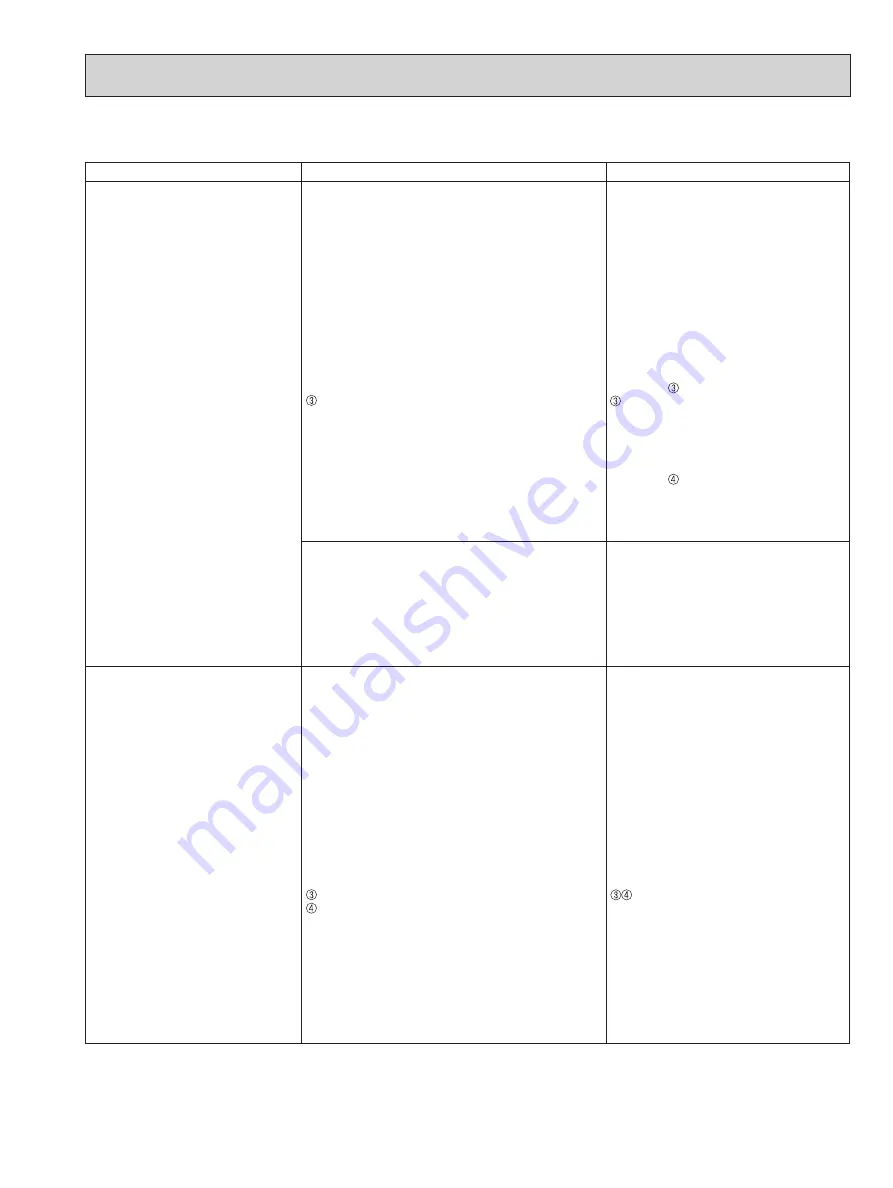
23
OCHT669
8-4. TROUBLESHOOTING OF PROBLEMS
Note: Refer to the manual of outdoor unit for the detail of remote controller.
*1: only P-series outdoor unit
Phenomena
Cause
Countermeasure
(1) LED2 on indoor controller board
is off.
• When LED1 on indoor controller board is also off.
1
Power supply of rated voltage is not supplied to out-
door unit.
2
Defective outdoor controller circuit board
Power supply of 220–240 V AC is not supplied to
indoor unit.
4
Defective indoor controller board
1
Check the voltage of outdoor power
supply terminal block (L, N) or (L
3
, N).
• When 220–240 V AC is not detected,
check the power wiring to outdoor unit
and the breaker.
• When 220–240 V AC is detected,
check
2
(below).
2
Check the voltage between outdoor
terminal block S1 and S2.
• When 220–240 V AC is not detected,
—check the fuse on outdoor controller
circuit board.
—check the wiring connection.
• When 220–240 V AC is detected,
check (below).
Check the voltage between indoor terminal
block S1 and S2.
• When 220–240 V AC is not detected,
check indoor/outdoor unit connecting
wire for miswiring.
• When 220–240 V AC is detected,
check (below).
4
Check the wiring connection between
TB4 and CN01. Check the fuse on indoor
controller board. If no problems are found,
indoor controller board is defective.
• When LED1 on indoor controller board is lit.
1
Mis-setting of refrigerant address for outdoor unit
(There is no unit corresponding to refrigerant address
“0”.) *
1
1
Check the setting of refrigerant address
for outdoor unit.
Set the refrigerant address to “0”.
(For grouping control system under
which 2 or more outdoor units are
connected, set one of the units to “0”.)
Set refrigerant address using SW1 (3-6)
on outdoor controller circuit board.*
1
(2) LED2 on indoor controller board
is blinking.
• When LED1 on indoor controller board is also blinking.
Connection failure of indoor/outdoor unit connecting
wire
• When LED1 is lit
1
Miswiring of remote controller wires
Under twin indoor unit system, 2 or more indoor units
2
Refrigerant address for outdoor unit is wrong or not
set.
Under grouping control system, there are some units
whose refrigerant address is 0. *
1
Short-cut of remote controller wires
Defective remote controller
Check indoor/outdoor unit connecting wire
for connection failure.
1
Check the connection of remote
controller wires in case of twin triple
indoor unit system. When 2 or more
indoor units are wired in one refrigerant
system, connect remote controller wires
to one of those units.
2
Check the setting of refrigerant address
in case of grouping control system. If
there are some units whose refrigerant
addresses are 0 in one group, set one of
the units to 0 using SW1 (3-6) on outdoor
controller circuit board. *
1
Remove remote controller wires and
check LED2 on indoor controller board.
• When LED2 is blinking, check the
condition of the remote controller wires,
to see if they are shorted.
• When LED2 is lit, connect remote
controller wires again and:
if LED2 is blinking, remote controller
is defective; if LED2 is lit, connection
failure of remote controller terminal
block, etc. has returned to normal.