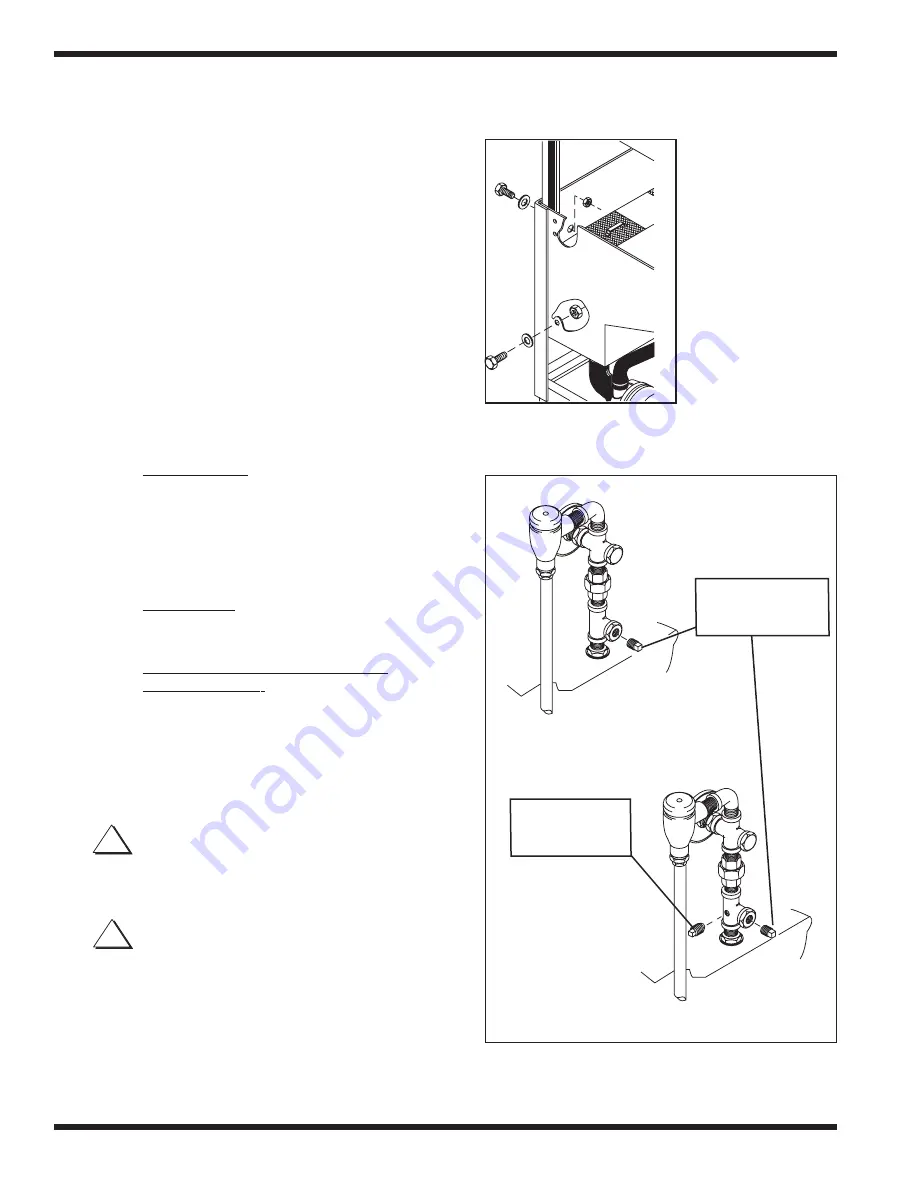
INSTALLATION
10
Chemical Connections (Cont.)
Refer to Fig. 10
5. A 1/2" detergent probe injection point
is provided at the rear and left side of
the dishwasher.
6. Detergent may be added manually if
your dishwasher is not equipped with
dispensing equipment. Consult your
chemical supplier for recommended
amounts.
Refer to Fig. 11
7.
MH-60, 6N, 6L
A 1/4" NPT rinse aid injection point is
provided in the final rinse manifold.
Use a liquid rinse aid.
The manifold is located on the top right
side of the dishwasher.
8.
MH-6L Only
A 1/8" NPT sanitizer injection point is
provided in the final rinse manifold.
Models MH-60 and MH-6N do not
require sanitizer.
9. Use a sodium hypochlorite (Chlorine)
based sanitizer at a minimum
concentration of 50PPM in the final rinse.
10. Use chlorine test papers to verify and
monitor the 50PPM chlorine level.
WARNING:
Never premix rinse aid with the
sanitizing agent. Mixing may cause
hazardous gases to form.
CAUTION:
Some metals, including silver, aluminum
and pewter, are attacked by sodium
hypochlorinte (chlorine). Avoid cleaning
these metals in a MH-6L.
Figure 10
Detergent Probe
Injection Points, 1/2"
Figure 11
Rinse Aid and
Sanitizer Injection Points
(Top of Dishwasher)
!
!
MH-60, 6N
1/4" NPT rinse-aid
injection point
Model MH60, 6N, 6L
1/8" NPT sanitizer
injection point
Model MH6L Only
Summary of Contents for MH-60M5
Page 6: ...iv THIS PAGE INTENTIONALLY LEFT BLANK...
Page 8: ...THIS PAGE INTENTIONALLY LEFT BLANK vi...
Page 39: ...REPLACEMENT PARTS 31 REPLACEMENT PARTS...
Page 72: ...Figure 36 Dishracks and PRV REPLACEMENT PARTS 64 1 2 3...
Page 74: ...THIS PAGE INTENTIONALLY LEFT BLANK 66...
Page 75: ...67 ELECTRICAL SCHEMATICS...