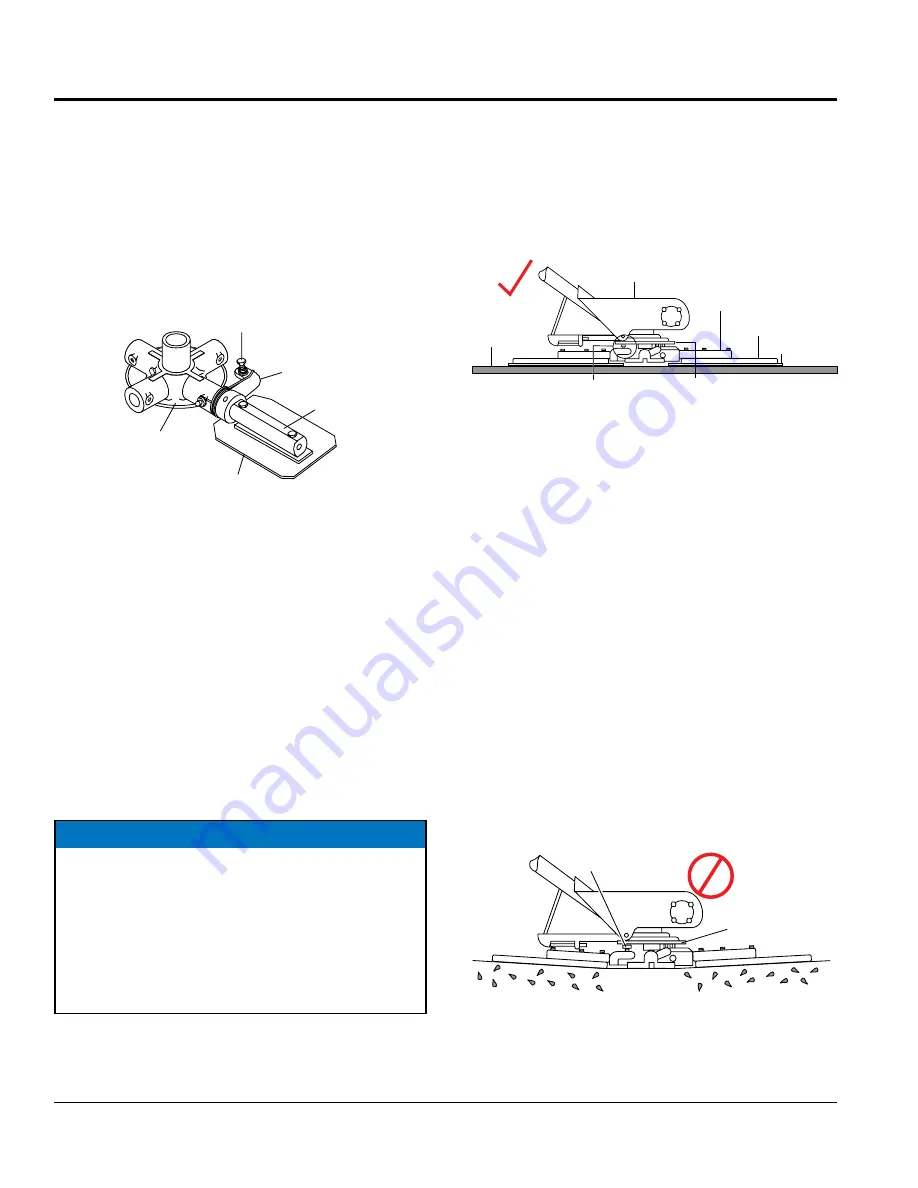
PAGE 36 — BS90C WALK-BEHIND TROWEL • OPERATION AND PARTS MANUAL — REV. #0 (9/4/15)
BLADE PITCH ADJUSTMENT PROCEDURE
The maintenance adjustment of blade pitch is an adjustment
that is made by a bolt (Figure 52) on the arm of the trowel
arm lever. This bolt is the contact point of the trowel arm
lever to the lower wear plate on the thrust collar. The goal
of the adjustment is to promote consistent blade pitch and
finishing quality. Adjustments are made by tightening or
loosening the blade pitch adjustment bolt.
Figure 52. Blade Pitch Adjustment Bolt
Watch for the following indications when determining if
blade pitch adjustments are necessary:
• Is the machine wearing out blades unevenly, (i.e. one
blade is completely worn out while the others look
new)?
