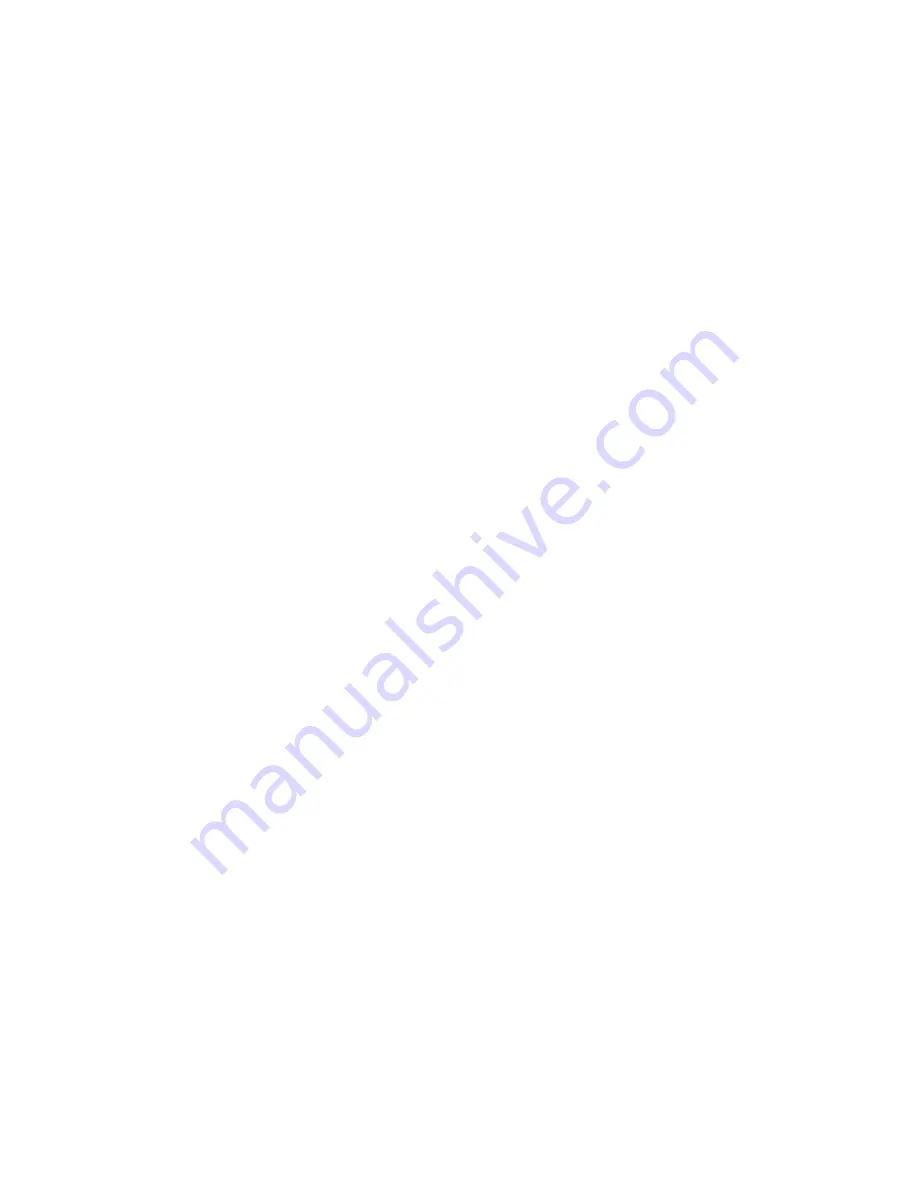
10
MS
HORNET
II
Assembly
Instructions
Thank
you
for
purchasing
a
Hornet
Micro
Helicopter
with
collect
ive
pitch
control.
Hornet
II
uses
CCPM
mixing
system,
and
your
transmitter
must
have
this
mixing
built
in
to
operate
the
Hor-
net
II.
Hornet
II
is
designed
for
a
wide
range
of
RC
heli
pilot
s
–
from
beginners
to
advanced.
T
o
ensure
you
get
the
best
from
your
Hornet,
please
follow
thes
e
instructions
carefully
.
W
e
recom-
mend
that
you
take
the
time
to
read
the
assembly
instructions
thoroughly
BEFORE
starting
to
build
the
Hornet.
