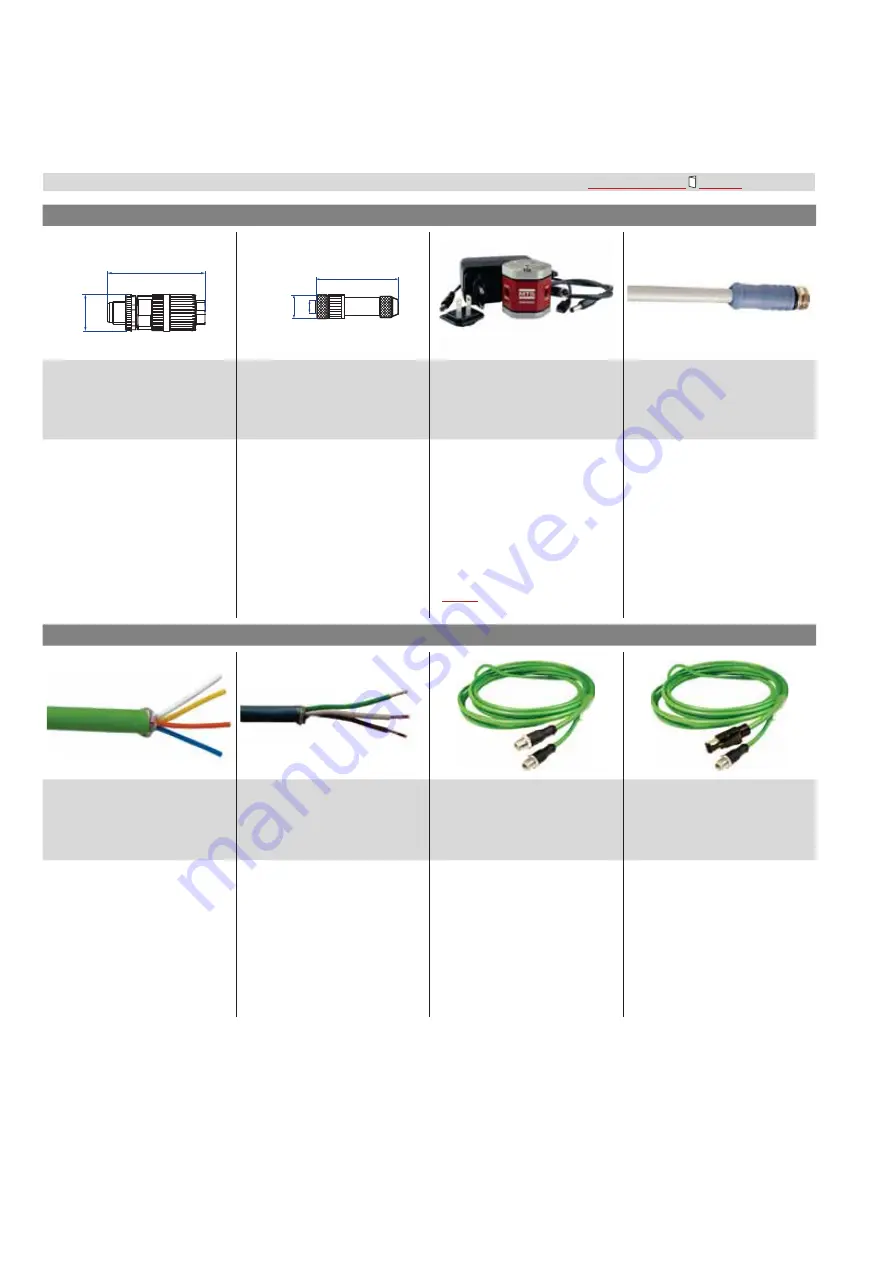
Temposonics
®
R-Series
V
POWERLINK
Operation Manual
I 20 I
4.10 Frequently ordered accessories for POWERLINK output
– Additional options available in our
Accessories Guide
551 444
&DEOHFRQQHFWRUV
3URJUDPPLQJNLW
&DEOHV
52
(2.05)
Ø 19.5
(Ø 0.77)
43
(1.7)
Ø 12
(Ø 0.47)
M8
6LJQDOFRQQHFWRU0'FRGHGPDOH
SLQVWUDLJKW
3DUWQR
3RZHUFRQQHFWRU0IHPDOH
SLQVWUDLJKW
3DUWQR
7HPSR/LQNNLWIRU7HPSRVRQLFV
®
56HULHV
V
3DUWQR7/(0IRU'
3RZHUFDEOHZLWK0IHPDOHFRQQHFWRU
SLQVWUDLJKWŋSLJWDLO
3DUWQRPIW
3DUWQRPIW
3DUWQRPIW
Material: Zinc nickel-plated
Termination: Insulation-displacement
&DEOHĽPPĽLQ
:LUH$:*ŋ$:*
Operating temperature:
ũĽŹ&ũĽŹ)
Ingress protection: IP65 / IP67
FRUUHFWO\ğWWHG
Fastening torque: 0.6 Nm
Material: CuZn nickel plated
Termination: Solder
&DEOHĽPPĽLQ
Wire: 0.25 mm2
Operating temperature:
ũĽŹ&ũĽŹ)
,QJUHVVSURWHFWLRQ,3FRUUHFWO\ğWWHG
Fastening torque: 0.5 Nm
• Connect wirelessly via Wi-Fi enabled
device or via USB with the diagnostic
tool
• Simple connectivity to the sensor
via 24 VDC power line (permissible
cable length: 30 m)
• User friendly interface for mobile
devices and desktop computers
• See product brief “TempoLink
smart assistant” (document part no.:
