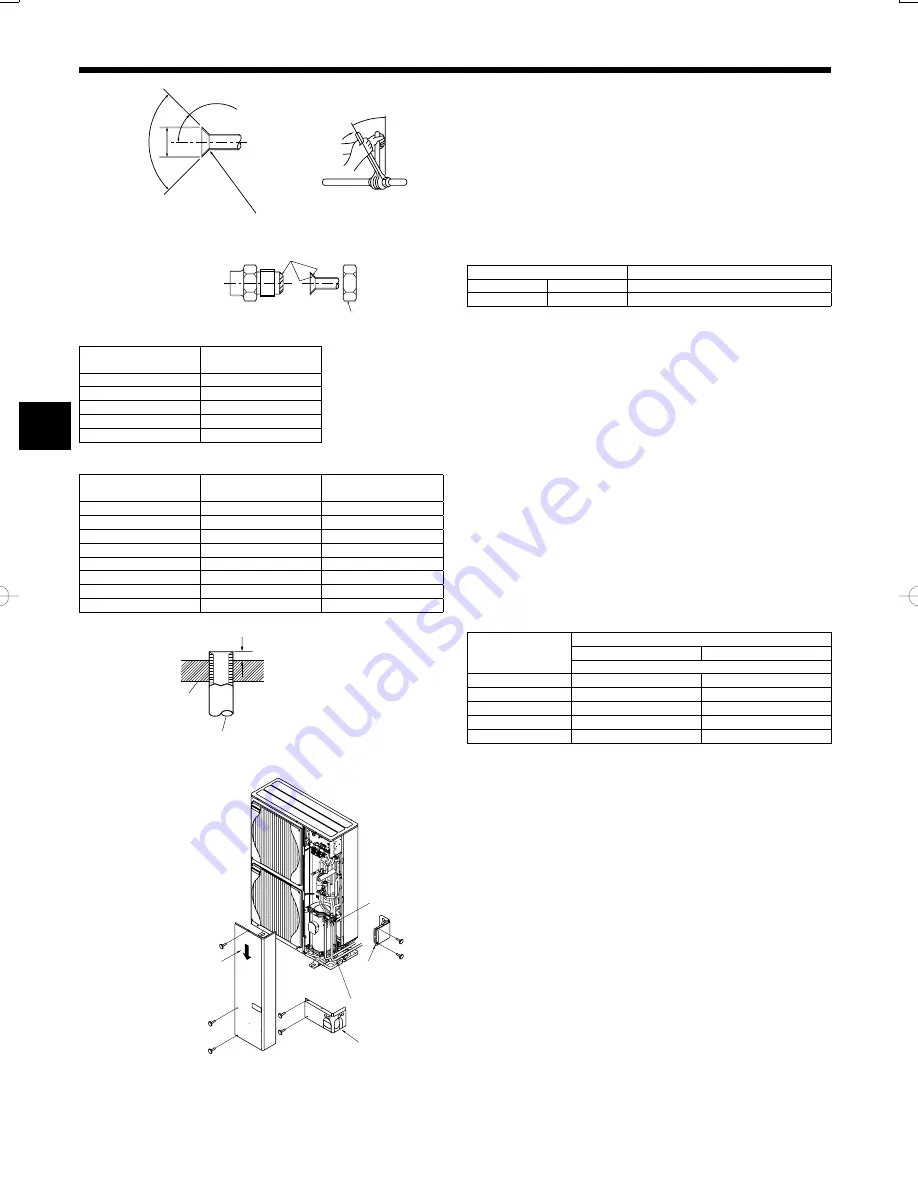
90
op
0.5
o
øA
R0.4~R0.8
45
op
2
o
6
4.2. Connecting pipes (Fig. 4-1)
•
When commercially available copper pipes are used, wrap liquid and gas pipes
with commercially available insulation materials (heat-resistant to 100 °C or
more, thickness of 12 mm or more).
•
The indoor parts of the drain pipe should be wrapped with polyethylene foam
insulation materials (specifi c gravity of 0.03, thickness of 9 mm or more).
•
Apply thin layer of refrigerant oil to pipe and joint seating surface before tighten-
ing fl are nut.
A
•
Use two wrenches to tighten piping connections.
B
•
Use leak detector or soapy water to check for gas leaks after connections are
completed.
•
Apply refrigerating machine oil over the entire fl are seat surface.
C
•
Use the fl are nuts for the following pipe size.