W
ARNING:
This
RC
model
helicopter
is
not
a
toy
.
The
ro
tating
parts
repr
esent
an
instant
sour
ce
of
danger
.
Never
use
br
oken
par
ts,
replace
even
if
you
only
suspec
t
the
part
might
be
not
in
a
perfect
condition.
Use
the
model
only
in
places
suitable
for
flying.
Parts/Items
required
for
building
the
Hornet
1
)
CyanoAcrylate
Glue
[CA]
–
we
recommend
a
medium
to
thick
vers
ion
2
)
CA
De-Bonder
for
easy
removal
of
parts
requiring
replacement
3
)
A
small
flat
face
screwdriver
4
)
Metric
allen
keys
5
)
A
pin
or
needle
for
the
application
of
CA
glue
in
precise
amo
unts
and
areas
6
)
Soldering
iron
&
solder
Electronic
components
required
for
H
ornet
operation
1
)
5CH
to
7
CH
Micro
Receiver,
for
example
MS-017,
MS-018
or
-01
9.
2
)
MS-024
Digital
Piezo
Micro
Gyro
or
equivalent
3
)
MS-055
Speed
controller
5,5A
with
BEC
or
equivalent
4
)
MS-006
Micro
Servo
MS-15
or
equivalent
-
4
pcs
5
)
Standard
receiver
crystal
6
)
Accu
8,4-9,6V/600-700mAh,
for
example
MS-009,
MS-030
or
MS-03
1
Recommended
Accessories
1
)
MS-008
NiMH
Fast
Charger
50-1500
mAh
2
)
MS-012
Charger
Lead
IMPOR
TANT
–
apply
the
CA
glue
using
a
pin
or
needle.
This
will
ensure
accurate
application
of
the
glue
onto
the
parts
to
be
glued
and
will
avoid
excess
being
used.
CA
glue
will
bond
skin
in
seconds,
please
read
the
label
on
the
CA
glue
for
further
information.
Many
parts
used
in
the
Hornet
are
small;
use
a
container
to
hol
d
the
component
pieces
until
they
are
needed
in
the
construction.
1.
–
Main
Body
Assembly
Parts
List:
E401
–
Main
Frame
x
1
E403
–
Frame
Support
x
1
E406
–
Undercarriage
Legs
x
2
E087
–
Undercarriage
Skids
x
2
E008
–
Anti-rotation
Support
x
1
E050
–
Nut
M1.6
x
2
E402
–
Frame
Base
x
1
E014
–
Canopy
Support
Upper
50
mm
x
1
E009
–
Anti
Rotation
pin
23
mm
x
1
L0360
–
Ball
Bearing
3
x
6
x
2
x
2
E055
–
Bolt
M2x8
x
4
E
405
–
Bolt
M1.6x6
x
2
E056
–
Nut
M2
x
4
E404
–
Link
Ball
x
2
Follow
the
pictures
for
Step
1.
1)
Fit
the
Ball
Races
L0360
into
the
Main
frame
E401
-
one
in
the
top
and
one
in
the
bottom.
2)
Assemble
and
glue
the
Anti-Rotation
Pin
E009
to
the
Anti-Ro
tation
Support
E008
as
shown.
3)
Glue
the
assembled
Support
to
the
Main
Body
E001.
The
Suppor
t
Pin
should
be
orientated
180°
15
2)
Press
the
holes
into
the
Canopy
using
a
needle
from
the
insi
de
out
on
marked
places.
Y
ou
can
add
small
drops
of
CA
at
the
end
of
the
canopy
support
to
ensur
e
tighter
canopy
fixing.
3)
T
o
complete
use
Stickers
E461.
HORNET
II
SETUP
AND
ADJUSTMENT
1)
Program
the
transmitter
for
the
corresponding
heli
mix
progr
am
–
HR3
or
SR3
(for
Futaba
transmitters),
or
equivalent
for
other
transmitter
types.
2)
Set
up
the
servo
reversing,
so
the
Swashplate
movements
corr
espond
to
the
stick
movements.
See
pics.
2
and
4.
3)
Set
up
the
Swashplate
servos’
deflections.
If
the
recommende
d
horn
length
has
been
used,
for
MS-15
and
MS-10
servos
use
values
of
60%
for
elevator
and
roll
and
30%
for
pitch.
