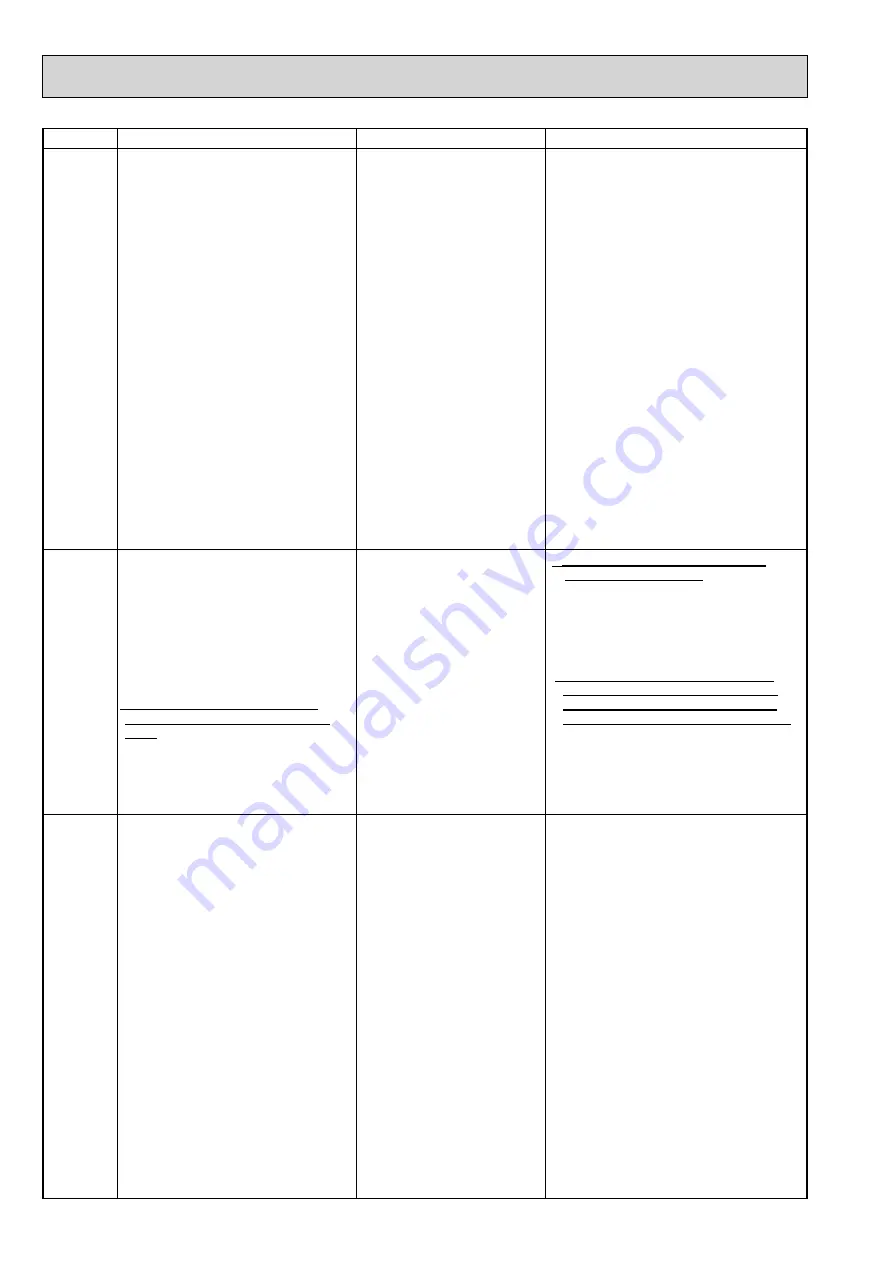
16
Error Code
Abnormal point and detection method
Cause
Countermeasure
P9
Pipe temperature thermistor / Condenser
/ Evaporator (TH5)
1
The unit is in 3-minute resume protec-
tion mode if short/open of thermistor is
detected. Abnormal if the unit does not
get back to normal within 3 minutes. (The
unit returns to normal operation, if it has
been reset normally.)
