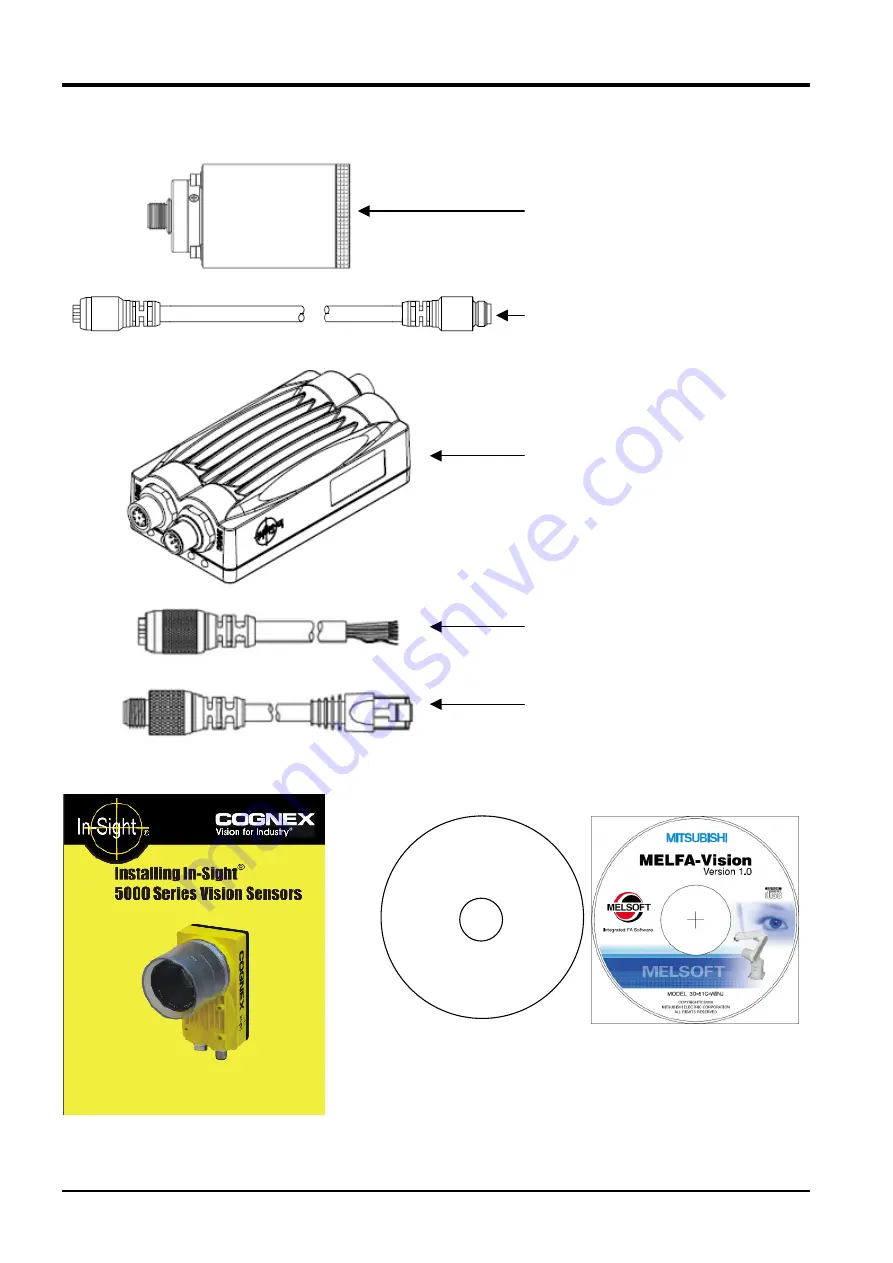
2
System configuration
Component Devices
2-10
The composition of 4D-2CG-5400R-PKG(Remote Head) are shown in figures.
Installation guide
Figure 2-2 Basic set(Remote Head Type) composition
Remote Head Camera
Camera Cable
Network Vision sensor
Breakout Cable
Network Cable
In‑Sight Software CD‑ROM
MELFA-Vision CD-ROM