D
HRP71,100,125
Gas side
Pipe size (mm)
ø15.88
Liquid side
Pipe size (mm)
ø9.52
•
When bending the pipes, be careful not to break them. Bend radii of 100 mm to
150 mm are suffi cient.
•
Make sure the pipes do not contact the compressor. Abnormal noise or vibration
may result.
1
Pipes must be connected starting from the indoor unit.
Flare nuts must be tightened with a torque wrench.
2
Flare the liquid pipes and gas pipes and apply a thin layer of refrigeration oil (Ap-
plied on site).
•
When usual pipe sealing is used, refer to Table 1 for fl aring of R410A refrigerant
pipes.
The size adjustment gauge can be used to confi rm A measurements.
A
(Fig. 4-1)
Copper pipe O.D.
(mm)
Flare dimensions
øA dimensions (mm)
ø6.35
8.7 - 9.1
ø9.52
12.8 - 13.2
ø12.7
16.2 - 16.6
ø15.88
19.3 - 19.7
ø19.05
23.6 - 24.0
B
(Fig. 4-1)
Copper pipe O.D.
(mm)
Flare nut O.D.
(mm)
Tightening torque
(N·m)
ø6.35
17
14 - 18
ø6.35
22
34 - 42
ø9.52
22
34 - 42
ø12.7
26
49 - 61
ø12.7
29
68 - 82
ø15.88
29
68 - 82
ø15.88
36
100 - 120
ø19.05
36
100 - 120
A
Flare cutting dimensions
B
Flare nut tightening torque
A
B
C
D
A
Die
B
Copper pipe
A
B
Fig. 4-1
Fig. 4-2
A
Table 1 (Fig. 4-2)
Copper pipe O.D.
(mm)
A (mm)
Flare tool for R410A
Flare tool for R22·R407C
Clutch type
ø6.35 (1/4")
0 - 0.5
1.0 - 1.5
ø9.52 (3/8")
0 - 0.5
1.0 - 1.5
ø12.7 (1/2")
0 - 0.5
1.0 - 1.5
ø15.88 (5/8")
0 - 0.5
1.0 - 1.5
ø19.05 (3/4")
0 - 0.5
1.0 - 1.5
4. Installing the refrigerant piping
Fig. 4-3
A
Front piping cover
B
Piping cover
C
Stop valve
D
Service panel
E
Bend radius : 100mm -150mm
4.3. Refrigerant piping (Fig. 4-3)
Remove the service panel
D
(three screws) and the front piping cover
A
(two
screws) and rear piping cover
B
(two screws).
1
Perform refrigerant piping connections for the indoor/outdoor unit when the out-
door unit’s stop valve is completely closed.
2
Vacuum-purge air from the indoor unit and the connection piping.
3
After connecting the refrigerant pipes, check the connected pipes and the indoor
unit for gas leaks. (Refer to 4.4 Refrigerant pipe airtight testing method)
4
A high-performance vacuum pump is used at the stop valve service port to main-
tain a vacuum for an adequate time (at least one hour after reaching –101 kPa
(5 Torr)) in order to vacuum dry the inside of the pipes. Always check the degree
of vacuum at the gauge manifold. If there is any moisture left in the pipe, the de-
gree of vacuum is sometimes not reached with short-time vacuum application.
After vacuum drying, completely open the stop valves (both liquid and gas) for
the outdoor unit. This completely links the indoor and outdoor refrigerant circuits.
•
If the vacuum drying is inadequate, air and water vapor remain in the refriger-
ant circuits and can cause abnormal rise of high pressure, abnormal drop of
low pressure, deterioration of the refrigerating machine oil due to moisture,
etc.
•
If the stop valves are left closed and the unit is operated, the compressor and
control valves will be damaged.
•
Use a leak detector or soapy water to check for gas leaks at the pipe connec-
tion sections of the outdoor unit.
•
Do not use the refrigerant from the unit to purge air from the refrigerant lines.
•
After the valve work is completed, tighten the valve caps to the correct torque:
20 to 25 N·m (200 to 250 kgf·cm).
Failure to replace and tighten the caps may result in refrigerant leakage. In
addition, do not damage the insides of the valve caps as they act as a seal to
prevent refrigerant leakage.
5
Use sealant to seal the ends of the thermal insulation around the pipe connec-
tion sections to prevent water from entering the thermal insulation.
Summary of Contents for PUHZ-HA2
Page 12: ......