• Does the machine have a perceptible rolling or
bouncing motion when in use?
• Look at the machine while it is running, do the guard
rings “rock up and down” relative to the ground?
If it is determined that blade pitch adjustments are required
do the following:
1. Place the trowel on a flat, level area free of dirt and
debris.
SPIDER
PLATE
BLADE PITCH
ADJUSTMENT
BOLT
TROWEL
ARM
TROWEL LEVER
FINGER
TROWEL
BLADE
NOTICE
Before any blade pitch adjustments can be made it
is essential to have a clean level area free of dirt and
debris to test the trowel. Any unlevel spots in the floor
or debris under the trowel blades will give an incorrect
perception of adjustment. Ideally, a 5 x 5 ft. (1.5 x 1.5
meter), three-quarter inch (19 mm) thick
FLAT
steel
plate should be used for testing.
MAINTENANCE
2. Pitch the blades as flat as possible. The pitch
adjustment bolts (Figure 53) should all barely make
contact (0.10 inch max. clearance) with the
lower
wear plate
on the spider. All pitch alignment bolts
should be spaced the same distance from the lower
wear plate. If one is not making contact, adjustment
will be necessary.
Figure 53. Correct Blade Pitch (Flat)
3. Adjust the “
high
” bolts down to the level of the one that
is not touching, or adjust the “
low
” bolt up to the level
of the higher ones. If possible, adjust the low bolt up
to the level of the rest of the bolts. This is the fastest
way, but may not always work. Verify after adjustment
the blades pitch correctly.
4. Blades that are incorrectly adjusted often will not be
able to pitch flat. This can occur if the adjusting bolts
are raised too high. Conversely, adjusting bolts that
are too low will not allow the blades to be pitched high
enough for finishing operations.
5. If, after making blade pitch adjustments the machine
is still finishing poorly, blades, trowel arms, and trowel
arm bushings may be suspect and should be looked
at for adjustment, wear, or damage.
6. Figure 54 illustrates, "incorrect alignment", worn spider
bushings or bent trowel arms.
Figure 54. Incorrect Spider Plate Alignment
GEARBOX
TROWEL
ARM
MOUNTING
BAR
BLADE
STEEL TEST
SURFACE
LOWER
WEAR PLATE
PITCH
ADJUSTMENT
BOLT
NO
“DISHED” EFFECT ON
FINISHED CONCRETE
PITCH
ADJUSTMENT
BOLT
LOWER
WEAR PLATE
Summary of Contents for BS90C
Page 70: ...PAGE 70 BS90CWALK BEHINDTROWEL OPERATION AND PARTS MANUAL REV 0 9 4 15 EX27 CRANKCASE ASSY ...
Page 72: ...PAGE 72 BS90CWALK BEHINDTROWEL OPERATION AND PARTS MANUAL REV 0 9 4 15 EX27 CRANKSHAFT ASSY ...
Page 74: ...PAGE 74 BS90CWALK BEHINDTROWEL OPERATION AND PARTS MANUAL REV 0 9 4 15 EX27 MUFFLER ASSY ...
Page 76: ...PAGE 76 BS90CWALK BEHINDTROWEL OPERATION AND PARTS MANUAL REV 0 9 4 15 EX27 AIR CLEANER ASSY ...
Page 78: ...PAGE 78 BS90CWALK BEHINDTROWEL OPERATION AND PARTS MANUAL REV 0 9 4 15 EX27 GOVERNOR ASSY ...
Page 80: ...PAGE 80 BS90CWALK BEHINDTROWEL OPERATION AND PARTS MANUAL REV 0 9 4 15 EX27 BLOWER ASSY ...
Page 84: ...PAGE 84 BS90CWALK BEHINDTROWEL OPERATION AND PARTS MANUAL REV 0 9 4 15 EX27 FUEL TANK ASSY ...
Page 86: ...PAGE 86 BS90CWALK BEHINDTROWEL OPERATION AND PARTS MANUAL REV 0 9 4 15 EX27 CARBURETOR ASSY ...
Page 90: ...PAGE 90 BS90CWALK BEHINDTROWEL OPERATION AND PARTS MANUAL REV 0 9 4 15 EX27 OIL SENSOR ASSY ...
Page 93: ...BS90CWALK BEHINDTROWEL OPERATION AND PARTS MANUAL REV 0 9 4 15 PAGE 93 NOTES ...