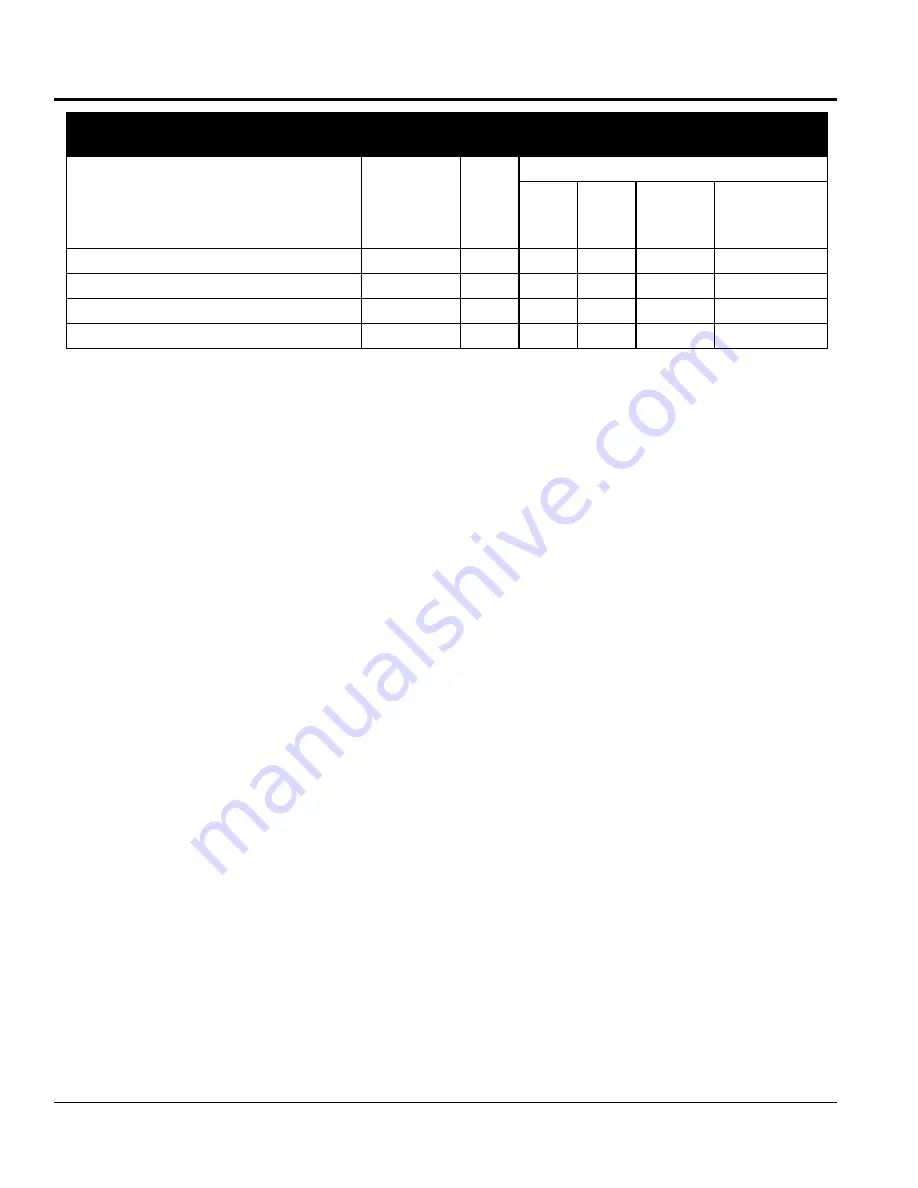
PAGE 20 — TB12SE/TB12PE TUFFTRUK POWER BUGGY • OPERATION MANUAL — REV. #0 (04/01/22)
MAINTENANCE
Table 5. Power Buggy Maintenance Schedule
Check Item
OPERATION DAILY
Periodic Maintenance Interval
Every
25 Hrs
Every
50 Hrs
Every
100-125
Hrs
Every 200 Hrs
Tub
Clean
X
X
Tub For Cracks/Deformations
Check
X
Tires For Severe Cuts/Wear
Check
X
Fastners
Check
X