrigerant
migration to the evaporator and potential liquid slugging on start-up.
2. Auxiliary air-cooled coil shall have aluminum finss mechanically bonded to copper tubes and shall be factory leak-tested.
3. Hot water heat exchanger shall be a brazed plate heat exchanger constructed of 316 stainless steel; designed, tested, and stamped in accordance
with UL 1995 code for 650 psig working pressure. The heat exchanger shall not be mounted above the compressor to eliminate liquid refrigerant
migration to the heat exchanger with consequent liquid slugging on start-up.
F. Compressor: Each module shall contain two hermetic scroll compressors in a tandem piping arrangement mounted to the module with rubber-in-
shear isolators. Each system also includes high discharge pressure and low suction pressure safety cut-outs.
G. Source/Sink Fans: Each module shall contain dual (four in ARA 060X) fans for each refrigerant circuit. Module shall use ECM Fans (575-volt units
require an additional transformer). Blades are aluminum construction owlet design seven-blade axial fan with integral ECM motor (direct drives
with external VFD driven motors are not acceptable). Efficiency exceeds criteria set out in the ErP 2015 directive. Individual fans are factory tested.
Encapsulation required. Encapsulation is a process of filling a complete electronic assembly with a solid compound for resistance to shock and
vibration, and for exclusion of moisture and corrosive agents. Sound pressure reductions at 30 feet, as compared to standard fan option, ranges
from 3-6 dBA.
H. Central Control System
1. Scheduling of the various compressors shall be performed by a microprocessor based control system (Master Controller). A new lead compressor is
selected every 24 hours to assure even distribution of compressor run time.
2. The master controller shall monitor and report the following on each refrigeration system:
a. Discharge Pressure Fault
b. Suction Pressure Fault
c. Compressor Winding Temperature
d. Suction Temperature
e. Evaporator Leaving Chilled Water Temp.
f. Condenser Leaving Hot Water Temp
3. The master controller shall be powered by the chillers single point power connection and shall monitor and report the following system parameters:
a. Chilled Water Entering and Leaving Temperature
b. Discharge Refrigerant Temperature
c. Proof of Chilled Water Flow
d. Hot Water Entering and Leaving Temperature
e. Discharge Refrigerant Temperature
f. Proof of Hot Water Flow
4. An out of tolerance indication from these controls or sensors shall cause a “fault” indication at the master controller and shutdown of that
compressor with the transfer of load requirements to the next available compressor. In the case of a system fFault the entire chiller will be shut
down. When a fault occurs, the master controller shall record conditions at the time of the fault and store the data for recall. This information shall
be capable of being recalled through the keypad of the master controller and displayed on the master controller’s two- line, 40-character back-lit
LCD. A history of faults shall be maintained including date and time of day of each fault (up to the last 20 occurrences).
5. Individual monitoring of leaving chilled water temperatures from each refrigeration system shall be programmed to protect against freeze-up.
Individual monitoring of leaving hot water temperatures from each refrigeration system shall be programmed to protect against hi head pressure
conditions.
6. Operation:
a. The control system shall monitor entering and leaving chilled water and hot water temperatures to determine both the chilled water and hot
water system demand. The control system will use the demand to make staging mode (cooling, heating, or simultaneous heat recovery)
decisions and select the number of compressors required to operate. Mode decisions shall be available from the controller as well as via
remote input. Response times and set points shall be adjustable. The system shall provide for variable time between compressor sequencing
and temperature sensing to optimize chiller performance at varying loads.
b. Modules shall be able to provide the following capabilities:
1. Full cooling capacity with zero need for hot water.
2. Full cooling capacity with ability to modulate the amount of hot water output between a minimum and maximum value by varying amount of
refrigerant routed to the air-to-refrigerant condenser coil.
3. Full heating capacity with zero need for chilled water.
Multistack has a policy of continual improvement and reserves the right to change product design, literature and specifica-
tions without notice. For more information on this and other Multistack products, contact your nearest Multistack dealer.
Guide Specifications