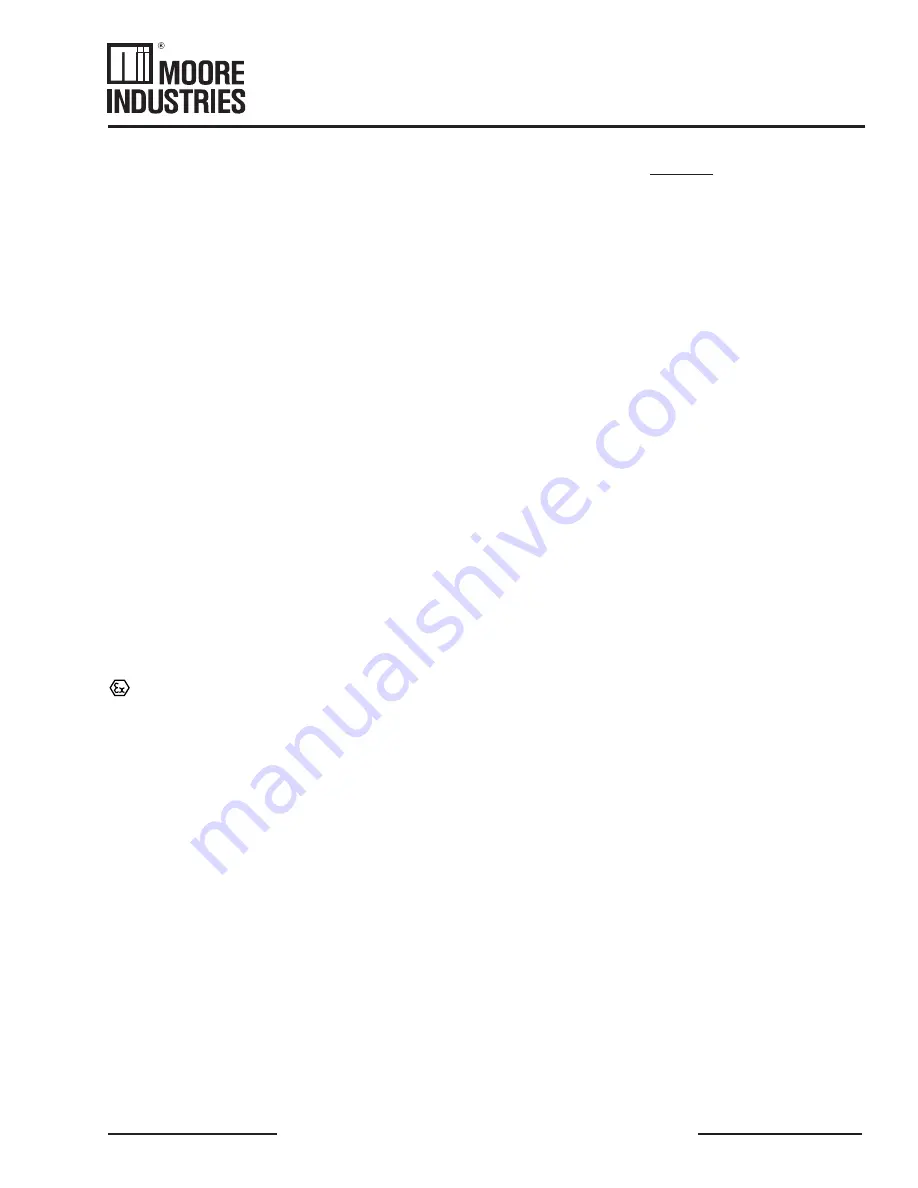
User’s Manual Supplement
Physical Instructions for Installing an
Encapsulated Hockey-Puck (HPP) Instrument
and LH2 Field-Mount Enclosure Apparatus
The Interface Solution Experts
• www.miinet.com
700-764-00A
January 2001
The Physical Instructions Supplement provides
references and additional information for safely installing
and commissioning a Moore Industries’ Hockey-Puck
instrument and LH2 Field-Mount Enclosure Apparatus.