2
Constantly detected during cooling,
drying, and heating operation (except
defrosting)
Short: 90°C or more
Open: -40°C or less
1
Defective thermistor
characteristics
2
Contact failure of connector
(CN29) on the indoor controller
board (Insert failure)
3
Breaking of wire or contact
failure of thermistor wiring
4
Temperature of thermistor is
90°C or more or -40°C or less
caused by defective refrigerant
circuit.
5
Defective indoor controller
board
1
–
3
Check resistance value of thermistor.
For characteristics, refer to (P1) above.
2
Check contact failure of connector (CN29)
on the indoor controller board.
Refer to 8-5.
Turn the power on and check restart after
inserting connector again.
4
Operate in test run mode and check pipe
<condenser/evaporator> temperature with
outdoor controller circuit board. If pipe
<condenser/evaporator> temperature is
extremely low (in cooling mode) or high (in
heating mode), refrigerant circuit may have
defect.
5
Operate in test run mode and check pipe
<condenser/evaporator> temperature
with outdoor control circuit board. If there
is extreme difference with actual pipe
<condenser/evaporator> temperature replace
indoor controller board.
There is no abnormality if none of above
comes within the unit.
Turn the power off and on again to operate.
E0
or
E4
Remote controller transmission
error(E0)/signal receiving error(E4)
1
Abnormal if main or sub remote con-
troller cannot receive any transmission
normally from indoor unit of refrigerant
address “0” for 3 minutes.
(Error code : E0)
2
Abnormal if sub-remote controller could
not receive for any signal for 2 minutes.
(Error code: E0)
1
Abnormal if indoor controller board
cannot receive normally any data from
remote controller board or from other
indoor controller board for 3 minutes.
(Error code: E4)
2
Indoor controller board cannot receive
any signal from remote controller for 2
minutes. (Error code: E4)
1
Check disconnection or looseness of indoor
unit or transmission wire of remote controller.
2
Set one of the remote controllers “main”, if
there is no problem with the action above.
3
Check wiring of remote controller.
• Total wiring length: max. 500 m
(Do not use cable × 3 or more)
• The number of connecting indoor units:
max. 16 units
• The number of connecting remote
controller: max. 2 units
When the above-mentioned problem of
1
~
3
are not seen.
4
Diagnose remote controllers.
a) When “RC OK” is displayed, remote
controllers have no problem.
Turn the power off, and on again to check.
If abnormality generates again, replace
indoor controller board.
b) When “RC NG” is displayed, replace
remote controller.
c) When “RC E3” or “ERC 00-66” is displayed,
noise may be causing abnormality.
1
Contact failure at transmission
wire of remote controller
2
All remote controllers are set
as “sub” remote controller. In
this case, E0 is displayed on
remote controller, and E4 is
displayed at LED (LED1, LED2)
on the outdoor controller circuit
board.
3
Miswiring of remote controller
4
Defective transmitting/receiving
circuit of remote controller
5
Defective transmitting/receiving
circuit of indoor controller board
of refrigerant address “0”
6
Noise has entered into the
transmission wire of remote
controller.
In case of checking pipe temperature
with outdoor controller circuit board,
be sure to connect A-control service
tool (PAC-SK52ST).
(
)
PL
Abnormal refrigerant circuit
During Cooling, Dry, or Auto Cooling
operation, when the following are
regarded as failures when detected for
one second.
a) The compressor continues to run for 30
or more seconds.
b) The liquid pipe temperature or the
condense/evaporator temperature is
75°C or more.
* These detected errors will not be
cancelled until the power source is
reset.
1
Abnormal operation of 4-way
valve
2
Disconnection of or leakage in
refrigerant pipes
3
Air into refrigerant piping
4
Abnormal operation (no rotation)
of indoor fan
·
Defective fan motor.
·
Defective indoor control
board.
5
Defective refrigerant circuit
(clogging)
1
When this error occurs, be sure to
replace the 4-way valve.
2
Check refrigerant pipes for disconnection or
leakage.
3
After the recovery of refrigerant, vacuum
dry the whole refrigerant circuit.
4
Refer to section 8-7.
5
Check refrigerant circuit for operation.
* To avoid entry of moisture or air into
refrigerant circuit which could cause
abnormal high pressure, purge air in
refrigerant circuit or replace refrigerant.
OCH493D