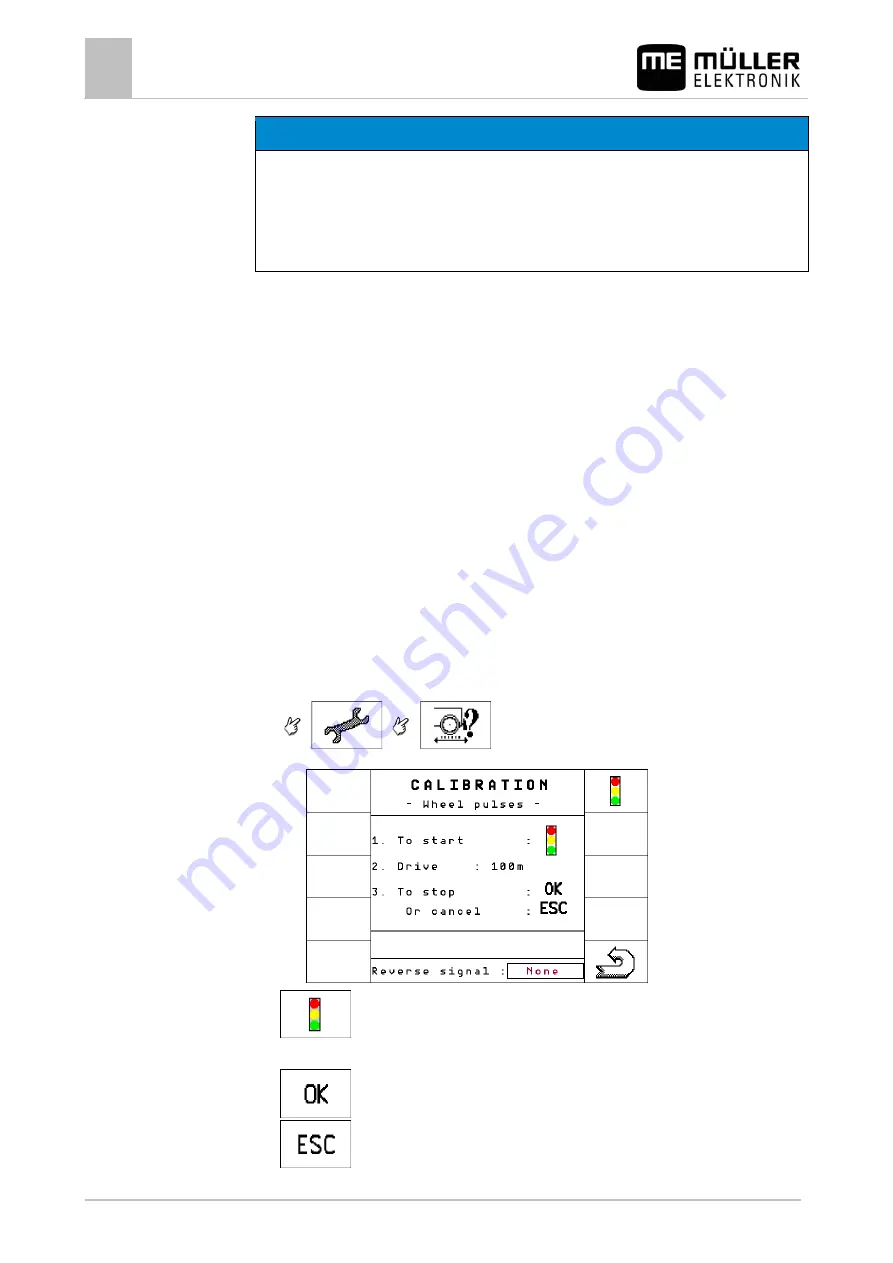
6
Configuring TRAIL-Control
Configuring the speed sensor
30
V2.20160912
30322332-02-EN
NOTICE
Imprecise calibration
The speed cannot be precisely determined with an incorrectly calibrated wheel sensor.
As a result, all the calculations of the applied area, the traveled distance and the volume applied will
be highly imprecise.
◦ Calibrate the wheel sensor very precisely.
Determining the pulses per 100 meters
When calibrating the wheel sensor with the 100m method, you determine the number of pulses
received by the sensor over a distance of 100 meters.
In order for the system to function correctly, the wheel sensor must receive at least 250 pulses over a
distance of 100 meters.
To increase the number of pulses, you must install additional magnets opposite of the wheel sensor.
If you know the number of pulses for the wheel sensor, you can also enter this number manually.
Wheel sensor is installed.
All wheel sensor magnets are fully functional.
A distance of 100m has been measured and marked. The distance must correspond to the field
conditions. It should therefore lead over a meadow or a field.
The tractor with connected implement is operational for a 100m drive and is positioned at the
start of the marked distance.
1.
Ensure that all prerequisites have been fulfilled.
2.
Switch to the "CALIBRATION – wheel pulses" screen:
⇨
The following screen appears:
3.
- Start calibration.
4.
The following function icons appear:
- Stop calibration.
- Abort calibration.
6.4.2
Procedure