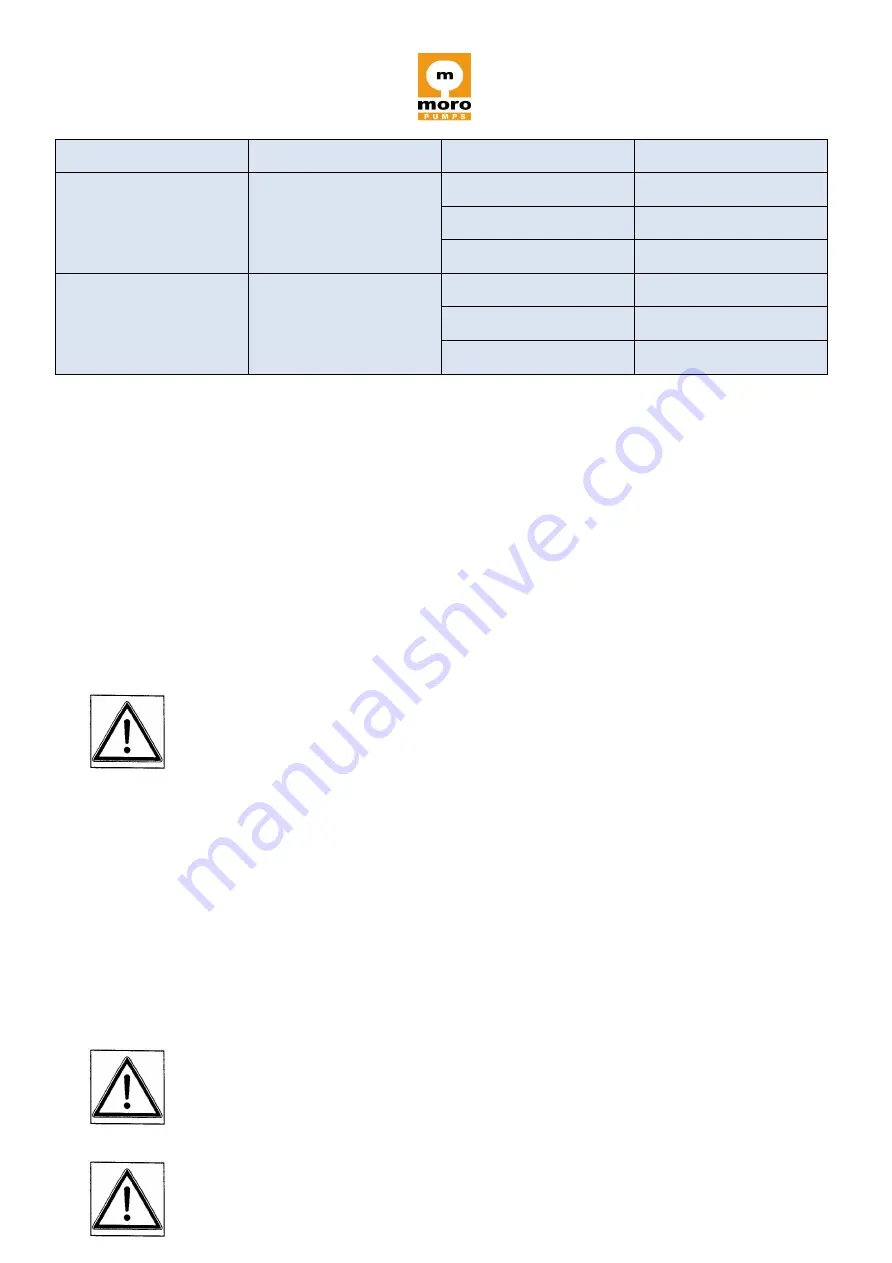
Rev. 00 of 01.01.2009
19 / 29
21.3 / 35.68.
55.62
2”
3.04 sq. in
7.1 / 21.48.
55.16
14.2 / 28.58
73.39
21.3 / 35.68
91.62
2”1/2
(free discharge)
4.37 sq. in
7.1 / 21.48
79.36
14.2 / 28.58
105.59
21.3 / 35.68
131.82
(Table 4)
8. TEST AND RUN-IN
8.1 TEST
To test the vacuum pump, verify the items above, using if necessary a
workbench. Make sure that the PTO shaft rotates freely and that the direction of
rotation is the same as that indicated by the arrow.
Verify that the position of the switch lever is correct and that the vacuum pump
intakes and exhausts air freely.
8.2 RUN-IN
The run-in period of the vacuum pump is about 50 hours of operation.
9. START-UP, OPERATION, STOP
9.1 START-UP
The vacuum pump is not provided with a start switch. To start it, just transmit the drive to the
shaft differently, according to the version of the vacuum pump.
Make sure, prior to starting, that the pump has been filled with oil both in the oil tank for
internal lubrication (all pumps) and in the drive side gearbox (version AM).
Before starting the vacuum pump, make sure that the guards of all the moving
parts are in place and in proper working order. Any damaged or missing part
must be replaced and correctly installed before using the pump.
9.2 OPERATION
Do not use the vacuum pump with pressure, temperature, speed and time values