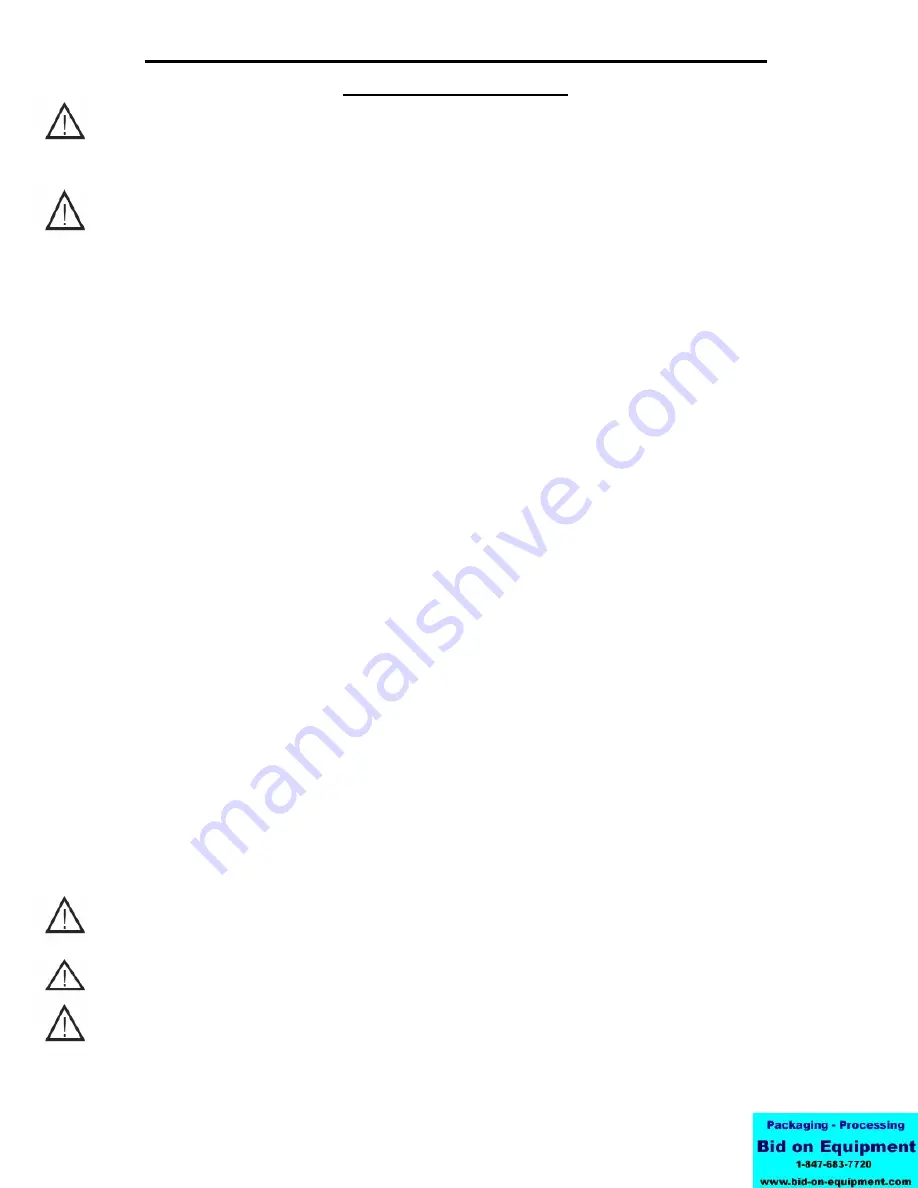
Concentrations of Propylene Glycol in excess of 50% will destroy o-rings in fittings and pump. Water shoul
be added to the system first or a liquid solution diluted Propylene Glycol mix.
Before filling system with Propylene Glycol and water, pressure test the piping system with compressed air.
Testing should be done at a minimum of 50 psi but no greater than 50 psi over the system's normal operating
pressure. The system should hold air pressure for a minimum of one hour with no leakage.
System that contains 50 or more U.S. gallons should have a tee fitting with a stopcock installed in the return
line close to the chiller. The stopcock can be opened and attached to a hose with a female X female hose
fitting. In the open end of the hose section (1 -1.5 feet long) insert a funnel and pour into the system the
diluted Propylene Glycol/liquid solution mixture or add water first and then the quantity of Propylene Glyco
needed for minimum ambient protection (refer to Table 6). After adding the Propylene Glycol /water mixtur
or liquid solution and then coolant proceed to add enough water to the system to achieve a 15 psi gauge
pressure. To measure system pressure shut off the stopcock, remove hose and attach a water pressure gauge.
Open the stopcock to read system pressure.
Systems that use the Chilled Liquid Solution Storage Tank should be filled at the tee/stopcock fitting in the
outlet fitting of the storage tank. Fill the tanks with 10 gallons of water and with a funnel pour the calculated
(refer to Table 6) amount of Propylene Glycol into the tank. The amount of Propylene Glycol added should
be calculated to achieve minimum ambient protection. After adding Propylene Glycol, fill the system with
enough liquid solution to bring system pressure to approximately 15 psi gauge pressure. To measure system
pressure shut off the stopcock and attach a water pressure gauge. Open the stopcock to read system
pressure.
Since we have the system filled we must eliminate the air left in the system. Briefly open each bleed valve a
the air handlers and allow trapped air to escape. This will eliminate much of the air left in the system.
Next we will start the pump and continue bleeding air from the system. Be sure the chiller has line voltage
available to it and set the chilled liquid solution control up to 100°F, which will ensure that only the pump ru
at this point. The pump should now start and remain running. Should the pump stop at any time during this
process it is an indication that the flow switch had air move across it allowing the circuit to be interrupted.
Continue to bleed some air out of the system at the highest locations before resetting the pump bypass timer
to get the pump running again. Open and close the power supply switch to the chiller to restart the pump.
Continue bleeding air with the pump operating. You may have to start and re-start the pump a few times to
complete air removal.
All piping systems should have a minimum of 10% Propylene Glycol in the system even in climates with no
freezing ambient temperatures.
Using less than the recommended Propylene Glycol percentage content voids equipment warranty.
Liquid solution control valves (solenoid or motorized valves) should be selected for low pressure drop. If a
selected valve contributes to pushing your total head calculation to more than 50 feet of head, a larger valve
may be needed to bring your total head below the maximum of 50 feet.
Air Elimination
30
Filling System with Liquid Solution and Coolant
(Propylene Glycol)