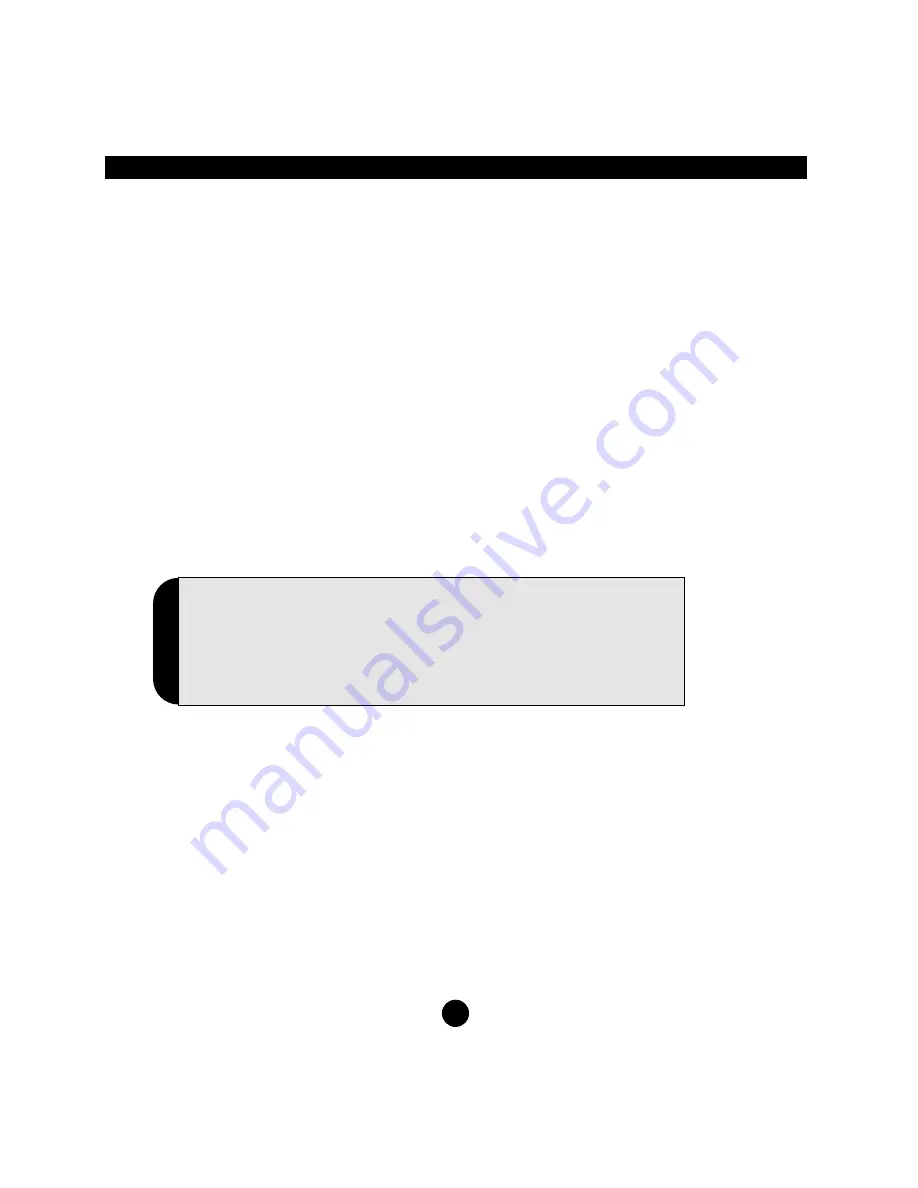
Transducer
Calibration
• Always calibrate the TorqueMate® Plus with the unit plugged into the AC power adapter and make
sure the batteries are fully charged.
• Calibration data for up to 15 transducers can be memorized by the TorqueMate® Plus.
There are two options available for calibrating a transducer:
1. FAST
- Fast Cal means that you do not use dead weights for calibration. The TorqueMate® Plus will
assume the mv/v signal entered is accurate and automatically span the range of the transducer and
store it in memory.
2. TRUE
- True Cal means that you use calibration arms and dead weights to calibrate the transducer.
The TorqueMate® Plus will take three readings in each direction and create a calibration table in
memory.
Procedure for Calibration
Attach the transducer to be calibrated.
• Enter Set-up by pressing the Mode and Tolerance keys at the same time. The Set-up icon will show
and the display will be blank.
• Press the Scroll Up key until the LCD shows CAL.
• Press Enter to select this option.
• The Units icon will be flashing.
• Press the Scroll Up key to select the units that you will be calibrating this transducer to. Press Enter to
select the Units.
• The display will now show the expected transducer number (c-1 to c-15). Press the Scroll Up key
until the desired transducer number is displayed. If the TorqueMate® Plus transducer number has
never been used it will show “3333” for the range (default). This will change as soon as you assign a
range to the transducer. Press Enter to select the proper transducer number.
• Enter the range of the transducer to be calibrated. Press the Scroll Up key to change the value of the
flashing digit. Press the Scroll Right key to select a different digit. When the desired value has been
selected press Enter to accept. Now set the decimal by pressing the Scroll Right key. Press the
Enter key to save the range of the transducer.
Continue the calibration with the steps on page 21.
20
Note: Calibration Security
To ensure that inadvertent alteration of calibration data does not
occur, a Key Sequence Override is required to be entered at the CAL
prompt. After pressing Enter to activate the Cal Menu the Key
Sequence Override is accomplished by pressing Enter, Scroll Right &
Tolerance. Press these keys in exact order to access the calibration
function.
i