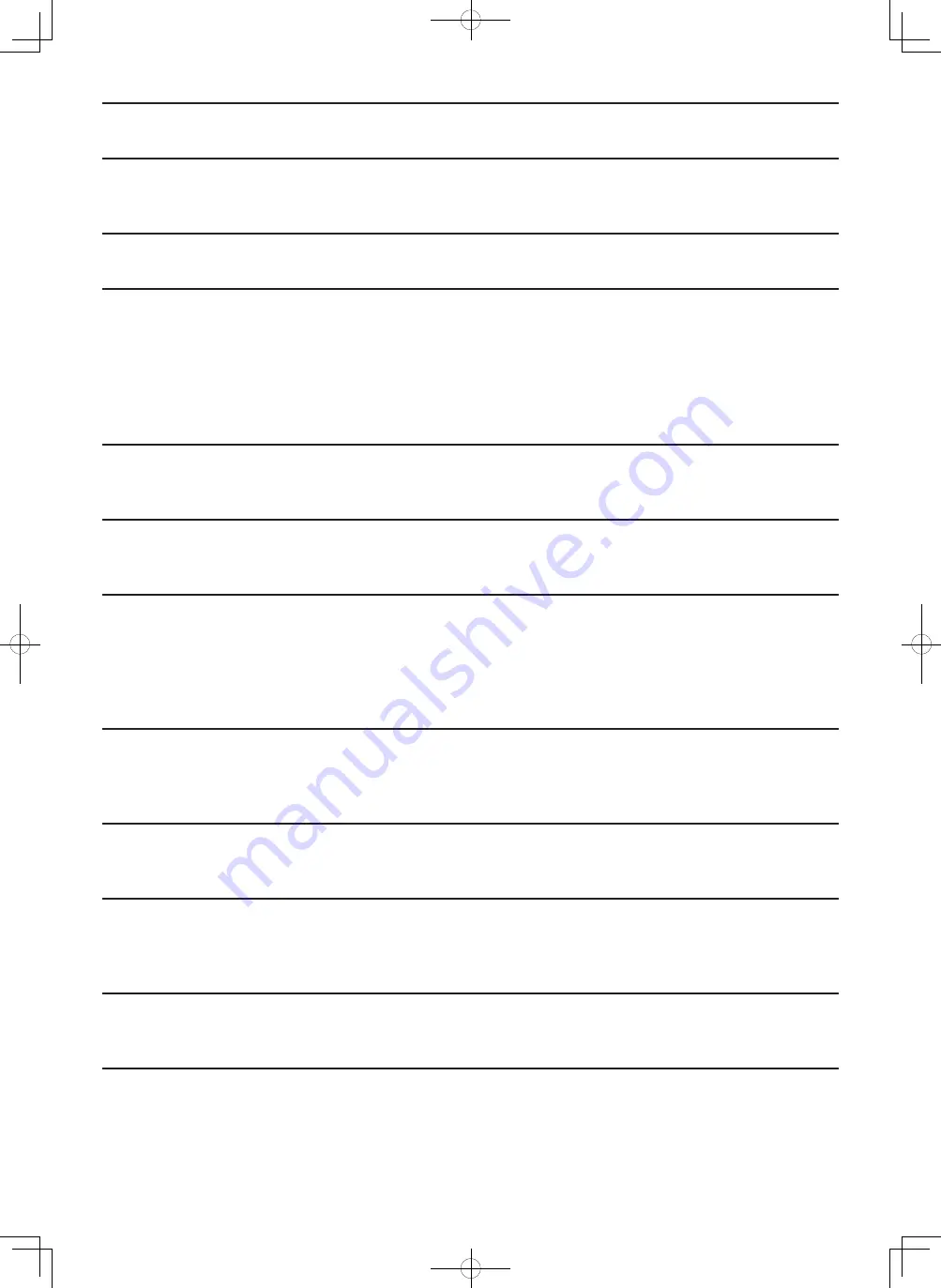
Keep the service valves closed until refrigerant charging is completed.
-Failure to do so will damage the unit.
Place a wet towel on the service valves before brazing the pipes to keep the temperature of
the valves from rising above 120ºC (248ºF).
-Failure to do so may result in equipment damage.
Keep the flame out of contact with the cables and metal sheet when brazing the pipes.
-Failure to do so may result in burnout or malfunction.
Use the following tools specifically designed for use with the specified refrigerant: Gauge
manifold, charge hose, gas leak detector, check valve, refrigerant charge base, vacuum
gauge, and refrigerant recovery equipment.
-Gas leak detectors for conventional refrigerants will not react to a refrigerant that does not
contain chlorine.
-If the specified refrigerant is mixed with water, refrigerant oil, or another refrigerant, the
refrigerant oil will deteriorate and the compressor will malfunction.
Use a vacuum pump with a check valve.
-If the vacuum pump oil flows back into the refrigerant lines, the refrigerant oil may deteriorate
and the compressor may malfunction.
Keep tools clean.
-If dust, dirt, or water accumulates on the charging hose or the flare processing tool, the
refrigerant will deteriorate and the compressor will malfunction.
Use refrigerant piping made of phosphorus deoxidized copper (copper and copper alloy
seamless pipes) that meets local requirements. Pipe joints should also meet local
requirements. Keep the inner and outer surfaces of the pipes clean and free of sulphur,
oxides, dust/dirt, shaving particles, oils, moisture, or any other contaminants.
-Contaminants on the inside of the refrigerant piping will cause the refrigerant oil to deteriorate
and cause the compressor to malfunction.
Store pipes indoors, and keep both ends of the pipes sealed until just before making a
flare connection or brazing. (Store elbows and other joints in plastic bags.)
-If dust, dirt, or water enters the refrigerant lines, the refrigerant oil will deteriorate and the
compressor will malfunction.
Braze the pipes with a nitrogen purge to avoid oxidation.
-Oxidized flux inside the refrigerant pipes will cause the refrigerant oil to deteriorate and cause
the compressor to malfunction.
Do not use existing refrigerant piping.
-The old refrigerant and refrigerant oil in the existing piping contain a large amount of chlorine,
which will cause the refrigerant oil in the new unit to deteriorate and cause the compressor to
malfunction.
Charge refrigerant in a liquid state.
-Charging refrigerant in the gaseous state will change the composition of the refrigerant and lead
to a performance drop.
Do not use a charging cylinder when charging refrigerant.
-The use of a charging cylinder may change the composition of the refrigerant and lead to a
performance drop.
8
WT09050X01