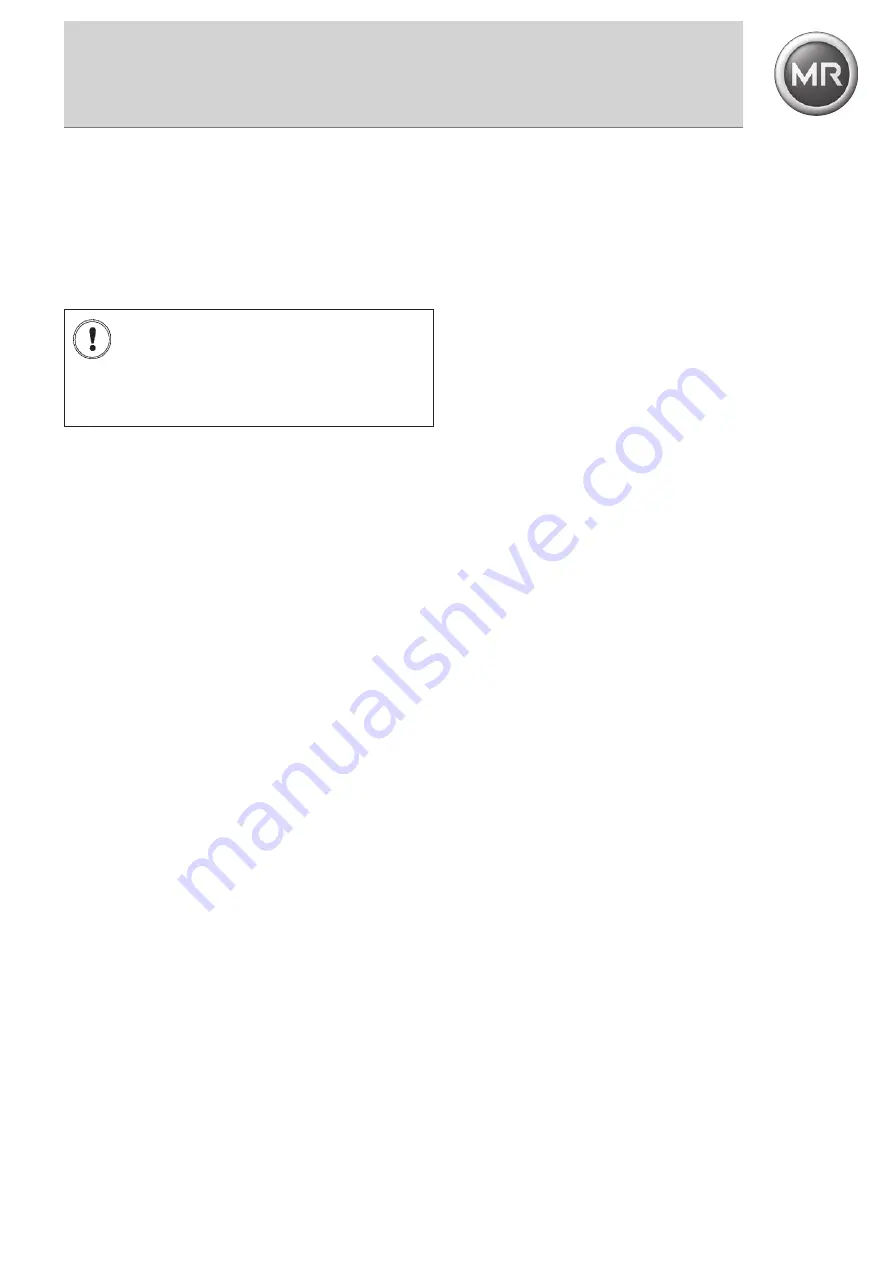
23
251/02 en
6
Parallel operation
6.1.4
Function tests, commissioning
6.1.4.1 Preliminary settings
The current transformer inputs must be connected and the
transformer configuration must be parameterised correctly.
The voltage regulators must be set to identical operating
parameters for the desired voltage, bandwidth, time delay 1,
and line compensation, if applicable (LDC or Z Compensation,
respectively).
In all cases, set STABILITY to "0“ and Blocking to "20“.
During parallel operation, time delay 2 must never be set
below 8 s!
All settings must be performed in the "Manual“ operating
mode.
6.1.4.2
Setting the interference variable
(
CIRCUL. REAC. CURR.
STABILITY)
Individually set both transformers to identical voltage with
the on-load tap-changers so that both voltage regulators are
in a balanced state (no presignal LED are lighting up, the
indication of "dU %" must be as low as possible, i. e. lower
than the preset bandwidth "dU max").
Now switch the transformers to parallel operation and enable
parallel control (connect terminal 90/91).
The voltage regulators must continue to remain in a balanced
state, the LED lamp "parallel operation" on the front panel is
lighting up.
Raise one of the two transformers by one voltage step and
lower the other of the two transformers by one voltage step.
Both regulators must continue to remain in a balanced state.
Raise the setting value "CIRC.REAC.CURR.STABILITY" of both
regulators in small steps starting with "0" until the corres-
ponding presignals appear (the regulator of the transformer
with the higher voltage step must show the tendency "lower"
while the other transformer must show the tendency "raise“).
Now add the setting values thus established and set the
added-up value for both regulators.
Select the "Auto" operating mode for both voltage regula-
tors. Both voltage regulators must control the on-load tap-
changers back into their previous service positions.
The presignals will go out.
NOTE
The prerequisite for the proper functioning of parallel
operation is the commissioning of the voltage regulators
for individual operation.
6.1.4.3
Setting the circulating reactive current
monitoring
(CIRCUL. REAC. CURR. MON.
BANDWIDTH)
Switch over one of the two voltage regulators to the
"Manual“ operating mode. Using the manual control, the
associated motor drive must now be reset to "Raise“ by the
maximum admissible difference of the service positions
between the parallel operating transformers (e. g. by 1 … 2
steps).
Starting with the preset value of "20 %", reset the blocking
towards a lower value in small steps until the message
"Circulating reactive current" appears in the status line of the
display (please wait 2 – 3 s between the individual steps).
The bandwidth threshold of the circulating reactive current
monitoring is reached as soon as this message appears.
The voltage regulators will block all further regulating actions
and the signalling relay will respond (terminal 83/84/85).
Now reset the blocking again towards a higher value until
the message „circulating reactive current“ disappears from
the status line of the display.
Again switch the voltage regulator back to the "Auto"
operating mode. The motor-drive will be automatically
controlled back to the original service position.
Use the value established for the "Blocking" threshold to set
it for all of the other regulators.
6.2
Parallel operation according to synchronized
tap-change operation Master/ Follower
This method is suitable for transformers featuring an identi-
cal rated current, identical step voltage, and an identical
number of service positions. The motor-drive must signal the
tap-change position by means of a current of 4 … 20 mA
(with 4 mA corresponding to the lowest position and 20 mA
corresponding to the highest position).
During parallel operation, actual voltage regulation is per-
formed by one of the voltage regulators (Master function).
The second voltage regulator (Follower) receives the tap-
change position of the motor-drive from the first regulator,
for comparison with the tap-change position of its own
motor drive. If a difference is noted, the motor-drive in
question will receive a suitable control pulse.
If the previous service position cannot be achieved that way,
the "CIRC.REAC.CURR. STABILITY“ setting needs to be in-
creased. If the on-load tap-changers are regulating out of
sync ("pumping“), this setting needs to be reduced.