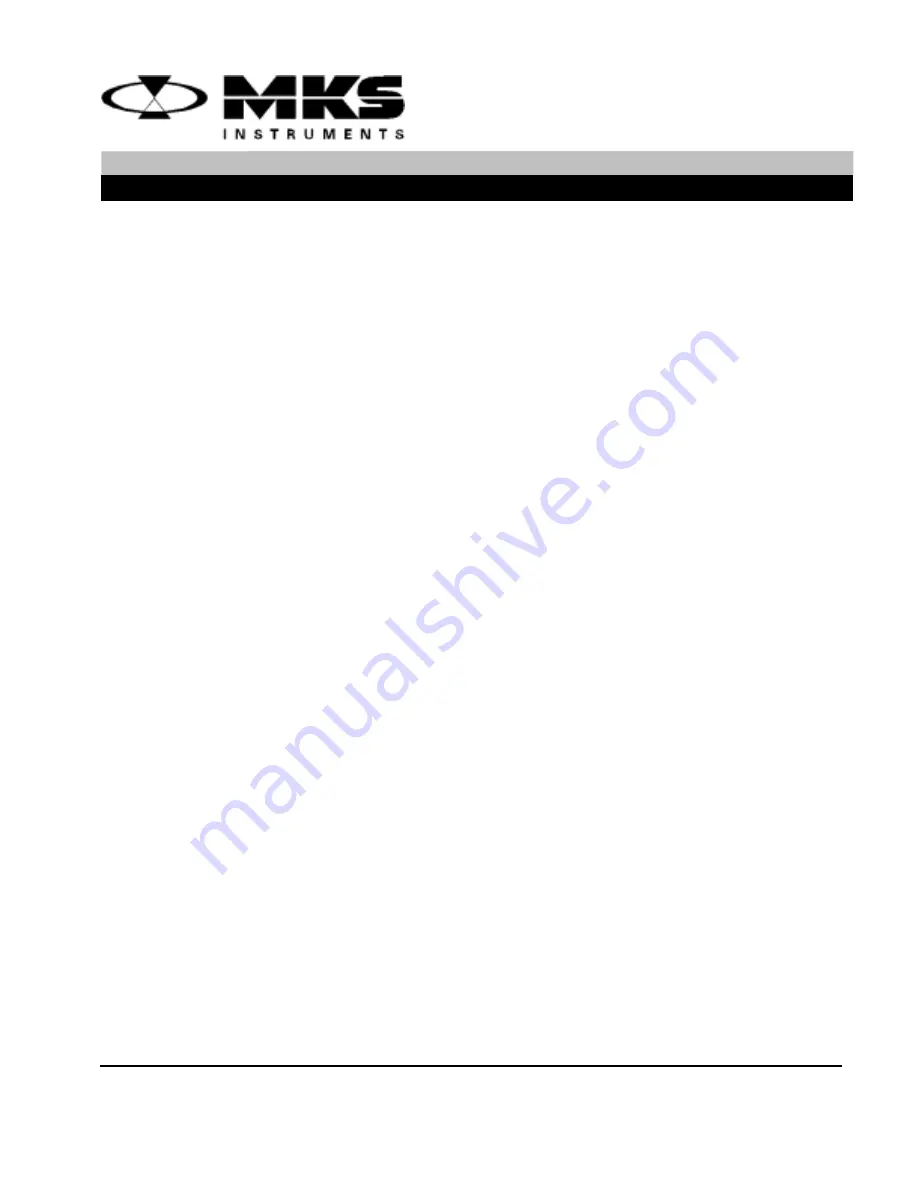
117082-P1
Rev D, 1/98
Instruction Manual
MKS Type 653B
Exhaust Throttle Valve
Six Shattuck Road
Andover, MA 01810-2449
(800) 227-8766 or (978) 975-2350
Fax: (978) 975-0093
E-mail: [email protected]
Web site: http://www.mksinst.com
117082-P1
Rev D, 1/98
Instruction Manual
MKS Type 653B
Exhaust Throttle Valve
Six Shattuck Road
Andover, MA 01810-2449
(800) 227-8766 or (978) 975-2350
Fax: (978) 975-0093
E-mail: [email protected]
Web site: http://www.mksinst.com