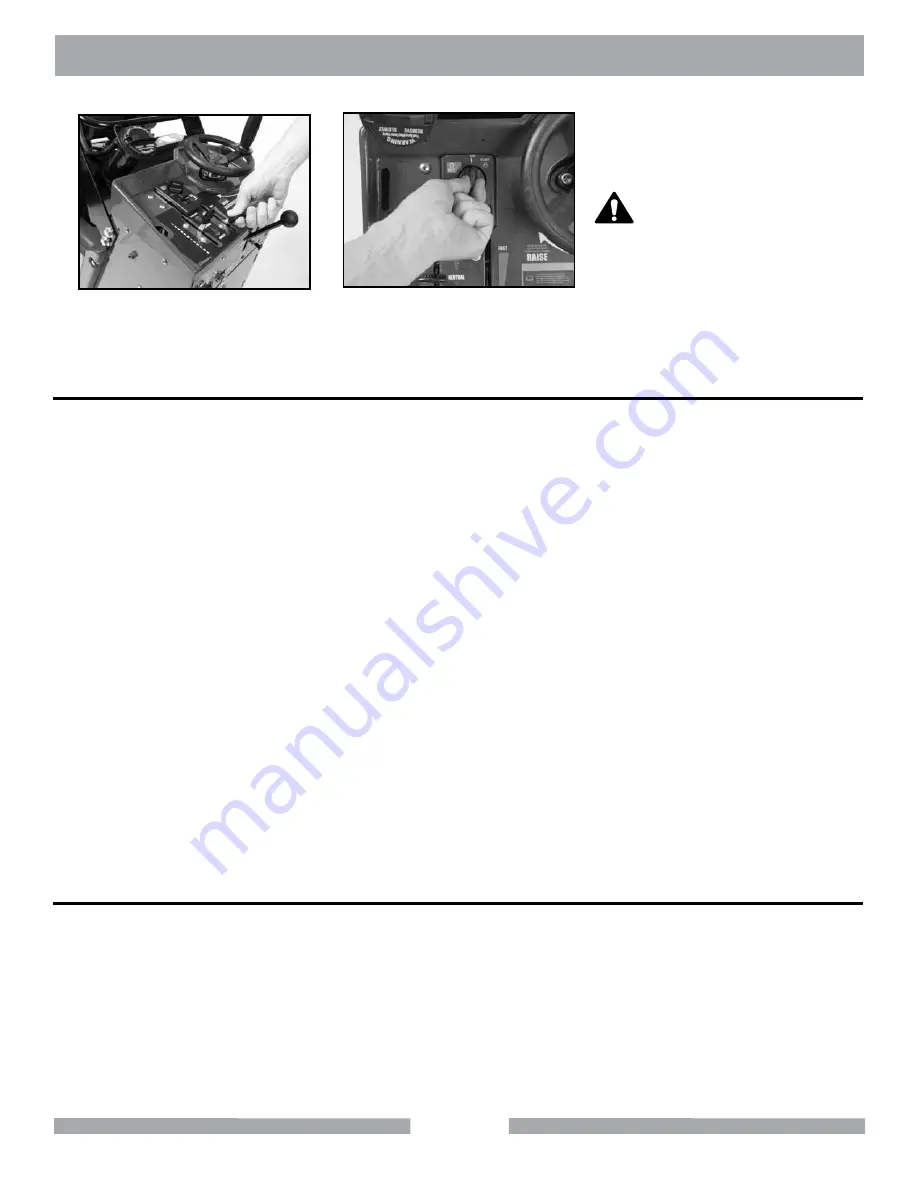
23
(M)
Move the Throttle Lever to lower
blade speed.
(N)
Turn off engine by rotating
Ignition Switch to off position.
dRY CUTTING
STEP CUTTING
MK-20 SERIES
oPERATIoN
1. Ensure the blade you are using is clearly marked for dry cutting.
2. Check the condition of the air filter at least every four hours of operation.
Refer to Engine Manual for details.
Airflow helps to cool the blade during dry cutting. Cutting too deep with one pass, or exerting exces-
sive forward or side pressure can be dangerous and cause damage. Step cut in increments of 2
inches or less, for best results. Thinner blades are especially advantageous when cutting dry.
NoTE:
If the engine has been running
hard and is hot do not shut en-
gine off abruptly. Cool engine by
removing load and allowing en-
gine to run idle for 3 to 5 minutes.
Do not turn off engine while
at full throttle.
NoTICE
NoTE:
1. Follow general instructions outlined in the section Standard Operation on page 19.
2. When deep sawing (more than 4”) or concrete with hard aggregate, sawing to full depth in
several cuts should be made in incremental steps of 1-1/2 to 2 inches until the desired depth of
cut is reached. In softer aggregates or asphalt, it may be possible to saw full depth in two passes.
3. Gradually move the speed control lever forward to increase the cutting speed. If the blade stalls in
the cut (which can happen when deep sawing) immediately raise blade from cut. If not done
at once, the belts will spin freely and burn. Check belts for proper tension and continue sawing at
a slower rate of speed.
4. On final pass, lower the blade until it hits the sub-base (sandy color will appear in the water being
discharged from the cut). Raise blade approximately 1/2” from bottom. The sand and gravel
particles of the sub-base may cause premature wear or damage to the saw blade.
5. It is common, on the final pass of the cut, for pavement to wedge blade, particularly on a hot day.
When this happens, immediately stop engine. If the blade is wedged, remove the Blade Shaft Bolt
and Outside Collar and move the saw away from the blade. To remove a wedged blade from the
concrete, use a jack hammer and carefully chip out concrete around the blade. (Pounding or
twisting the blade may cause severe damage).
6. Go slowly with a new blade until it “opens up” that is, until you can see and feel the diamonds.
7. Small corrections can be made by leaning on handles.
Deep sawing is very hard on saws and blades. Experienced operators soon get a “feel” for the
saw and are constantly on guard to slow down when they hit excessive steel or hard aggregate.
Summary of Contents for MK-2013HE GX390
Page 9: ...9 NOTES...
Page 33: ...33 NOTES...
Page 36: ...36 MK 20 Series EXPLODED VIEW FIGURE 1 PARTS LIST MK 2020HSP concrete saw P N 156498...
Page 42: ...42 MK 20 Series Exploded View FIGURE 2 PARTS LIST MK 2024HSP concrete saw P N 158777...
Page 55: ...55 NOTES...
Page 58: ...58 notes...
Page 59: ...59 notes...