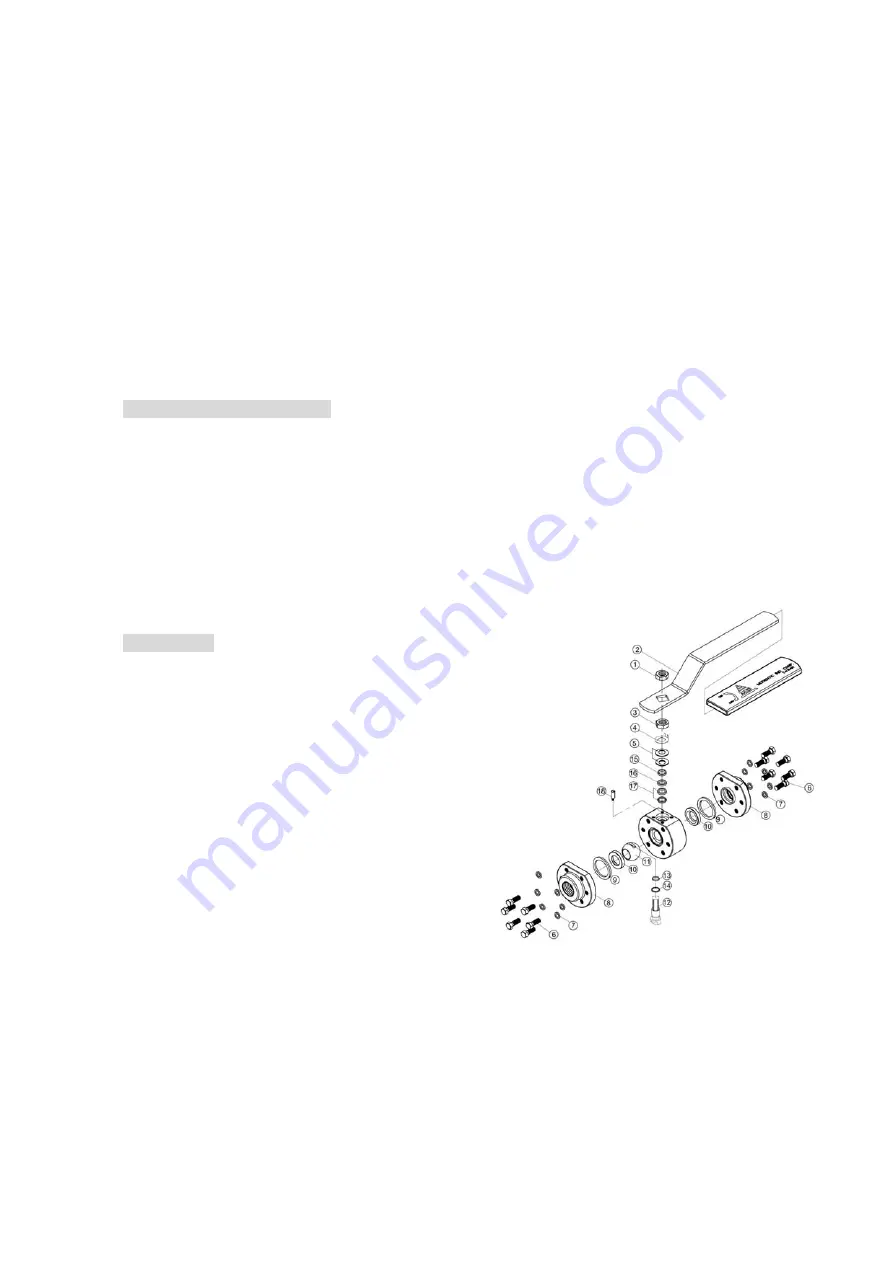
operate the valve about 3 times to ensure
b. S
to
c. A
in about 3 times to ensure the
function.
the function.
ystems hydrostatic test
Before delivery, valves are tested 1.5 times
the allowable working pressure at ambient
temperature in open position. After
installation, the pipe line system may
subject to system tests, as condition not
exceed the maximum working pressure.
fter pressure testing, user shall operate the
valve aga
7.
a.
ion, such as pressure, temperature and
b.
the product to avoid danger in the
future.
Dangers of inappropriate use
Never uses the product exceed its allowed
condit
fluid.
If the product has any inappropriate use, the
product was damage however there are no
signals occurs immediately. User shall
change
8.
a.
re effect and high-temperature
effect etc.
b.
ement between stem and
stem packing.
c.
em
ry,
(1)
valve must follow the
(2)
and inflammability
(3)
dure is protecting the surface of the
(4)
the seat retainer fall down from end
(5)
d the ball
d
ion, maintenance, and
(1
damage factors as far as possible as
(2
Maintenance
Maintenance frequency
The maintenance frequency is determined
upon the application. User shall consider the
time interval depend on the kinds of fluid,
flow velocity, operation frequency,
high-pressu
Adjustment of the Gland
Tighten the gland nut about
¼
turn
periodically to compensate for the wear
caused by mov
Disass
bly
(NOTE
If complete disassembly is necessa
replacement of all seats and seals is recommended.)
To dismantle the
procedure below.
It doesn’t matter where the position of
valve located is; usually it contained the
seal up fluid, so operator must be very
carefully when moving the valve on the
pipe. It must open the ball a little and let
the fluid come out slowly, it also need to
watch out the poisonous
objects if there is any.
It must turn the ball in the close position
before dismantle the valve. The ball cannot
be taken out from valve body if the ball is in
the open or semi-open position. The right
position for store the valve is put the flange
end on the ground. If it is a valve with the
hand wheel, than it must dismantle the
hand
wheel from the valve
first than put
the valve flange end on the ground. This
proce
ball.
To dismantle the valve body and end cap,
release retainer with a special tool. It
must be careful to dismantle the ball to
avoid
cap.
To lift the ball by hoist, it must make the
protection on corner to avoi
damaged by metal contacted.
. Parts inspect
replacement:
) Check the surface of ball if it is scraped
use the PT for inspection if necessary. If
there is any damage on the surface, then find
out the root cause such as the dirt fluid…etc.
avoid the
we can .
) The damage of the ball surface, to gauge if it
is locate on the contacting area of ball and ball
5
Summary of Contents for 3PC
Page 5: ...f Dimensions Parts List 3 ...
Page 10: ...8 ...