NOTE:
When
increasing
the
positive
pitch,
the
Swashplate
moves
down.
4)
Check
again
the
Connecting
Rod
lengths.
In
neutral
servo
pos
itions
(don’t
forget
to
reset
the
trims)
the
Swashplate
must
be
perpendicular
to
the
Main
Rotor
S
haft,
the
Main
Blades
pitch
must
be
0°
and
the
Stabilizer
Paddles
pitch
must
be
0°
as
well.
The
throttle
stick
should
be
at
50%
(central
stick
position)
during
this
check.
Furthermore,
check
the
servo
horns,
which
must
be
horizontal.
See
Pic.
2.
5)
To
check
the
Blade
pitch,
use
the
included
Pitch
Gauge.
6)
Pitch
Gauge
Usage:
Cut
off
and
bend
both
halves
of
the
Pitch
Gauge
as
shown
in
the
picture.
Pay
attention
to
cutting
as
precisely
,
as
you
can
–
the
resulting
setting
accuracy
depends
on
the
accuracy
of
the
Pitch
Gauge.
Put
both
pitch
gauge
parts
on
the
square
part
of
the
Blade
Grips,
keeping
the
gap
between
the
scales
as
small
as
possible.
The
pi
tch
can
be
read
on
the
scale.
7)
Set
the
Tail
Rotor
Pushrod
length
so
the
pitch
shown
in
the
pic.
3
is
achieved.
The
servo
is
in
neutral
position.
After
setup,
CA
the
other
Servo
Link
to
the
P
ushrod.
8)
Set
up
the
REVO
mix
corresponding
to
your
preference
and
to
your
gyro
settings.
REVO
mix
can
be
set
up
to
compensate
for
changing
torque
when
changing
the
Main
Blades’
pitch.
9)
The
maximal
possible
pitch
angle
depends
on
the
Gear
Ratio
chosen,
the
Motor
and
Battery
used.
If
the
Standard
Motor
and
Battery
pack
are
used,
and
the
medium
Gear
Ratio,
i.e.
pinion
with
11
teeth,
the
maximum
pitch
angle
can
be
set
to
10°.
The
exact
setup
can
be
done
only
by
flight
testing.
T
oo
much
pitch
will
cause
significant
shortenin
g
of
the
flight
time,
and
can
lead
to
overload
of
the
Motor
and
Speed
Controller
.
This
situation
can
result
in
no
power
reserve
at
a
critical
time.
W
e
recommend
performing
the
flight
tests
and
pit
ch
setup
with
a
Battery
only
char
ged
to
50%
capacity
,
to
ensure
the
pitch
angle
will
be
enou
gh
to
fly
when
the
battery
is
partially
discharged.
The
maximum
positive
pitch
angle
is
limit
ed
to
+15°,
which
is
sufficient
reserve
for
autorotation
landings.
T
o
perform
autorotations,
MS
-230
upgrade
set
must
be
in-
stalled.
The
minimum
pitch
angle
is
limited
by
length
of
the
E0
15
joints.
For
inverted
flight
this
should
be
–10°.
For
normal
flight
modes
we
recommend
the
negati
ve
pitch
angle
to
be
set
at
–2°
to
–3°,
to
allow
safe
and
stable
flight
descent.
For
autorotati
on,
the
angle
can
be
increased
to
–
5°.
10)
The
Rotor
Blades
are
fixed
to
the
Blade
Grips
using
Bolts
E
078,
which
should
be
not
over
tightened.
11)
The
Blade
tracking
must
be
performed
in
the
hover
as
a
part
of
initial
heli
setup.
Check
if
the
Main
Rotor
Blades
follow
one
track.
If
not,
correct
it
by
chang
ing
the
length
of
the
Pitch
Connecting
Rod.
For
the
low
running
Blade,
the
Rod
must
be
exte
nded
(and
vice
versa).
If
you
are
unable
to
determine
which
Blade
is
lower,
just
try
and
exte
nd
one
of
the
Rods.
Make
the
correction
slowly
–
by
a
half
turn
only
.
If
it
gets
worse,
exte
nd
the
Connecting
Rod.
T
ry
it
until
the
Blades
track
properly
.
T
roubleshooting
If
you
experience
tail
control
problems,
often
the
reason
is
th
e
control
system
being
too
tight.
The