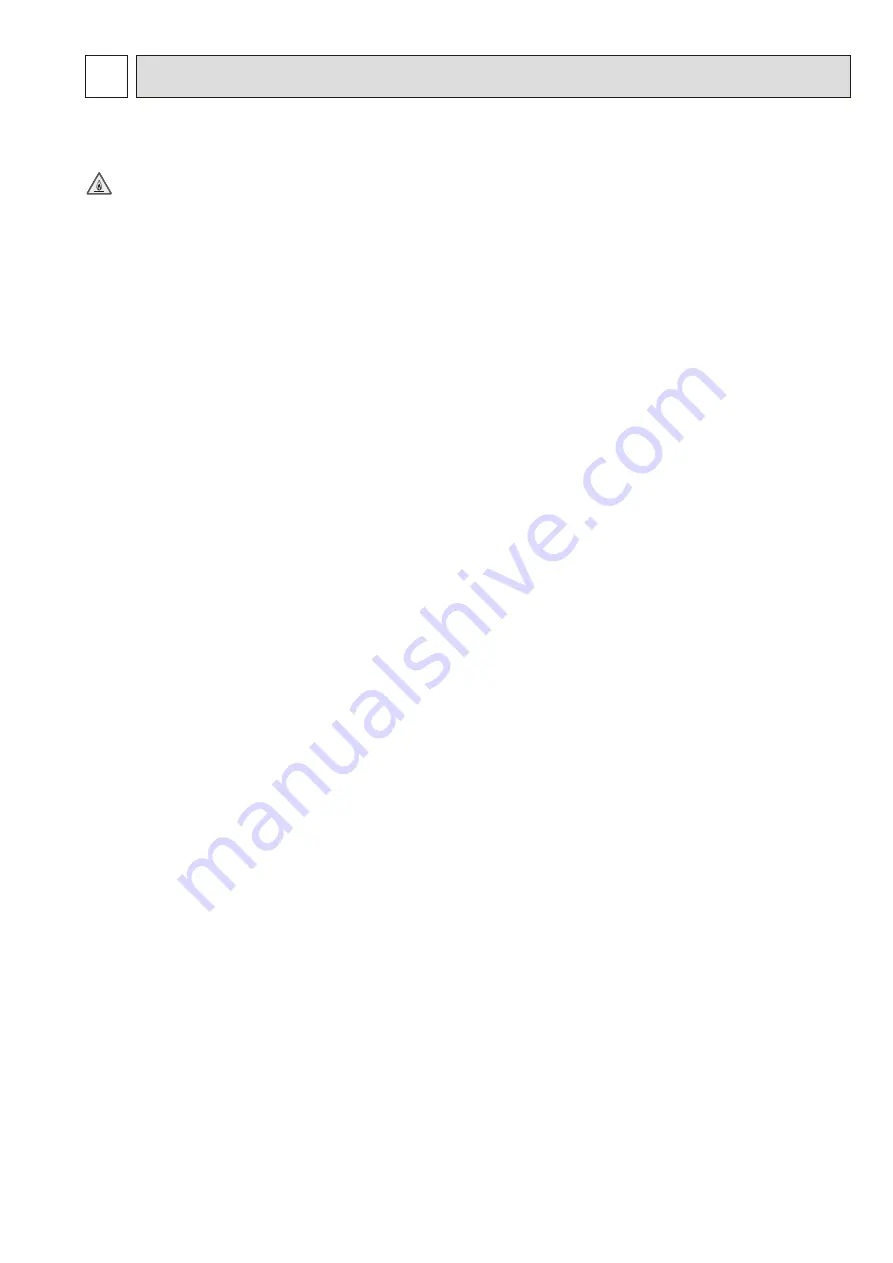
3
2
SAFETY PRECAUTION
Cautions for units utilizing refrigerant R32/R410A
2-1. CAUTIONS RELATED TO NEW REFRIGERANT
WARNING
1. Warning for service
(1) In case of reconnecting the refrigerant pipes after detaching, make the flared part of pipe re-fabricated.
(2) This unit should be installed in rooms which exceed the floor space specified in outdoor unit installation manual. Refer to
outdoor unit installation manual.
(3) Refrigerant pipes connection shall be accessible for maintenance purposes.
(4) Do not use low temperature solder alloy in case of brazing the refrigerant pipes.
(5) Do not use means to accelerate the defrosting process or to clean, other than those recommended by the manufacturer.
(6) The appliance shall be stored in a room without continuously operating ignition sources (for example: open flames, an
operating gas appliance or an operating electric heater).
(7) Do not pierce or burn.
(8) Be aware that refrigerants may not contain an odour.
(9) Pipe-work shall be protected from physical damage.
(10) The installation of pipe-work shall be kept to a minimum.
(11) Compliance with national gas regulations shall be observed.
(12) Keep any required ventilation openings clear of obstruction.
(13) Servicing shall be performed only as recommended by the manufacturer.
(14) The appliance shall be stored in a well-ventilated area where the room size corresponds to the room area as specified for
operation.
(15) Maintenance, service and repair operations shall be performed by authorized technician with required qualification.
2. Cautions for unit using R32 refrigerant
Basic work procedures are the same as those for conventional units using refrigerant R410A. However, pay careful
attention to the following points.
(1) Information on servicing
(1-1) Checks on the Area
Prior to beginning work on systems containing flammable refrigerants, safety checks are necessary to ensure that the
risk of ignition is minimized.
For repair to the refrigerating systems, (1-3) to (1-7) shall be completed prior to conducting work on the systems.
(1-2) Work Procedure
Work shall be undertaken under a controlled procedure so as to minimize the risk of a flammable gas or vapor being
present while the work is being performed.
(1-3) General Work Area
All maintenance staff and others working in the local area shall be instructed on the nature of work being carried out.
Work in confined spaces shall be avoided. The area around the workspace shall be sectioned off. Ensure that the con-
ditions within the area have been made safe by control of flammable material.
(1-4) Checking for Presence of Refrigerant
The area shall be checked with an appropriate refrigerant detector prior to and during work, to ensure the technician is
aware of potentially toxic or flammable atmospheres. Ensure that the leak detection equipment being used is suitable
for use with all applicable refrigerants, i.e. non-sparking, adequately sealed or intrinsically safe.
(1-5) Presence of Fire Extinguisher
If any hot work is to be conducted on the refrigeration equipment or any associated parts, appropriate fire extinguishing
equipment shall be available to hand.
Have a dry powder or CO2 fire extinguisher adjacent to the charging area.
(1-6) No Ignition Sources
No person carrying out work in relation to a refrigeration system which involves exposing any pipe work shall use any
sources of ignition in such a manner that it may lead to the risk of fire or explosion. All possible ignition sources, includ-
ing cigarette smoking, should be kept sufficiently far away from the site of installation, repairing, removing and disposal,
during which refrigerant can possibly be released to the surrounding space. Prior to work taking place, the area around
the equipment is to be surveyed to make sure that there are no flammable hazards or ignition risks. “No Smoking” signs
shall be displayed.
(1-7) Ventilated Area
Ensure that the area is in the open or that it is adequately ventilated before breaking into the system or conducting any
hot work. A degree of ventilation shall continue during the period that the work is carried out. The ventilation should
safely disperse any released refrigerant and preferably expel it externally into the atmosphere.
OBH843