551976
) for further information
Material: PUR jacket; gray
Features: Shielded
&DEOHPPLQ
Operating temperature:
ũĽŹ&ũĽŹ)
&DEOHV
385VLJQDOFDEOH
3DUWQR
39&SRZHUFDEOH
3DUWQR
6LJQDOFDEOHZLWK0'FRGHGPDOH
FRQQHFWRUSLQVWUDLJKWŋ0
'FRGHGPDOHFRQQHFWRUSLQ
VWUDLJKW
3DUWQR
6LJQDOFDEOHZLWK0'FRGHGPDOH
FRQQHFWRUSLQVWUDLJKWŋ5-
PDOHFRQQHFWRUVWUDLJKW
3DUWQR
Material: PUR jacket; green
)HDWXUHV&DWKLJKO\ĠH[LEOHKDORJHQ
free, energy chain capable, mostly oil &
ĠDPHUHVWLVWDQW
&DEOHPPLQ
Cross section: 2 × 2 × 0.35 mm
2
$:*
Operating temperature:
ũĽŹ&ũĽŹ)
Material: PVC jacket; gray
)HDWXUHV6KLHOGHGĠH[LEOH
PRVWO\ĠDPHUHVWLVWDQW
&DEOHPPLQ
Cross section: 3 × 0.34 mm²
Bending radius: 10 × D
Operating temperature:
ũĽŹ&ũĽŹ)
Material: PUR jacket; green
Features: Cat 5e
Cable length: 5 m (16.4 ft)
&DEOHPPLQ
Ingress protection: IP65, IP67, IP68
FRUUHFWO\ğWWHG
Operating temperature:
ũĽŹ&ũĽŹ)
Material: PUR jacket; green
Features: Cat 5e
Cable length: 5 m (16.4 ft)
&DEOHPPLQ
Ingress protection M12 connector:
,3FRUUHFWO\ğWWHG
Ingress protection RJ45 connector:
,3FRUUHFWO\ğWWHG
Operating temperature:
ũĽŹ&ũĽŹ)
Follow the manufacturer‘s mounting instructions
&RQWUROOLQJGHVLJQGLPHQVLRQVDUHLQPLOOLPHWHUVDQGPHDVXUHPHQWVLQDUHLQLQFKHV