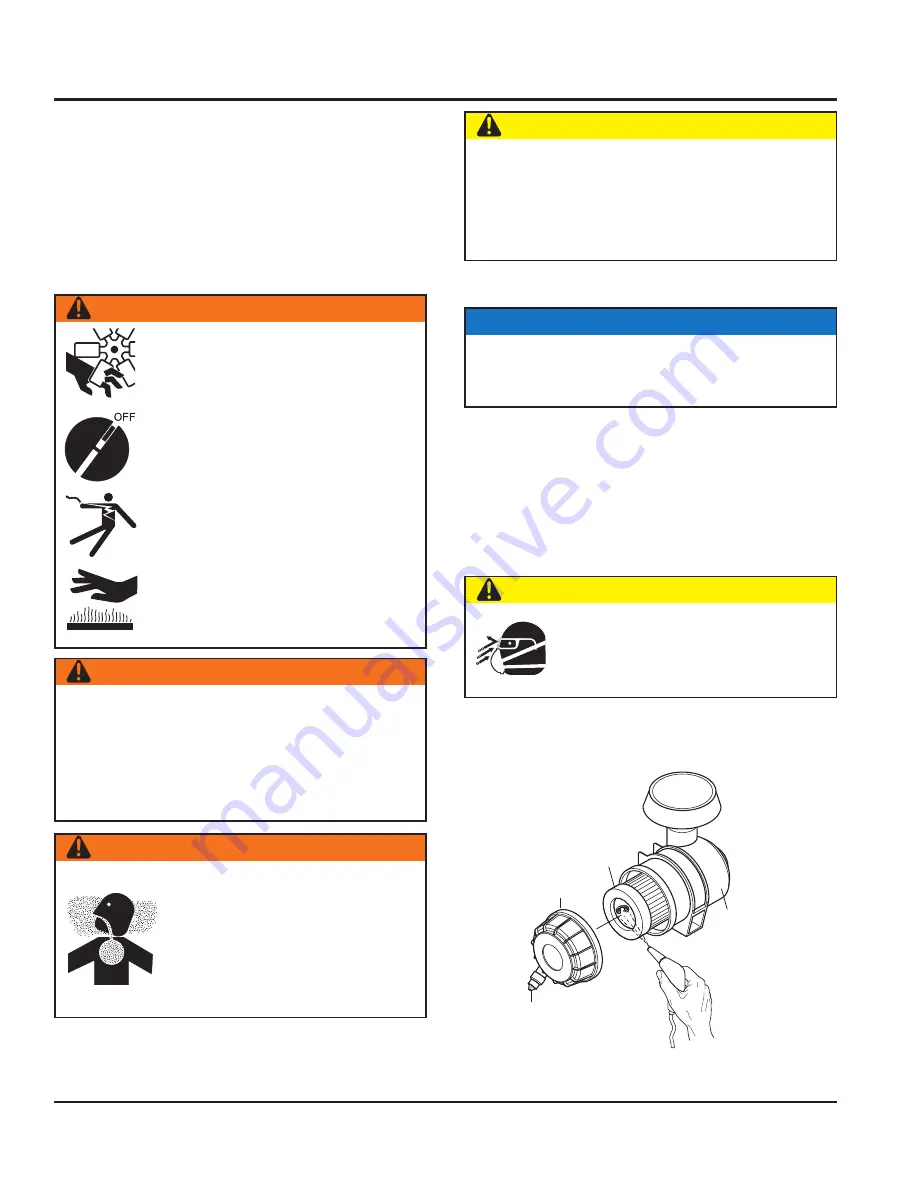
PAGE 54 — WRS5200DFPU HYDRAULIC ROLLER SCREED • OPERATION MANUAL — REV. #2 (03/08/18)
MAINTENANCE
General maintenance practices are crucial to the
performance and longevity of your screed. This equipment
requires routine cleaning, truss sections inspection,
lubrication and V-belt inspection for wear and damage.
Reference (Table 4) and (Table 5) for scheduled engine
and screed maintenance.
The following procedures, devoted to maintenance, can
prevent serious screed damage or malfunctioning.
WARNING
Accidental starts can cause severe injury
or death.
ALWAYS place the ignition switch in the
OFF position before performing any
maintenance.
Disconnect negative battery cable from
battery before servicing.
ALWAYS allow the engine to cool
before servicing.
NEVER attempt any
maintenance work on a hot (muffler,
radiator, etc.) power unit.
WARNING
Certain maintenance operations or machine
adjustments require specialized knowledge and skill.
Attempting to perform maintenance operations or
adjustments without the proper knowledge, skills or
training could result in equipment damage or injury to
personnel. If in doubt, consult your dealer.
WARNING
Some maintenance operations may
require the engine to be run. Ensure
that the maintenance area is well
ventilated. Gasoline engine exhaust
contains poisonous carbon monoxide
gas that can cause unconsciousness
and may result in
DEATH
AIR FILTER (DAILY)
The gasoline/propane engine used with this screed is
equipped with a replaceable, high-density paper air filter
element.
Check the air filter (Figure 51) daily or before starting the
engine. Check for and remove any heavy buildup of dirt and
debris along with loose or damaged components.
1. Unlock/release the clamps that secure the dust pan
cover to the body.
Figure 51. Air Filter Components
CAUTION
ALWAYS disconnect the spark plug wire from the spark
plug and secure away from the engine before performing
maintenance or adjustments on the machine.
ALWAYS disconnect battery cables before attempting
any service or maintenance on screed.
NOTICE
Operating the engine with loose or damaged air filter
components could allow unfiltered air into the engine
causing premature wear and failure.
CAUTION
Wear protective equipment such as
approved safety glasses or face shields
and dust masks or respirators when
cleaning air filters with compressed air.
PRIMARY
AIR FILTER
ELEMENT
BLOW COMPRESSED
AIR FROM THE
INSIDE OUT
DUST PAN
EVACUATOR
VALVE
BODY
Summary of Contents for WRS5200
Page 5: ...PAGE 5 WRS5200DFPU HYDRAULIC ROLLER SCREED OPERATION MANUAL REV 2 03 08 18 NOTES...
Page 23: ...PAGE 23 WRS5200DFPU HYDRAULIC ROLLER SCREED OPERATION MANUAL REV 2 03 08 18 NOTES...
Page 66: ...PAGE 66 WRS5200DFPU HYDRAULIC ROLLER SCREED OPERATION MANUAL REV 2 03 08 18 NOTES...
Page 81: ...PAGE 81 WRS5200DFPU HYDRAULIC ROLLER SCREED OPERATION MANUAL REV 2 03 08 18 NOTES...