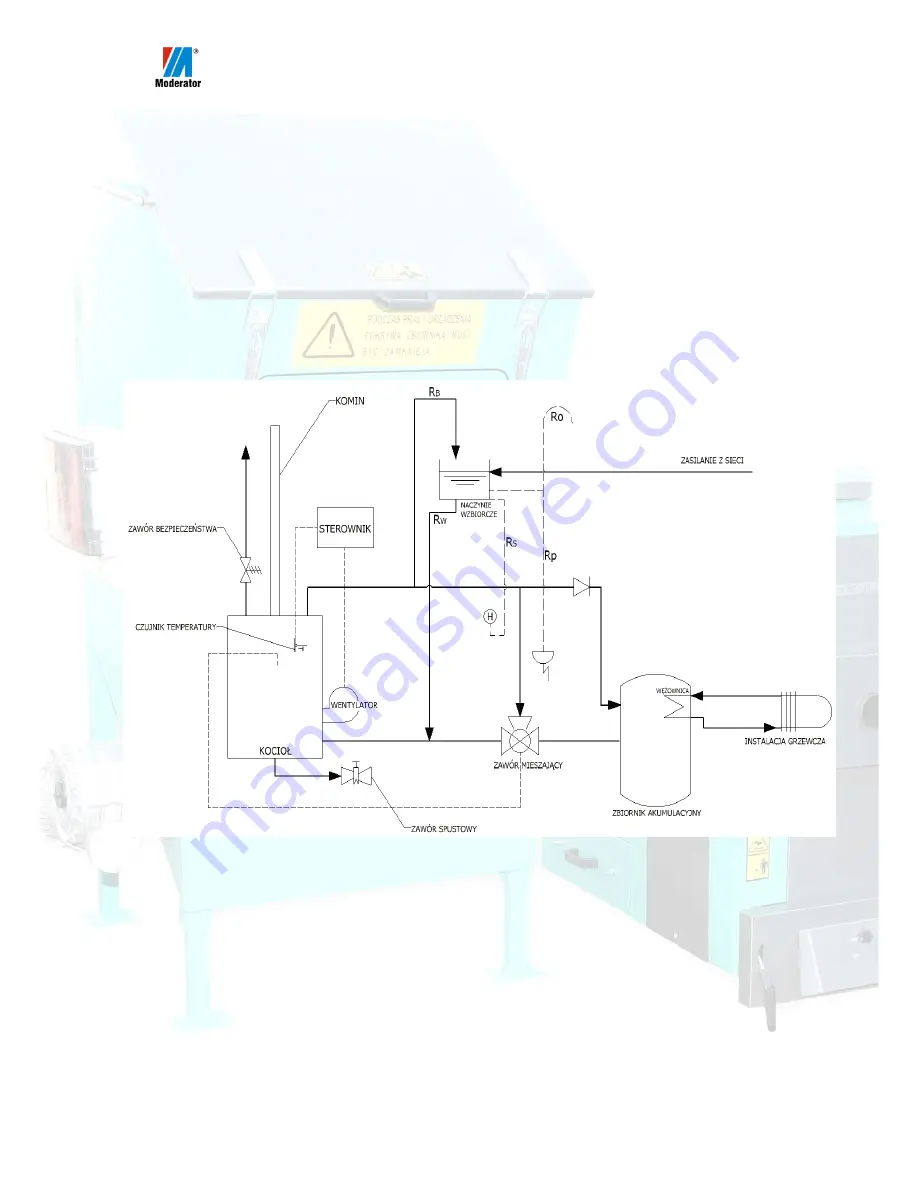
15
overflows in the overflow pipe of the pressure vessel. Installations operating
without losses may be supplied with raw water, provided that its hardness does
not exceed 10n. Otherwise water shall be pre-treated.
Install boiler accessories (handles and Bakelite knobs).
2.5. Protection of the installation
2.5.1. An open system
Moderator boilers operating in open central heating systems must be
connected according to requirements of the PN-91/B-02413 standard, so that
excess heat in the form of steam shall be removed through an open connection
(RP overflow pipe) to atmosphere.
KOMIN – CHIMNEY
ZAWÓR BEZPIECZE
Ń
STWA - SAFETY VALVE
CZUJNIK TEMPERATURY – TEMPERATURE SENSOR
KOCIOŁ – BOILER
STEROWNIK – CONTROLLER
WENTYLATOR – BLOWER
ZAWÓR SPUSTOWY – DRAINAGE VALVE
NACZYNIE WZBIORCZE – PRESSURE VESSEL
ZAWÓR MIESZAJ
Ą
CY– MIXING VALVE
ZBIORNIK AKUMULACYJNY – HEAT ACCUMULATION TANK
W
ĘŻ
OWNICA - COIL
INSTALACJA GRZEWCZA – HEATING INSTALLATION
ZASILANIE Z SIECI - WATER PIPE SUPPLY
Fig. 4 Diagram of installation protection for boilers operated in open central-
heating installations
.