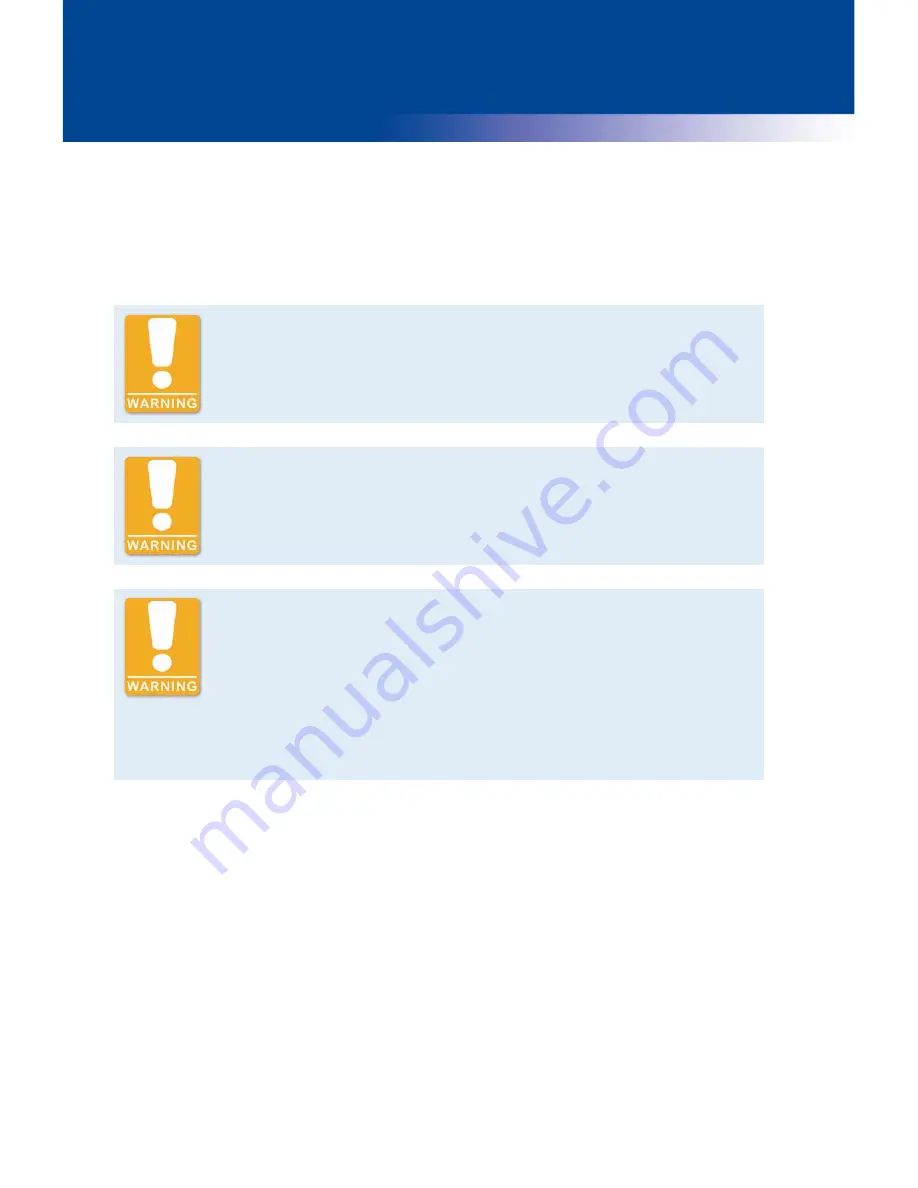
20
Rev. 07/2013
5.1
Installation Instructions
Unpack the stepper motor without damaging it and ensure that the operating manual is always
within reach of the device and easily accessible. Installation locations where strong vibrations
or ambient temperatures of below -15 °C (5 °F) or above 65 °C (149 °F) are present are not
permissible and result in the warranty being voided.
Risk of damage!
The device must not be installed directly on or at the engine, as vibration
and heat may cause damage to electronic components.
Risk of damage!
Please make sure that the device is not covered and ensure sufficient
circulation of air.
Risk of destruction due to electrostatic discharge!
The VariStep stepper motor card may only be installed by specialized
personnel who has been trained in handling ESD sensitive components and
with due regard to relevant ESD standards. It must be installed into a
control cabinet, and it is necessary to comply with the ESD standard
DIN EN 61340-5-1; VDE 0300-5-1:2008-07.
Damages caused by electrostatic discharge are not covered by the
guarantee.
Scope of Supply
The VariStep stepper motor card as supplied consists of the following components:
–
VariStep stepper motor card
–
CD-ROM
–
USB cable
–
Operating manual
Assembly of Control Unit
1.
Please install the control unit on the DIN-rail in the control cabinet.
2.
Please fix the card using the attachment screws on the sides.
5 INSTALLATION INSTRUCTIONS