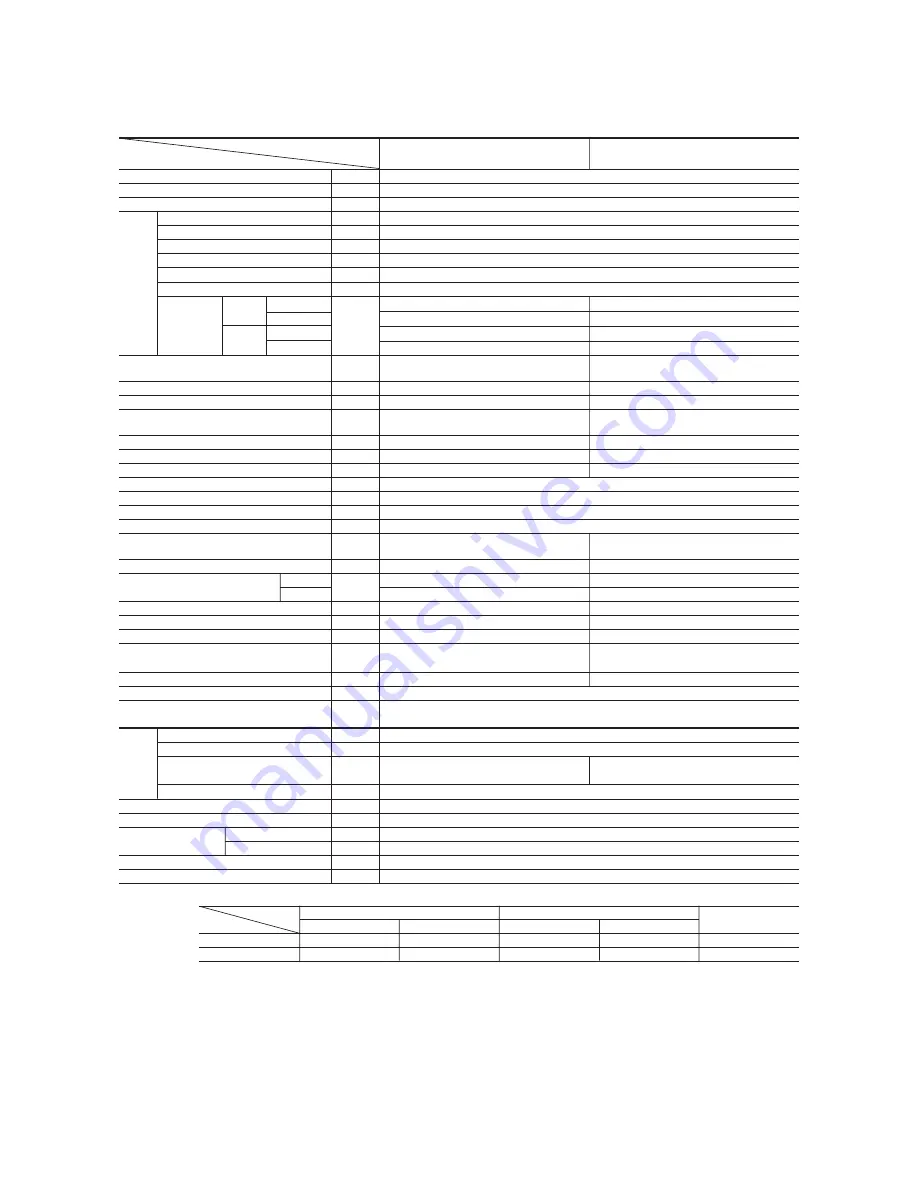
-
3
-
Model SRK63HE (Indoor unit)
SRC63HE (Outdoor unit)
(2) The operation data are applied to the 220/230/240V districts respectively.
(3) The refrigerant quantity to be charged includes the refrigerant in 7m connecting piping.
(Purging is not required even in the short piping.)
If the piping length is longer, when it is 7 to 15m, add 25g refrigerant per meter.
Item
Model
SRK63HE
SRC63HE
Cooling capacity
(1)
W
6100
Heating capacity
(1)
W
6300
Power source
1 Phase, 220-240V, 50Hz
Cooling input
kW
2.17
Running current (Cooling)
A
10.8/10.4/9.9
Heating input
kW
1.83
Running current (Heating)
A
9.1/8.7/8.4
Inrush current
A
48.2
COP
Cooling: 2.81 Heating: 3.44
Cooling
Sound level
Hi 44, Me 40, Lo 37
49
Noise level
Power level
dB
59
65
Heating
Sound level
Hi 45, Me 40, Lo 38
49
Power level
60
65
Exterior dimensions
Height
×
Width
×
Depth
mm
318
×
1098
×
248
640
×
850
×
290
Color
Yellowish white
Stucco white
Net weight
kg
15
48
Refrigerant equipment
Compressor type & Q’ty
–
RM5526GNE4 (Rotary type)
×
1
Motor
kW
–
1.9
Starting method
–
Line starting
Heat exchanger
Slit fins & inner grooved tubing
Straight fin & inner grooved tubing
Refrigerant control
Capillary tubes + Electric expansion valve
Refrigerant
(3)
kg
R22 1.6 (Pre-Charged up to the piping length of 7m)
Refrigerant oil
R
0.7 (B-32SAM)
Deice control
Microcomputer control
Air handling equipment
Fan type & Q’ty
Tangential fan
×
1
Propeller fan
×
1
Motor
W
46
43
(Cooling)
18
42
Air flow (at High)
(Heating)
CMM
19
42
Air filter, Q’ty
Polypropylene net (washable)
×
2
–
Shock & vibration absorber
–
Cushion rubber (for compressor)
Electric heater
–
–
Operation control
Operation switch
Wireless-Remote control
–
Room temperature control
Microcomputer thermostat
–
Pilot lamp
RUN (Green), TIMER (Yellow), HI POWER (Green), ECONO (Orange)
Safety equipment
O.D
mm (in)
Liquid line:
φ
6.35 (1/4
″
)
Gas line:
φ
15.88 (5/8
″
)
Connecting method
Flare connecting
Attached length of piping
Liquid line: 0.70m
Gas line: 0.63m
–
Insulation
Necessary (Both sides)
Drain hose
Connectable
Power source supply
Terminal block (Screw fixing type)
Size
×
Core number
1.5 mm
2
×
4 cores (Including earth cable)
Connection wiring
Connecting method
Terminal block (Screw fixing type)
Accessories (included)
Mounting kit, Clean filter (Natural enzyme filter
×
1, Photocatalytic washable deodorizing filter
×
1)
Optional parts
Wired - Remote control
Notes (1) The data are measured at the following conditions.
Item
Indoor air temperature
Outdoor air temperature
Standards
Operation
DB
WB
DB
WB
Cooling
27ºC
19ºC
35ºC
24ºC
ISO-T1, JIS C9612
Heating
20ºC
–
7ºC
6ºC
ISO-T1, JIS C9612
Operation data
(1) (2)
Refrigerant
piping
Compressor: overheat protection, Heating overload protection (High pressure control), Frost protection,
Serial signal error protection, Indoor fan motor error protection
The piping length is 7.5m.
(220/230/240V)