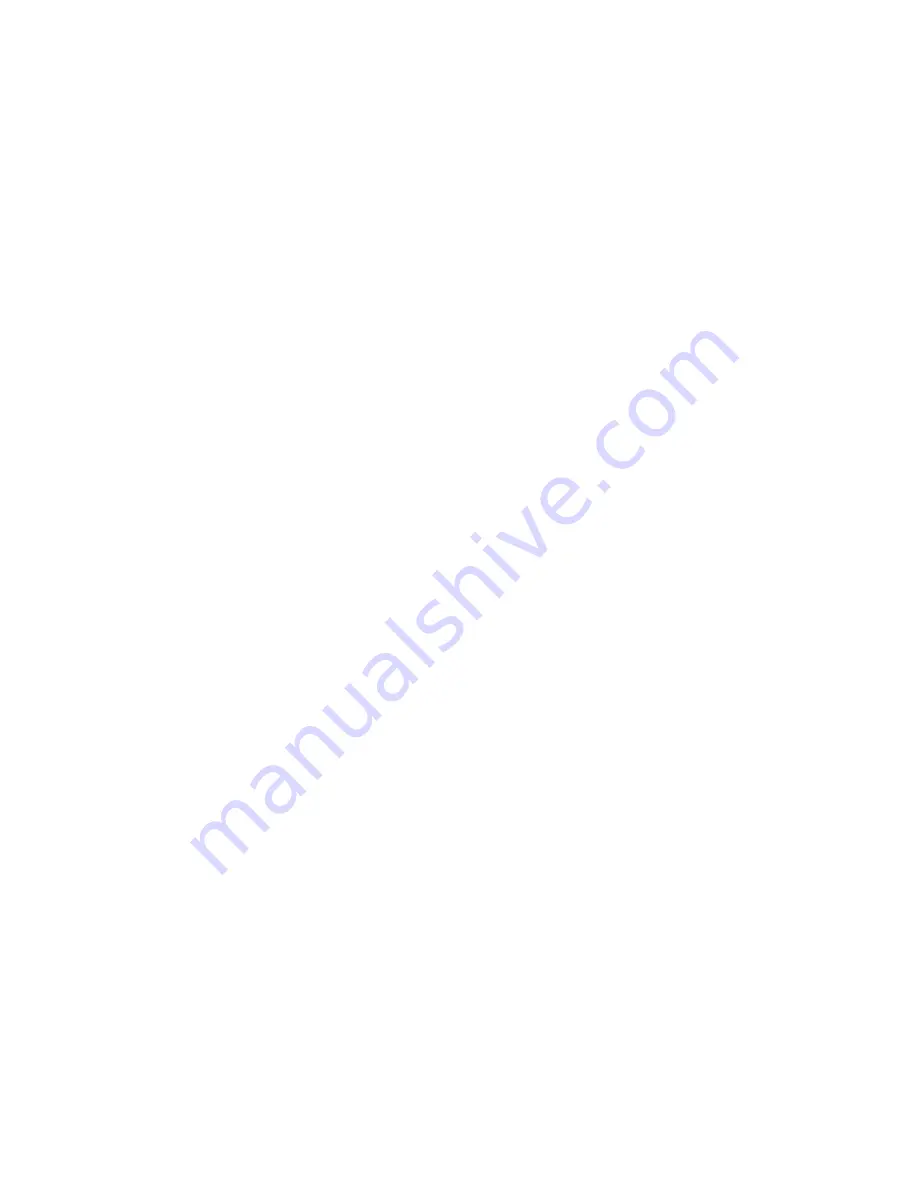
Appendix G
54
New ISO Medium Test Dust and its effect on ISO . . .
ISO therefore defined the requirements for the replacement for ACFTD and
asked the National Institute of Standards and Technology (NIST) in the USA
to produce a standard, traceable reference material. The new dust’s parti-
cle size distribution has been accurately determined with the aid of modern
scanning electron microscope and image analysis techniques.
New Test Dust Benefits
The new ISO Medium Test Dust (ISO MTD) consists of similar materials to
the old ACFTD, but to minimize particle counting errors, it is of a slightly
coarser grade because ACFTD included too many particles smaller than 5µm
which gave problems during testing.
ISO MTD is produced to a standard distribution and stringent quality control
procedures, thereby ensuring excellent batch-to-batch repeatability. These
procedures, combined with a revised ISO APC calibration method give:
•
A traceable and controlled reference test dust with greatly reduced vari-
ation in particle size distribution. This gives the trace-ability required by
ISO 9000, QS9000 and similar quality management systems.
•
A procedure for determining the performance of APCs so that minimum
acceptable levels can be set by the user.
•
Improved calibration techniques and procedures.
•
More accurate calibration.
•
Improved levels of particle count reproducibility with different equip-
ment.
•
More accurate and consistent filter test results.
Effect on Industry
The introduction of ISO MTD has necessitated changes to certain ISO stan-
dards.
Summary of Contents for LPA2
Page 1: ...LPA Analyser UserGuide 200 053 EN www mpfiltri co uk ...
Page 7: ...Introduction 7 ...
Page 40: ...40 Warranty ...
Page 70: ...Appendix L 70 Fault Finding ...