Instrument Labeling and Identification
—The fully
assembled apparatus consists of a Moore Industries’
Hockey-Puck unit securely mounted in an LH2
enclosure. Such an apparatus is intended for use in
both indoor and outdoor Hazardous (Classified)
Locations where a degree of protection from windblown
dust and rain, splashing and hose-directed water, and
protection from the formation of ice on the enclosure is
required. A series of selected Moore Industries’ 2-Wire
hockey-puck style units mounted in the LH2 enclosure
(consult factory for a list of the certified instruments) are
certified as an Explosion-Proof and Dust Ignition-Proof
appartus in accordance with Factory Mutual Research
‘3600’ standard (NEC-based) and as Flame-Proof in
accordance with the CENELEC/ATEX Directive 94/9/EC
(IEC-based). For applications intended in North America
and other related areas, the approval classifications are
stated on the externally mounted metal ID Tag to be FM
approved as Explosion-Proof for Class I, Division 1,
Groups A, B, C and D; Dust Ignition-Proof for Class II/III,
Division 1, Groups E, F and G; T6 @ 60°C Maximum
Operating Ambient Temperature. In regards to
protection from Environmental hazards/effects, the
apparatus carries a NEMA Type 4X rating with an
Ingress Protection Code of IP66 as per IEC-529. For
applications intended in Europe and other related areas,
the ID Tag clearly states that the apparatus is certified by
ISSeP to be Flame-Proof and marked as such:
II 2GD EEx d IIC; T6 @ Tamb. (-20°C
≤
Tamb.
≤
+60°C). The temperature marking for dust atmo-
spheres is up to + 80°C. The maximum power param-
eters are: Vmax = 42 VDC, Imax = 110 mA and
Pmax = 2W. Also, the tag clearly shows the CE marking
denoting full compliance with the relevant European
Community directives applicable to the Process
Instrumentation Industry. For 2-wire transmitters certified
and intended to be operated as either Intrinsically Safe,
Non-Incendive (Class I, Div. 2) or Type N; the power
parameters are clearly stated on both the Instrument ID
Label and the Apparatus ID Tag. Also, the power
parameters and cabling requirements are stated in the
‘Intrinsically Safe Barrier and Field Installation Diagram’
that is included in the relevant User’s Manuals. This
apparatus is designed in such a way that it: a) does not
give rise to physical injury or other harm due to contact,
b) does not produce excessive surface temperature,
infra-red, electromagnetic, ionizing radiation and, c)
have no non-electrical dangers.
CAUTION
Read, understand and adhere to the manufacturer’s
installation and operating procedures. Substitution of
components may impair the instrument’s Intrinsic Safety
and/or Non-Incendivity. Keep cover tightly closed. Do not
open unit when energized. Do not open unit when either
an explosive gas or dust atmosphere is present. Cable
entry temperature may exceed 70°C. Cabling to be
suitable. Do not allow layers of dust to accumulate on
the surfaces of the equipment. Disconnect power before
servicing.
Contact Information—
If you have installation, mainte-
nance, periodic service, warranty questions or emer-
gency repair requirements, please contact the nearest
Moore Industries sales and service office. Contact
information can be found on the back of this Supplement,
in the User’s Manual for the instrument, or at Moore
Industries’ web site: www.miinet.com
User’s Manual
—Complete information for an individual
instrument model can be found in the Moore Industries
User’s Manual for that instrument. The manual provides
information for putting the instrument safely into service.
This, where applicable, includes instructions, drawings
and diagrams. The Manual also includes appropriate
Warnings, Cautionary Statements, and Notes.
User’s Manual components, where applicable, include:
Introduction
—Brief description of the instrument and its
general application and use.
Specifications
—Provides electrical and environmental
conditions under which the instrument is designed to
safely perform.
Ordering Information
—Provides a description of the
product model number to assist in verifying that the
instrument received matches the instrument ordered for
the installation.
Calibration and Configuration
—Describes how to
accomplish instrument settings and adjustment required
to set up the unit
Installation and Connection
—Describes how to install
the instrument and make electrical connections
(including terminal designations). See the back of this
Supplement for additional information on how to install
the hockey-puck instrument into the LH2 enclosure.
Maintenance
—Describes recommended maintenance (if
any required) for the instrument. The user should consult
their own maintenance procedures for any site-specific
maintenance procedures (such as scheduled re-
calibrations) or other maintenance schedules that may
apply to instruments such as those supplied by Moore
Industries.
Troubleshooting
—Describes, where applicable,
procedures for correcting any operational difficulties that
may be encountered as a result of improper configura-
tion/calibration or installation of the instrument.
Customer Support
—Describes the procedure and
information required to efficiently receive answers to
questions regarding instrument installation, set up, or
operation.
Summary of Contents for TRZ
Page 2: ......