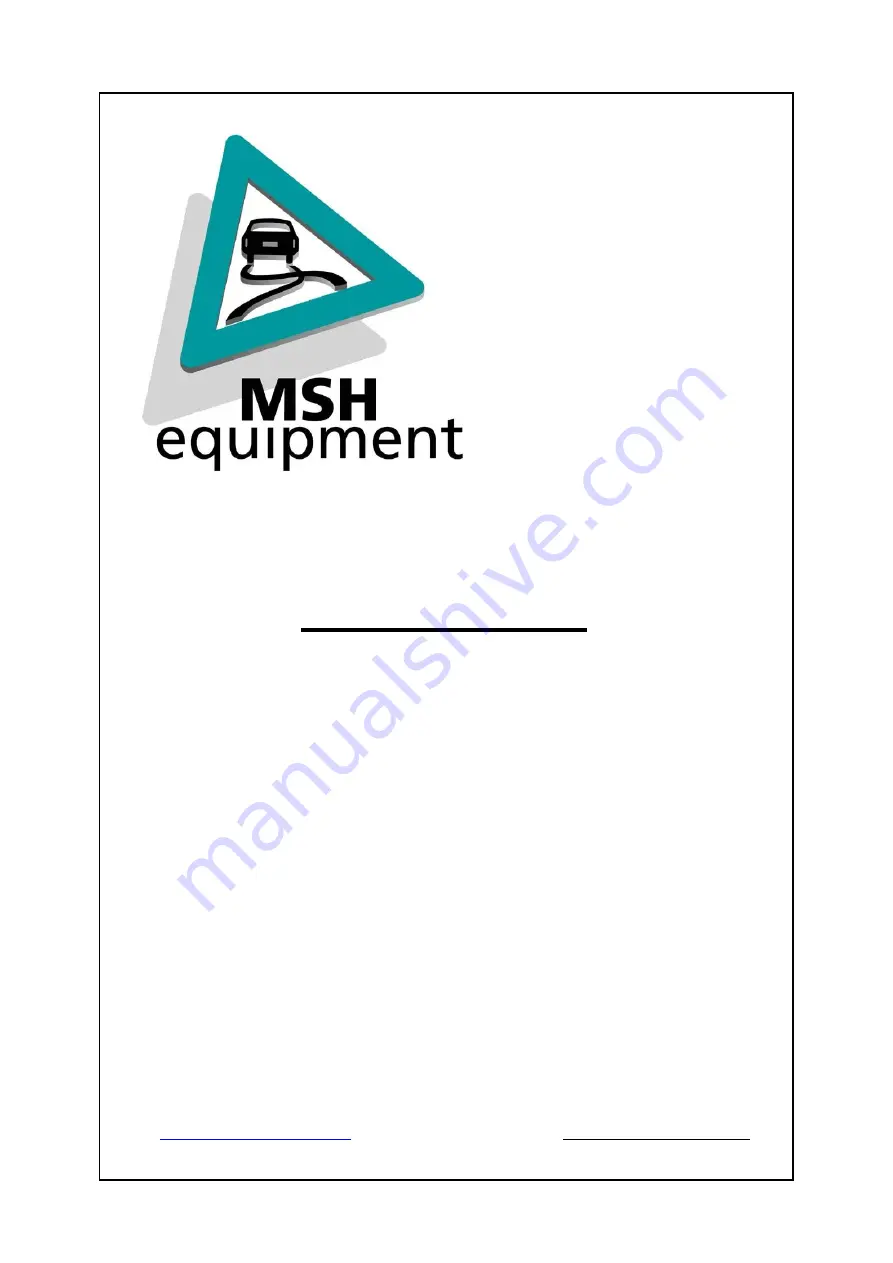
Handleiding
Effemme
EF WizUP30I - Schaarbrug dorpelopname Wiz
UP30 Inbouw
EZ WizUP30FL- Schaarhefbrug dorpelopname
Wizard UP30F
MSH equipment
Appelmarkt 7
1681 PE Zwaagdijk-Oost
Tel: 0228-561100
Fax: 0228-561112
Mail:
Website:
www.msh-equipment.nl
Taal: engels
Summary of Contents for WIZARD UP 30
Page 9: ...Wizard Up30 Rev 4 28 04 2017 8 OVERALL DIMENSIONS Pic 6 ...
Page 10: ...Wizard Up30 Rev 4 28 04 2017 9 Pic 6 ...
Page 11: ...Wizard Up30 Rev 4 28 04 2017 10 Pic 6 ...
Page 12: ...Wizard Up30 Rev 4 28 04 2017 11 Pic 6 ...
Page 19: ...Wizard Up30 Rev 4 28 04 2017 18 ELECTRIC SYSTEM CONNECTION THREEPHASE Pic 11 ...
Page 20: ...Wizard Up30 Rev 4 28 04 2017 19 Pic 11a ...
Page 22: ...Wizard Up30 Rev 4 28 04 2017 21 Pic 12 14 mm 14 mm ...
Page 30: ...Wizard Up30 Rev 4 28 04 2017 29 Pic 16 ...
Page 31: ...Wizard Up30 Rev 4 28 04 2017 30 ...
Page 33: ...Wizard Up30 Rev 4 28 04 2017 32 ...
Page 34: ...Wizard Up30 Rev 4 28 04 2017 33 CONTROL BOX Pic 20 a Pic 20 b 33 23 24 25 1 29 3 18 22 32 16 ...