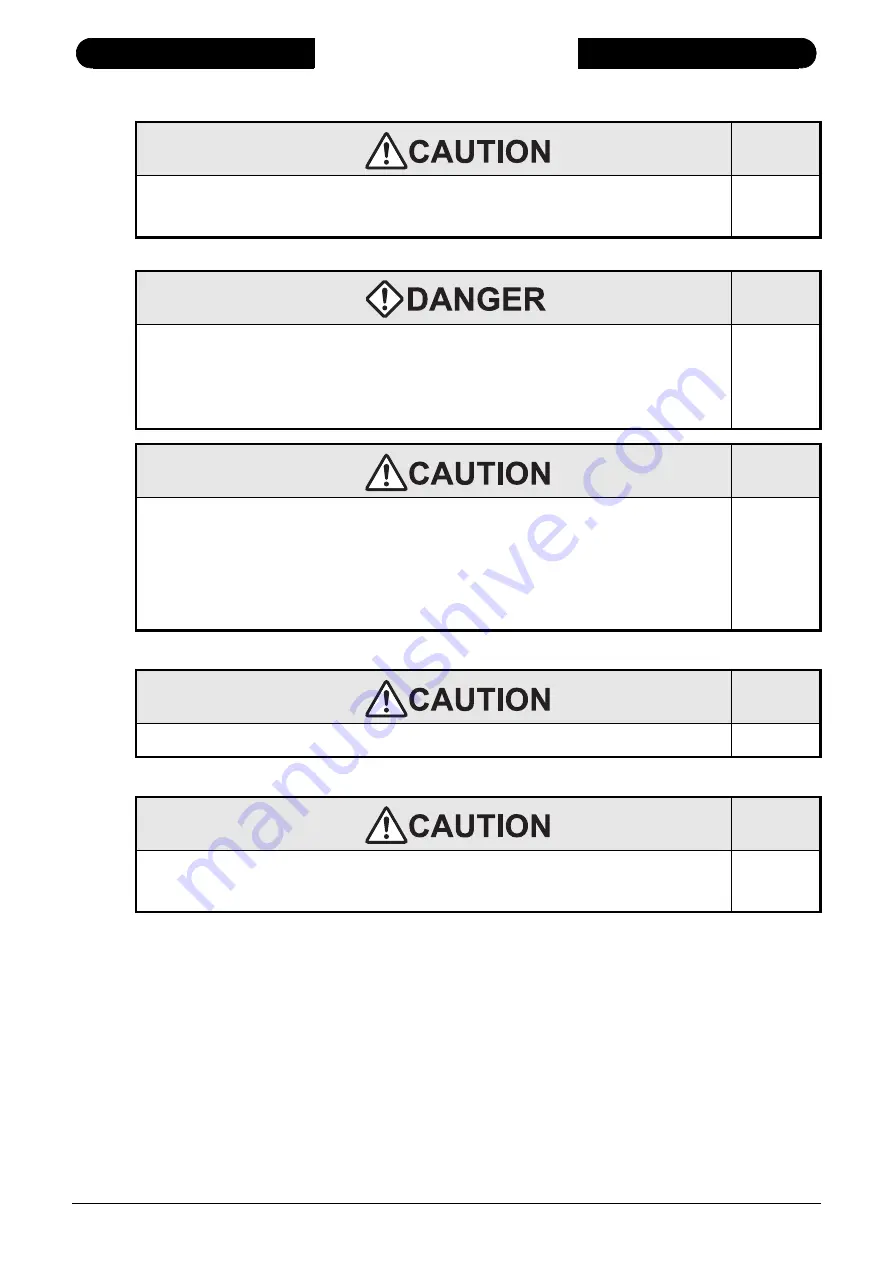
Safety Precautions
(Read these precautions before using.)
(3)
4. STARTUP AND MAINTENANCE PRECAUTIONS
5. DISPOSAL PRECAUTIONS
6. TRANSPORTATION PRECAUTIONS
Reference
•
When disconnecting a communication/power cable connected to the module, do not hold the cable area.
For a cable connected to a terminal block, loosen screws of the terminal block, then disconnect the cable.
If a cable is pulled while it is connected to a module, the module may malfunction or the module and the cable may
be damaged.
24
Reference
•
Do not touch any terminal while the PLC's power is on.
Doing so may cause electric shock or malfunctions.
•
Before cleaning or retightening terminals, cut off all phases of the power supply externally.
Failure to do so may cause electric shock.
•
Before modifying or disrupting the program in operation or running the PLC, carefully read through this manual and
the associated manuals and ensure the safety of the operation.
An operation error may damage the machinery or cause accidents.
24
Reference
•
Do not disassemble or modify the PLC.
Doing so may cause fire, equipment failures, or malfunctions.
For repair, contact your local Mitsubishi Electric distributor.
•
Turn off the power to the PLC before connecting or disconnecting any extension cable.
Failure to do so may cause equipment failures or malfunctions.
•
Turn off the power to the PLC before attaching or detaching the following devices.
Failure to do so may cause equipment failures or malfunctions.
-
Display module, peripheral devices, expansion boards, and special adapters
-
Terminal blocks, I/O extension units/blocks and special function units/blocks
25
Reference
•
Please contact a certified electronic waste disposal company for the environmentally safe recycling and disposal of
your device.
14
Reference
•
The PLC is a precision instrument. During transportation, avoid impacts larger than those specified in the general
specifications of the PLC main unit manual.
Failure to do so may cause failures in the PLC.
After transportation, verify the operations of the PLC.
14
Summary of Contents for FX3U-64CCL
Page 1: ...FX3U 64CCL USER S MANUAL ...
Page 2: ......
Page 6: ... 4 MEMO ...
Page 11: ...5 FX3U 64CCL User s Manual Table of Contents Warranty 69 Revised History 70 ...
Page 77: ......