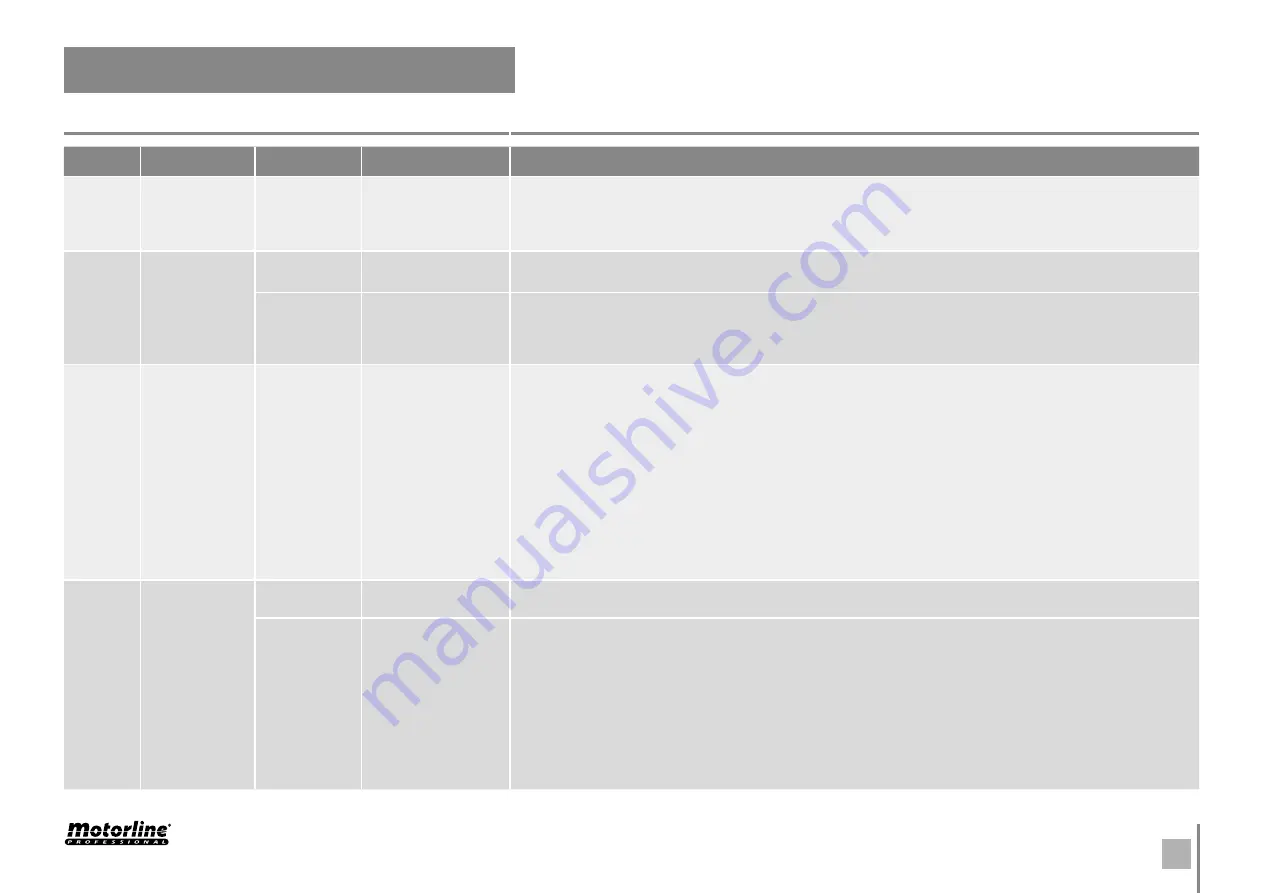
9
EN
SPECIALIZED TECHNICIANS INSTRUCTIONS
05. TROUBLESHOOTING
FINAL CONSUMERS INSTRUCTIONS
Problem
Procedure
Behavior
Procedure II
Discovering the origin of the problem
• Barrier
doesn't work.
• Make sure you
have power in the
automation control
board and if it is
working properly.
• Still not working.
• Consult a qualified
MOTORLINE technician.
• Barrier
doesn’t move
but makes
noise.
