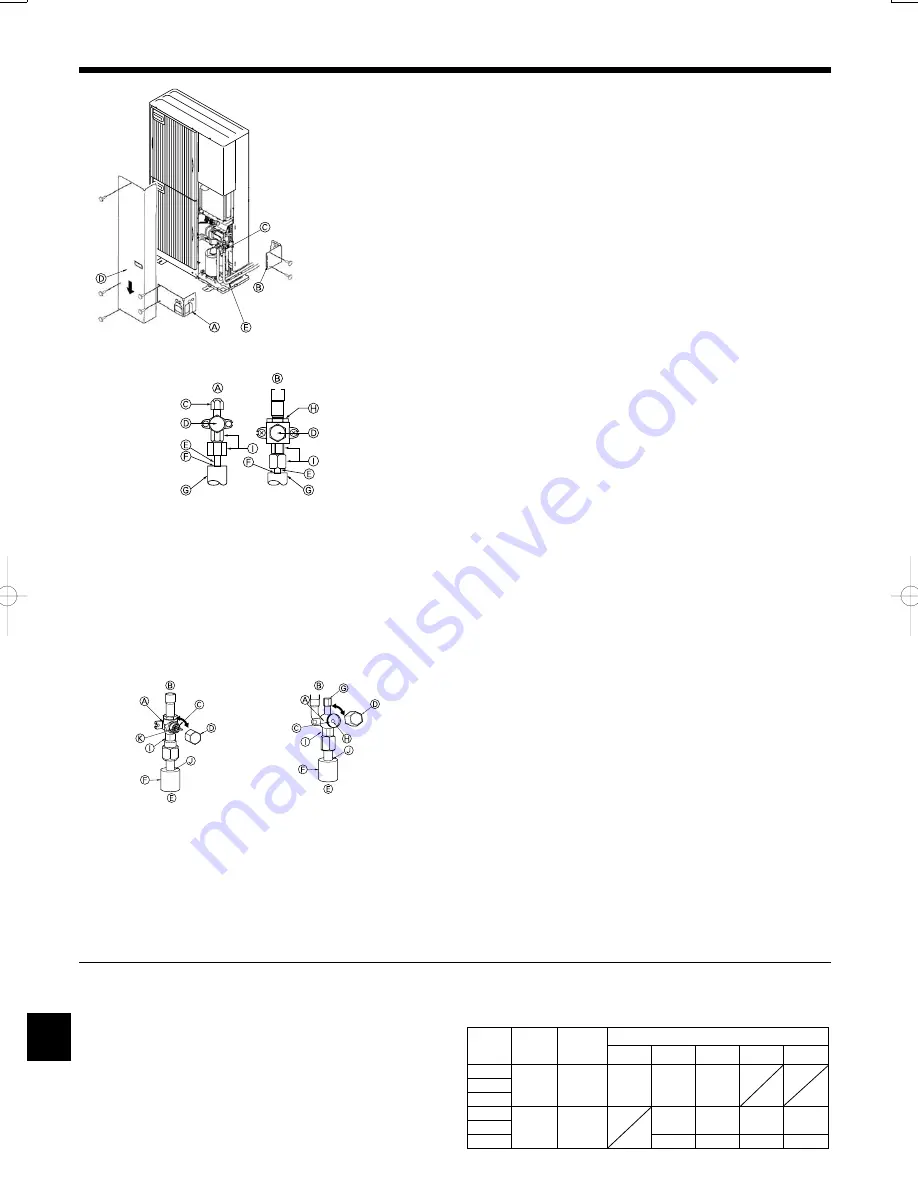
6
4. Installing the refrigerant piping
4.3. Refrigerant piping (Fig. 4-4)
Remove the service panel
D
(3 screws) and the front piping cover
A
(2 screws)
and rear piping cover
B
(2 screws).
1
Perform refrigerant piping connections for the indoor/outdoor unit when the out-
door unit’s stop valve is completely closed.
2
Vacuum-purge air from the indoor unit and the connection piping.
3
After connecting the refrigerant pipes, check the connected pipes and the indoor
unit for gas leaks. (Refer to 4.4 Refrigerant pipe airtight testing method)
4
A high-performance vacuum pump is used at the stop valve service port to main-
tain a vacuum for an adequate time (at least 1 hour after reaching –101 kPa (5
Torr)) in order to vacuum dry the inside of the pipes. Always check the degree
of vacuum at the gauge manifold. If there is any moisture left in the pipe, the de-
gree of vacuum is sometimes not reached with short-time vacuum application.
After vacuum drying, completely open the stop valves (both liquid and gas) for
the outdoor unit. This completely links the indoor and outdoor refrigerant circuits.
•
If the vacuum drying is inadequate, air and water vapor remain in the refriger-
ant circuits and can cause abnormal rise of high pressure, abnormal drop of
low pressure, deterioration of the refrigerating machine oil due to moisture,
etc.
•
If the stop valves are left closed and the unit is operated, the compressor and
control valves will be damaged.
•
Use a leak detector or soapy water to check for gas leaks at the pipe connec-
tion sections of the outdoor unit.
•
Do not use the refrigerant from the unit to purge air from the refrigerant lines.
