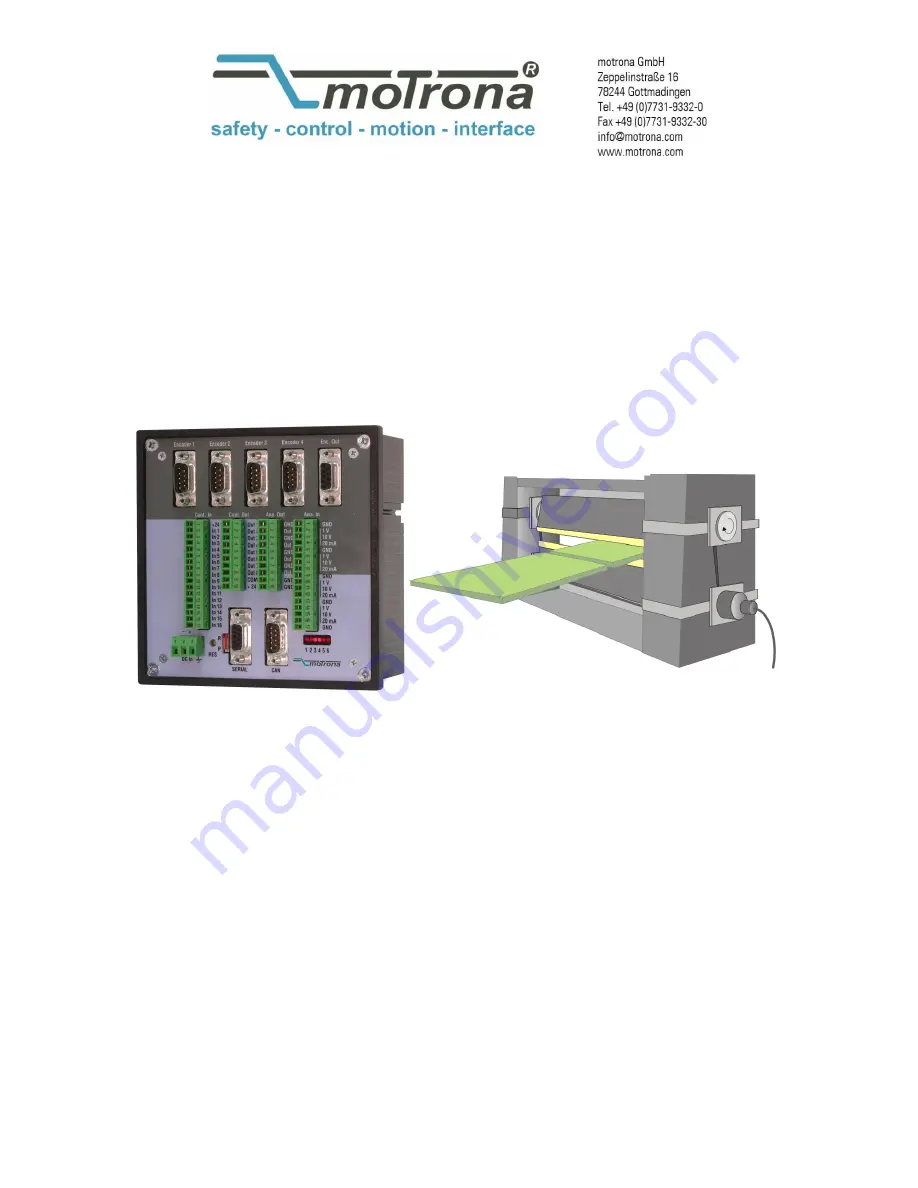
CT70104B_e.doc / Nov-15
Page 1 / 29
CT 701.04
Motion Control Firmware for
Rotary “Guillotine” Shears
with MC700 Controllers
Easy parameter setting instead of sophisticated programming, immediately ready to
work with minimum commissioning time
Synchronous cutting process, with cosine-compensated motion profile during
penetration of the cutting tool
Particularly suitable for “flying cut” of steel plates, sheet metals and profiles
High dynamic response by means of short cycle time
High cutting precision due to
400 kHz of feed-back frequency
Suitable for “stand-alone” operation as well as for connection to field bus systems
(CANBUS, PROFIBUS etc.)
Operating Instructions