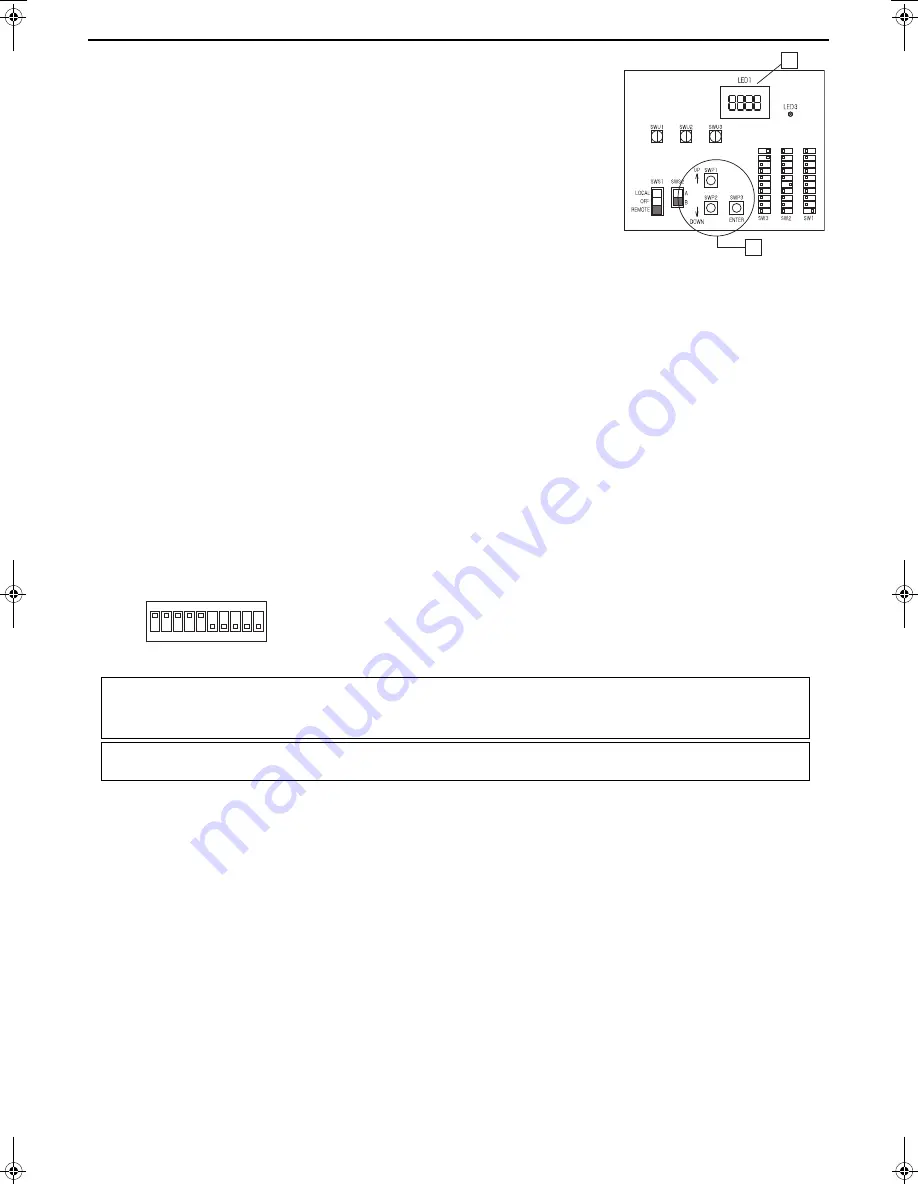
28
3. Set the preset values with the switches on the circuit board.
(1) Set the dip switches SW2 and SW3 by following the procedure in
page 49. (Set the dip switches 3-8, 3-9, and 3-10 to ON.)
* [EEEE] will disappear, and an item code ([101]) will appear on LED1
(labeled B in the figure at right).
(2) Use SWP3 to toggle through the item codes and select an item code to
change its current value. (The item codes will appear in the following
order: [101]
→
[104]
→
[105]
→
[106]
→
[107]....)
(3) Use SWP1 to increase the value and SWP2 to decrease the value.
(4) Press SWP3 to save the changed value.
(5) Set the dip switches 3-8, 3-9, and 3-10 to OFF.
(6)
When connecting AE-200, perform the procedures described in 4 on
page 31.
Following the steps above, set the value for the following items as necessary.
[101] Not used
[104] Not used
[105] Function setting (When AE-200 is not connected to QAHV, the values set by rotary switches SWU1 and SWU2
are set as the preset values. When AE-200 is connected to QAHV, set the preset values referring to the notes
below.)
[106] Total number of units in the system (Initial value: 1) (Leave it as it is.)
[107] “2” when connected to AE-200 (Initial value: 0)
[108] Not used
[109] Not used
[110] Function setting (“1” when connected to AE-200) (Initial value: 0)
[111] M-NET address of main sensor of own tank (Initial value: 1)
[112 to 120] Not used
[121] Secondary side control is enabled when “1” is set. (Initial value: 0)
* When connecting AE-200 and remote controller (PAR-W31MAA) simultaneously, make the settings above, and
then turn off the power, turn it back on, and set “1” for item code [105]. After these settings, perform the
procedures described in (5) on page 32.
* Set SWS1 to OFF from the remote controller or with the local switch.
Settings cannot be changed unless the ON/OFF switch is set to OFF.
B
A
ON
1
23
456
7
89
1
0
ON
1
23
456
7
89
1
0
ON
1
23
456
7
89
1
0
10’s digit (0) 1’s digit (1)
(0)
ON
1
2
3
4
5
6
7
8
9
10
The figure at left shows that the switches 1 through 5 are set to ON and 6 through 10 are set to OFF.
WT08219X05.book 28 ページ 2018年10月1日 月曜日 午後7時47分
Summary of Contents for QAHV
Page 83: ......