•
After the valve work is completed, tighten the valve caps to the correct torque:
20 to 25 N·m (200 to 250 kgf·cm).
Failure to replace and tighten the caps may result in refrigerant leakage. In
addition, do not damage the insides of the valve caps as they act as a seal to
prevent refrigerant leakage.
5
Use sealant to seal the ends of the pipe cover around the pipe connection sec-
tions to prevent water from entering the thermal insulation.
4.4. Refrigerant pipe airtight testing method(Fig.4-5)
(1) Connect the testing tools.
•
Make sure the stop valves
A B
are closed and do not open them.
•
Add pressure to the refrigerant lines through the service port
C
of the liquid
stop valve
A
.
(2) Do not add pressure to the specifi ed pressure all at once; add pressure little by little.
1
Pressurize to 0.5 MPa (5 kgf/cm
2
G), wait 5 minutes, and make sure the pres-
sure does not decrease.
2
Pressurize to 1.5 MPa (15 kgf/cm
2
G), wait 5 minutes, and make sure the
pressure does not decrease.
3
Pressurize to 4.15 MPa (41.5 kgf/cm
2
G) and measure the surrounding tem-
perature and refrigerant pressure.
(3) If the specifi ed pressure holds for about one day and does not decrease, the
pipes have passed the test and there are no leaks.
•
If the surrounding temperature changes by 1 °C, the pressure will change by
about 0.01 MPa (0.1 kgf/cm
2
G). Make the necessary corrections.
(4) If the pressure decreases in steps (2) or (3), there is a gas leak. Look for the
source of the gas leak.
4.5. Stop valve opening method
The stop valve opening method varies according to the outdoor unit model. Use the
appropriate method to open the stop valves.
(1) Gas side(Fig. 4-6)
1
Remove the cap, pull the handle toward you and rotate 1/4 turn in a counter-
clockwise direction to open.
2
Make sure that the stop valve is open comletely,push in the handle and rotate
the cap back to its original position.
(2) Liquid side(Fig. 4-7)
1
Remove the cap and turn the valve rod counterclockwise as far as it will go
with the use of a 4 mm hexagonal wrench. Stop turning when it hits the stop-
per.
(ø9.52: Approximately 10 revolutions)
2
Make sure that the stop valve is open completely and rotate the cap back to
its original position.
Refrigerant pipes are protectively wrapped
• The pipes can be protectively wrapped up to a diameter of ø90 before or after
connecting the pipes. Cut out the knockout in the pipe cover following the
groove and wrap the pipes.
Pipe inlet gap
• Use putty or sealant to seal the pipe inlet around the pipes so that no gaps re-
main. (If the gaps are not closed, noise may be emitted or water and dust will
enter the unit and breakdown may result.)
•
Be careful when installing multiple units. Connecting to an incorrect indoor unit
can lead to abnormally high pressure and have a serious effect on operation
performance.
4.6. Addition of refrigerant
•
Additional charging is not necessary if the pipe length does not exceed 20 m for
BP100-BP140 and 30 m for BP170-BP250.
•
If the pipe length is exceeded, charge the unit with additional R410A refrigerant
according to the permitted pipe lengths in the following table.
*
When the unit is stopped, charge the unit with the additional refrigerant
through the liquid stop valve after the pipe extensions and indoor unit have
been vacuumized.
When the unit is operating, add refrigerant to the gas check valve using a
safety charger. Do not add liquid refrigerant directly to the check valve.
*
After charging the unit with refrigerant, note the added refrigerant amount
on the service label (attached to the unit).
Refer to the “1.5. Using R410A refrigerant air conditioners” for more infor-
mation.
Models
Permitted
pipe
length
Permitted
vertical
difference
Additional refrigerant charging amount
21-30m
31-40m
41-50m
51-60m
61-70m
BP100
~50m
~30m
0.6kg
1.2kg
1.8kg
BP125
BP140
BP170
~70m
~30m
0.9kg
1.8kg
2.7kg
3.6kg
BP200
BP250
1.2kg
2.4kg
3.6kg
4.8kg
A
Front piping cover
B
Piping cover
C
Stop valve
D
Service panel
E
Bend radius : 100 mm-150 mm
Fig. 4-4
A
Stop valve <Liquid side>
B
Stop valve <Gas side>
C
Service port
D
Open/Close section
E
Local pipe
F
Seal section
(Seal the end of the heat insulation
material at the pipe connection section
with whatever seal material you have on
hand so that water does not infi ltrate the
heat insulation material.)
G
Pipe cover
H
Do not use a wrench here.
Refrigerant leakage may result.
I
Double spanner section
(Do not apply a spanner other than to
this section. Doing so would cause
refrigerant leaks.)
A
Valve
B
Unit side
C
Operation section
D
Cap
E
Local pipe side
F
Pipe cover
G
Service port
H
Wrench hole
I
Double spanner section
(Do not apply a spanner other than to this section. Doing
so would cause refrigerant leaks.)
J
Seal section
(Seal the end of the heat insulation material at the pipe connection
section with whatever seal material you have on hand
so that water does not infi ltrate the heat insulation material.)
K
Handle
Fig. 4-5
Fig. 4-6
Fig. 4-7
(1)
(2)