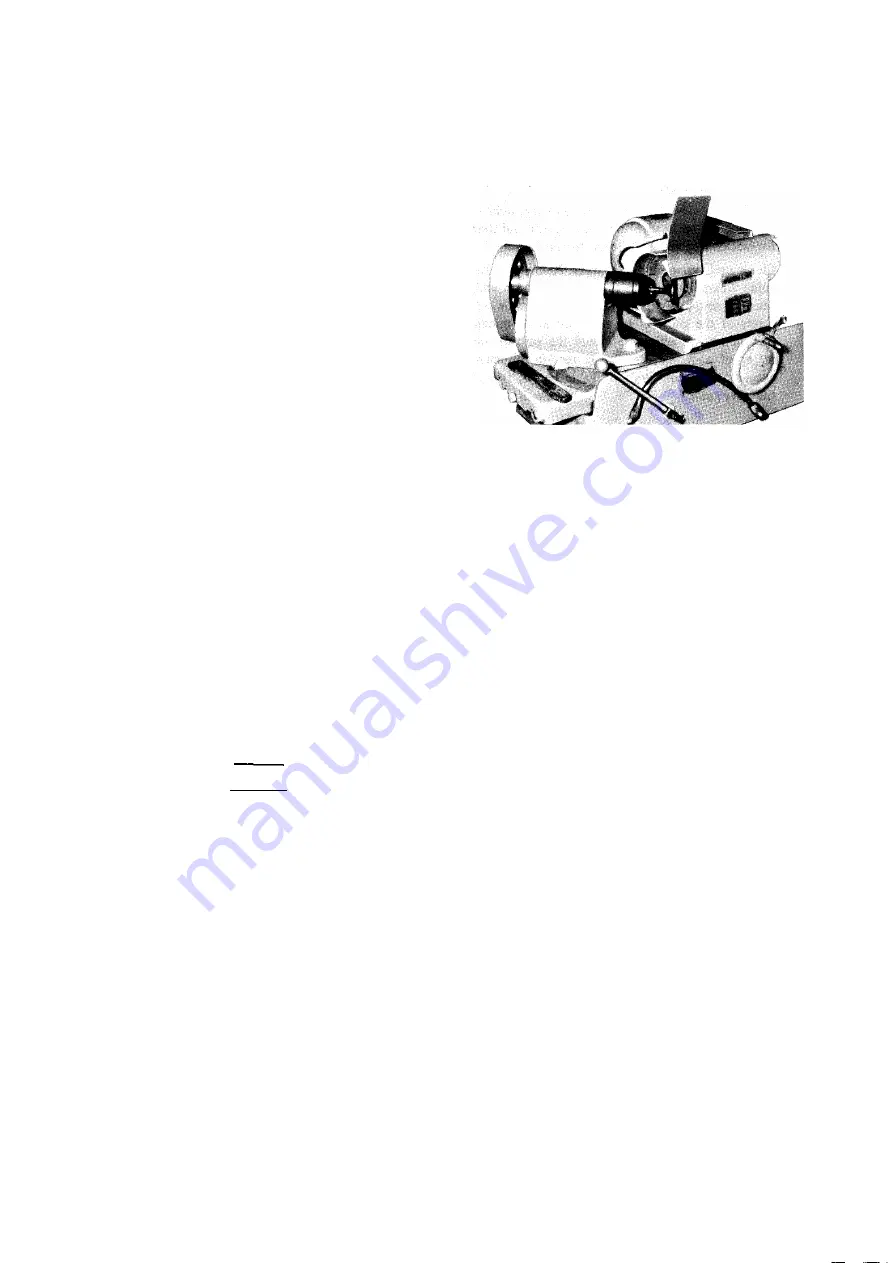
Valve refacer
{a) Set a valve refacer to an angle of 45 degrees.
{b) Grind the valve stock to a minimum and, if the
margin is less than 1.2 mm (0.04 7 in.), replace
the valve.
Valve seat cutter
Repair an excessively worn valve seat by using a
valve seat grinder or valve seat cutter.
(c) When using a valve seat cutter, exercise care so
as to apply a uniform pressure to valve seat to
prevent uneven cutting. After cutting, reface
the seat by rotating the cutter with No. 400
sandpaper put between the cutter and seat.
(d)
If
valve seat width is overcut, repair it using a
30-degree cutter.
If
valve seat width exceeds
1.6 mm (0.063 in.) due to wear, rep.lace the
seat. Also replace the seat when valve sinkage
exceeds 1.3 mm (0.051 in.).
Valve seat installation
Chill the valve seat inserts in ether or alcohol containing
dry ice. Heat the cylinder head to a temperature of 80
°
C
to 100
°
C (176
°
F to 212
°
F). Press the inserts in the
cylinder head by using the insert calking tools (30691-
02700 for intake valve, 30691-02800 for exhaust valve).
Leave the cylinder head and the inserts in the air until
shrinkage-expansion fit is obtained between the two.
Calk around the inserts with the insert calking tool to
machine the seat width.
(NOTE]
The insert calking tool may be used both for
pressing and calking the valve seat inserts by
reversing the calking ring.