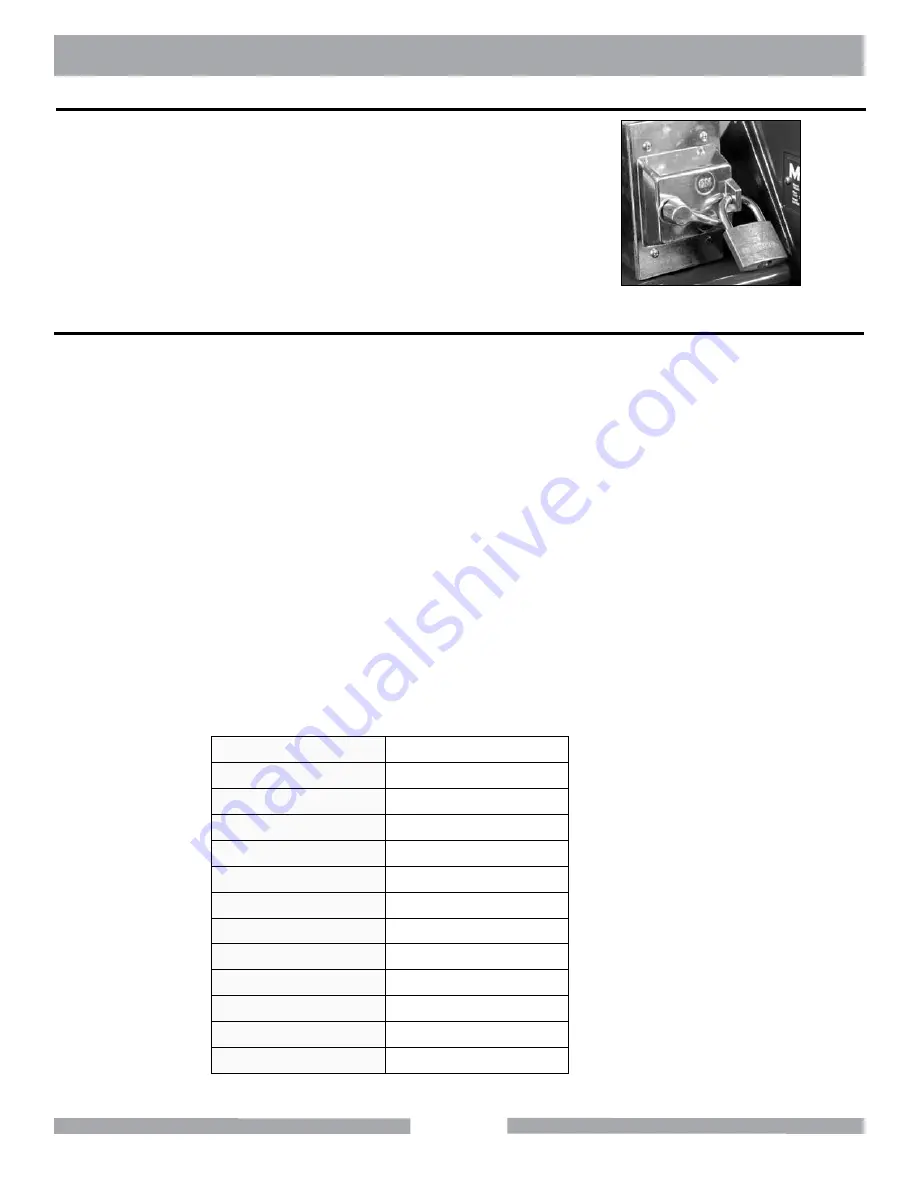
20
PRODUCT SPECIFICATIONS
Motor
Baldor (Electric)
Power
1-1/2 HP, 120V
AMP
14.3
Blade RPM
3450
Blade Capacity
10” (254 mm)
Arbor
5/8"
Depth of Cut
3” (76 mm)
Length of Cut
24" (610 mm)
Diagonally Cut
18" (457 mm)
L x W x H (inches) 48" x 24" x 29"
L x W x H (mm)
1,219 x 610 x 737
Weight
156 lbs. (71 kg)
Part #
153243-JCS
Motor available in other electrical configurations.
• Integrated stand allows operator to set up or transport in a matter of seconds
• Solid rubber heavy-duty wheels won't scuff floors
• Designed for easy transport, loading and storage by one person
• Integrated gas shocks help handle the weight of the saw during setup and breakdown
• Wheel latches prevents stand from moving during operation
• Fully enclosed high torque, fan-cooled motor
• Permanently lubricated, dual-sealed, heavy-duty blade shaft bearings
• Multi-position motor post and cutting head for convenient cutting of various tile sizes
• Built-in water distribution system supplies water to both sides of blade
• Variable height cutting head allows for plunge cuts and use of blades smaller than 10" in diameter
• Accommodates 6" and 8" profile wheels
• Micro V-belt drive
• Blade shaft lock for easy blade removal
• Linear-bearing and chrome plated guide-bar assembly ensure precise cutting
• Cast aluminum blade guard and motor post
• Made in the USA
• One-year limited warranty
MK-101 Pro24 JCS SAFETY
In order to help prevent accidental starting and to help make
your work area “kidproof,” this machine is provided with a
means to deactivate the functioning of the motor switch. The
switch is equipped with a lockout tab that can be used with a
lock to prevent movement of the switch. With the switch un-
able to move the motor cannot be turned on. Removing the
lock reactivates the switch.
LOCK OUT METHOD
Summary of Contents for MK-101 PRO24
Page 51: ...51 NOTES ...
Page 54: ...54 MK 101 Pro24 JCS EXPLODED VIEW JCS Portable Stand Part 169218 ...
Page 66: ...66 NOTES ...
Page 67: ...67 NOTES ...