• Unlock barrier and
move boom by hand
to check for mechani-
cal problems on the
movement.
• Encountered
problems?
• Consult a qualified
MOTORLINE technician.
1 • Check all motion axis and associated motion systems related with the barrier to find out what is the problem.
• Boom moves
easily?
• Consult a qualified
MOTORLINE technician.
• Barrier
opens but
doesn’t close.
• Unlock motor and
move boom by hand
to closed position.
Lock motor again and
turn off power supply
for 5 seconds. Recon-
nect it and send order
to open barrier using
transmitter.
• Barrier opened but
didn’t close again.
1 • Check if there is any
obstacle in front of the
photocells;
2 • Check if any of the
control devices (key selector,
push button, video intercom,
etc.) of the barrier are jam-
med and sending permanent
signal to control unit;
3 • Consult a qualified MO-
TORLINE technician.
• Barrier
doesn’t make
complete
route.
• Unlock barrier and
move boom by hand
to check for mechani-
cal problems on the
barrier.
• Encountered
problems?
• Consult a qualified
MOTORLINE technician.
1 • Check all motion axis and associated motion systems related with the barrier to find out what is the problem.
• Boom moves
easily?
• Consult a qualified
MOTORLINE technician.
1 • Open control box and check
if it has 230V/110V/24V power
supply;
2 • Check input fuses;
3 • Disconnect barrier from
control board and test them by
connecting directly to power
supply in order to find out if they
have problems (see page 7B).
4 • If the barrier works, the
problem is on the control board.
Pull it out and send it to our
MOTORLINE technical services
for diagnosis;
5 • If the barrier doesn’t work,
remove them from installation
site and send to our MOTORLINE
technical services for diagnosis.
1 • Check capacitors, testing
operator with new capacitor;
2 • If capacitors are not the
problem, disconnect motor from
control board and it them by
connecting directly to power
supply in order to find out if it
has problems (see page 7B).
3 • If the motor works, the
problem is from control board.
Pull it out and send it to our
MOTORLINE technical services
for diagnosis;
4 • If the motor doesn’t work,
remove them from installation
site and send to our MOTORLINE
technical services for diagnosis.
All MOTORLINE control boards
have LEDs that easily allow to
conclude which devices are with
anomalies. All safety devices
LEDs (DS) in normal situations
remain On. All "START" circuits
LEDs in normal situations remain
Off.
If LEDs devices are not all On,
there is some security systems
malfunction (photocells,
safety edges), etc. If "START"
circuits LEDs are turn On, there
is a control device sending
permanent signal.
A) SECURITY SYSTEMS:
1 • Close with a shunt all
safety systems on the control
board (check manual of the
control board in question). If
the automated system starts
working normally check for the
problematic device.
2 • Remove one shunt at a time
until you find the malfunction
device .
3 • Replace it for a functional
device and check if the motor
works correctly with all the other
devices. If you find another one
defective, follow the same steps
until you find all the problems.
B) START SYSTEMS:
1 • Disconnect all wires from
START terminal input (terminal 3
of CN3 connector).
2 • If the LED turned Off, try
reconnecting one device at a
time until you find the defective
device.
NOTE:
In case procedures described in
sections A) and B) don’t result,
remove control board and send
to our technical services for
diagnosis.
1 • Check capacitors, testing
with new capacitors;
2 • If capacitors are not the
problem, disconnect motor
from control board and test it
by connecting directly to power
supply in order to find out if it is
broken;
3 • If the motor doesn’t work,
remove it from installation site
and send to our MOTORLINE
technical services for diagnosis.
4 • If motor work well and move
barrier at full force during the
entire course, the problem is
from controller. Set force using
trimmer on the board. Make a
new working time programming
, giving suffient time for opening
and closing with appropriate
force (page 08.B of this manual
for MBM6 230V).
5 • If this doesn’t work, remove
control unit and send it to
MOTORLINE technical services
services.
NOTE: Setting force of the
controller should be sufficient to
make the barrier open and close
without stopping, but should
stop and invert with a little effort
from a person. In case of safety
systems failure, the barrier shall
never cause physical damaged
to obstacles (vehicles, people,
etc.).