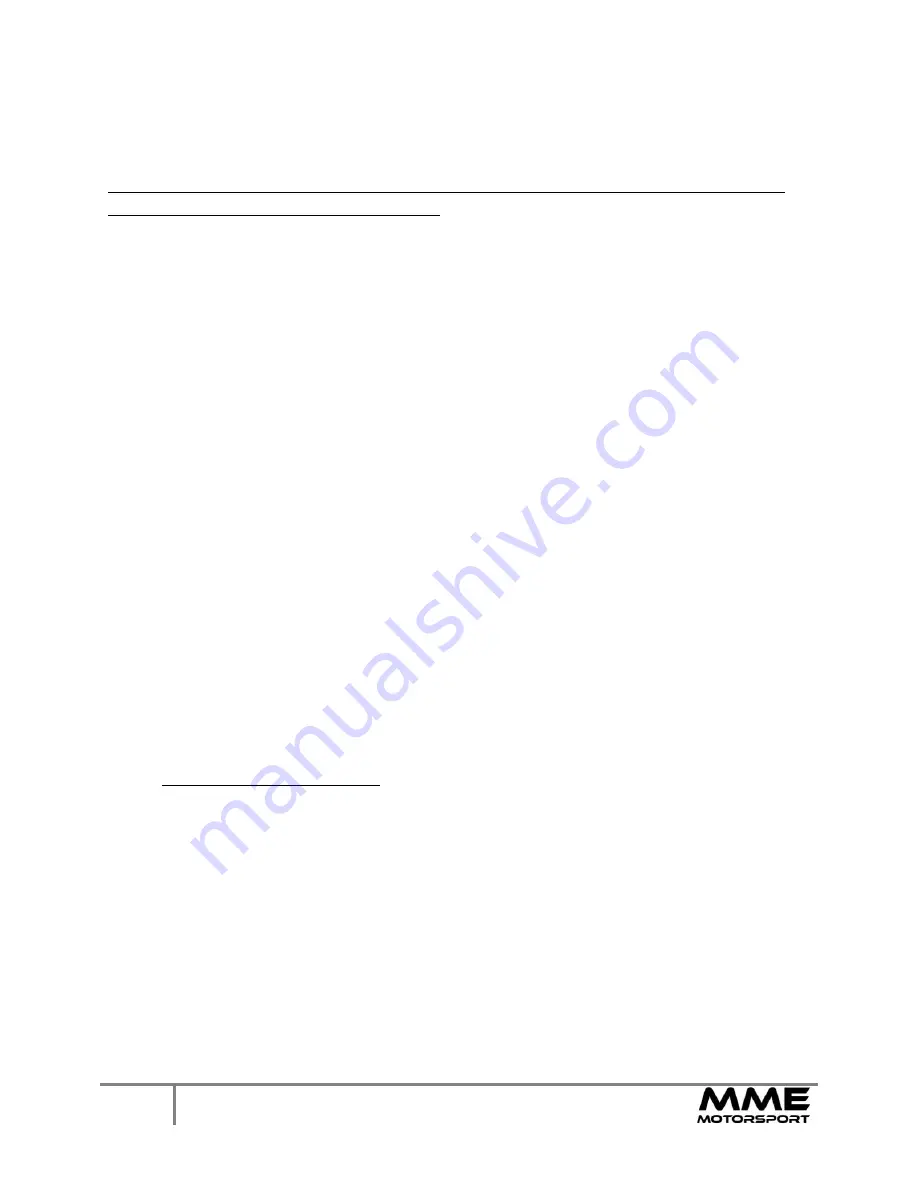
2020-08-26
GCU7 Manual
29
XIII.
H PATTERN GEARBOX – QUICKSTART
Please note: if any parameter is changed, settings must be sent to the GCU (Settings – send to GCU or
Send Changed to GCU - F5) in order to take effect.
After successfully connected to the GCU7 (green bottom bar in the software), go to the
GENERAL/SENSORS
tab and:
Select
GEARBOX Type
to H-Pattern. If you have our clutch actuator and this is synchromesh
gearbox, choose H / Synchromesh, otherwise H / Dogbox.
Under
GEARBOX Function
, Select Standalone if you want the GCU to take care of the cutting,
blip signal and every other operation needed to shift. If you have Engine ECU capable of
complete paddle shifting logic, use Ext. Logic. Please note: if you only do the cutting with Engine
ECU, you still need the Standalone, because GCU7 will still need to send a signal to cut.
Adjust
NEUTRAL SENSOR
and
CLUTCH SENSOR
accordingly. If you will shift with the paddles
from N->R, R->N, N->1 or 1->N you need to enable this switch. If you’re using clutch actuator,
clutch sensor has to be enabled and Type set to MME CA/CCU.
Verify that all connected inputs are working correctly. In the top right corner you can see if
GCU7 sees the signals. Inputs to look for and: UP paddle, DOWN paddle, Neutral*, Clutch*.
Verify the
Ignition
CUT, Blip (
if present) outputs by pressing the output tests.
Enter number of gears and gear ratios in the
GEARBOX
group and go to
DOWN
tab and adjust
the
Max engine RPM
parameter. This is the absolute maximum engine rpm you will able to
reach when downshifting. Go back to the
GENERAL/SENSORS
tab.
If you use pressure sensor (usually not the case), enable the
AIR PRESSURE SENSOR
and enter
max sensor pressure. Currently, we only support 4-20 mA sensors (connected to GCU7 pin A1).
Adjust
TACHO SENSOR
and
TPS
, including the TPS Calibration process if needed (
Calibrate
button). Make sure the RPM and TPS are working properly. For more info see
GENERAL/SENSORS in chapter II.
Go to
UP
tab and:
Adjust
Allow shift from N to 1
and
R to N
accordingly.
Put these to 0:
Delay after cut
,
Keep cut after shift
,
Don’t cut if TPS <
,
Actuator preload
,
Lever
return actuator
. Increase
Delay after cut
if engine is slow to respond to the cut.
Disable:
Auto retry on failed shift
,
Autoshift
and
External cut
.
Set
Min between shifts to
200ms.
If you have MME TBC module installed (drive by wire), uncheck the
Close throttle instead of
CUT.