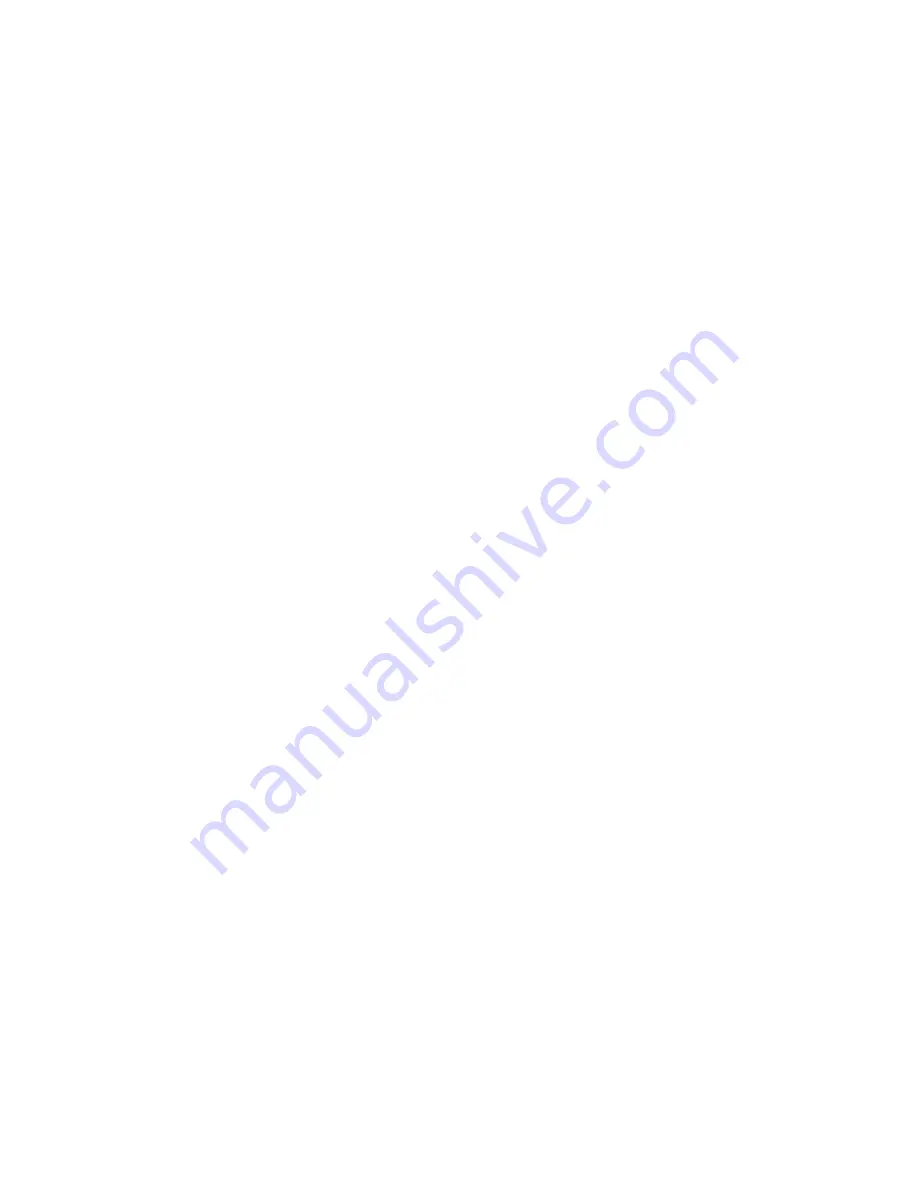
10
SECTION 6
VACUUM OPERATION
6.1
A pump with a pumping capacity four times greater than the chamber volume is
commonly used. When working below vacuums of 1mm, a diffusion type pump will
be needed. See Section 9.0 for chamber capacities
6.2 IT IS IMPORTANT TO USE VACUUM TUBING FOR ALL THE VACUUM
HOOKUPS. OTHER TYPES OF TUBING MAY COLLAPSE AND PREVENT
COMPLETE EVACUATION.
6.3
To Apply Vacuum To The Chamber:
Attach the hose from the vacuum pump to
the 3/8" hose connection on back of the oven. Close the VENTILATION valve
(clockwise) and open the VIDE valve. Latch the door shut and start the vacuum
pump. This action will hold the door shut and against the gasket until the pump
creates a vacuum in the chamber. Once a good vacuum seal is accomplished, the
door will hold itself shut and sealed until the chamber is returned to atmospheric
pressure.
6.4
Watch
the
VACUUM GAUGE
and when the required vacuum is obtained, close the
VACUUM valve and turn pump off. The VACUUM GAUGE is calibrated from 1 to
900 millibars with 1013 millibars representing atmospheric pressure. The oven can
be evacuated to pressures as low as 10 microns.
6.5 Vacuum
Release:
To return the chamber to atmospheric pressure, open the
VACUUM valve very slowly and allow the chamber to re-pressurize. The speed of
pressurizing can be controlled by how much the valve is opened.
NOTE: A 1 inch sealed pipe is provided at the back of the unit. This access port
can be used to plumb the chamber to a larger, faster roughing pump or as a conduit
for other service applications. Any use of this pipe requires the operator to assure
the attachment is vacuum tight.