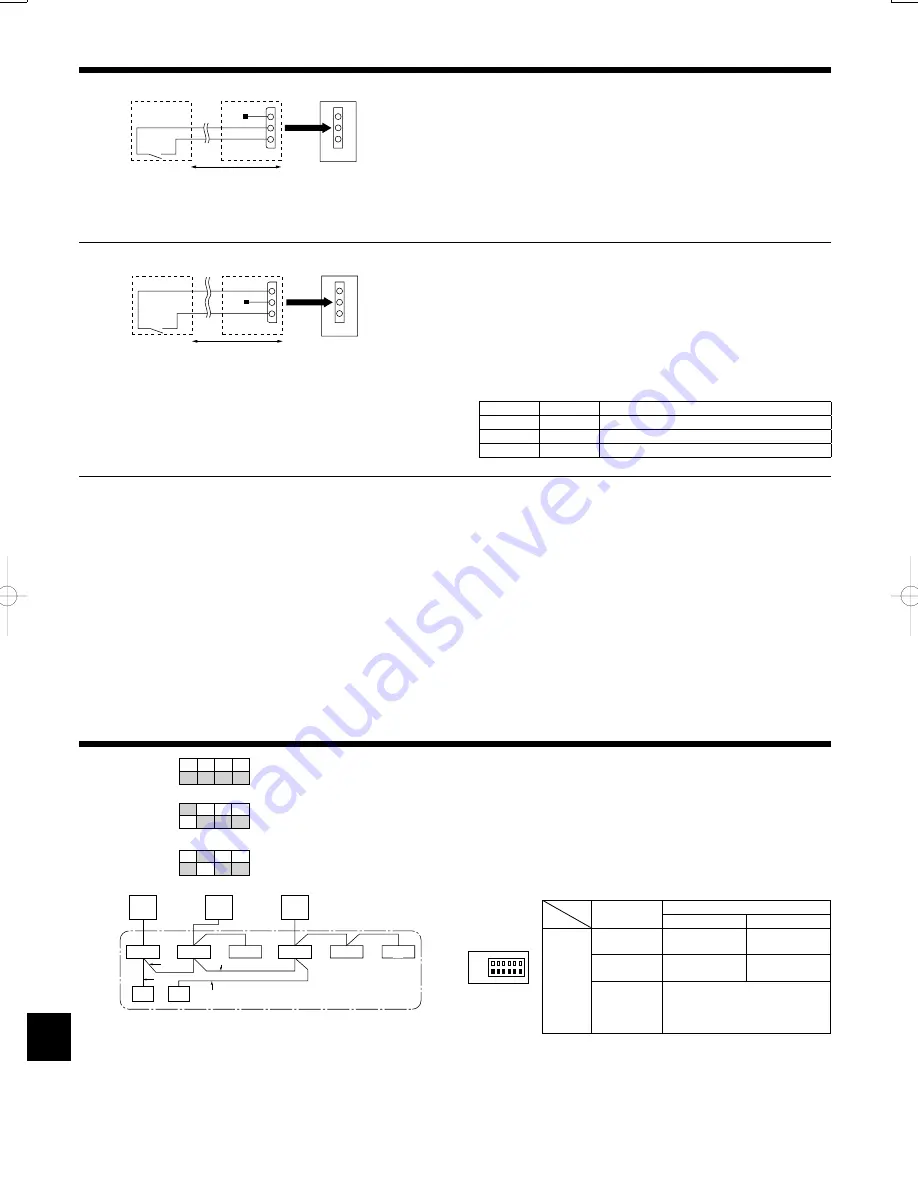
10
1 2 3 4 5 6
8. Special Functions
8.1. Low noise mode (on-site modifi cation) (Fig. 8-1)
By performing the following modifi cation, operation noise of the outdoor unit can be
reduced by about 3-4 dB.
The low noise mode will be activated when a commercially available timer or the
contact input of an ON/OFF switch is added to the CNDM connector (option) on the
control board of the outdoor unit.
•
The ability varies according to the outdoor temperature and conditions, etc.
1
Complete the circuit as shown when using the external input adapter
(PAC-SC36NA). (Option)
2
SW1 ON: Low noise mode
SW1 OFF: Normal operation
A
Circuit diagram example (low noise
mode)
B
On-site arrangement
C
External input adapter (PAC-SC36NA)
D
Outdoor unit control board
E
Max. 10 m
8.3. Refrigerant collecting (pump down)
Perform the following procedures to collect the refrigerant when moving the indoor
unit or the outdoor unit.
1
Supply power (circuit breaker).
*
When power is supplied, make sure that “CENTRALLY CONTROLLED” is not
displayed on the remote controller. If “CENTRALLY CONTROLLED” is dis-
played, the refrigerant collecting (pump down) cannot be completed normally.
2
After the gas stop valve is closed, set the SWP switch on the control board of the
outdoor unit to ON. The compressor (outdoor unit) and ventilators (indoor and
outdoor units) start operating and refrigerant collecting operation begins. LED1
and LED2 on the control board of the outdoor unit are lit.
*
Only set the SWP switch (push-button type) to ON if the unit is stopped. How-
ever, even if the unit is stopped and the SWP switch is set to ON less than
three minutes after the compressor stops, the refrigerant collecting operation
cannot be performed. Wait until compressor has been stopped for 3 minutes
and then set the SWP switch to ON again.
* Set the refrigerant address using the DIP switch of the outdoor unit.
1
Wiring from the Remote Control
This wire is connected to TB5 (terminal board for remote controller) of the indoor
unit (non-polar).
2
When a Different Refrigerant System Grouping is Used.
Up to 16 refrigerant systems can be controlled as one group using the slim MA re-
mote controller.
Note:
In single refrigerant system (twin/triple), there is no need of wiring
2
.
A
Outdoor unit
B
Indoor unit
C
Master remote controller
D
Subordinate remote controller
E
Standard 1:1 (Refrigerant address = 00)
F
Simultaneous twin (Refrigerant address = 01)
G
Simultaneous triple (Refrigerant address = 02)
E
SW 1 - 3 ~ 6
F
SW 1 - 3 ~ 6
G
SW 1 - 3 ~ 6
Red
A
B
C
D
E
SW1
CNDM
3
1
Fig. 8-1
3
Because the unit automatically stops in about 2 to 3 minutes after the refrigerant
collecting operation (LED1 and LED2 are lit), be sure to quickly close the gas
stop valve. When LED1 and LED2 are lit and the outdoor unit is stopped, open
the liquid stop valve completely, and then repeat step
2
after 3 minutes have
passed.
*
If the refrigerant collecting operation has been completed normally (LED1 and
LED2 are lit), the unit will remain stopped until the power supply is turned off.
4
Turn off the power supply (circuit breaker).
* Note that when the length of the extension piping is long, it may no be pos-
sible to perform a pump-down operation.When performing the pump-down
operation,make sure that the low pressure is lowered to near 0 MPa( gauge).
9. System control (Fig. 9-1)
Fig. 9-1
SW1
Function table
<SW1>
Function
Operation according to switch setting
ON
OFF
SW1
function
settings
1 Compulsory
defrosting
Start
Normal
2 Error history
clear
Clear
Normal
3
4
5
6
Refrigerant
system ad-
dress setting
Settings for outdoor unit addresses
0 to 15
TB1
A
G
F
A
A
E
B
B
B
B
B
B
D
C
TB1
TB1
TB4
TB5
TB4
TB5
TB4
TB4
TB5
TB4
TB4
1
1
2
ON
OFF
ON
OFF
ON
OFF
3 4 5 6
3 4 5 6
3 4 5 6
Brown
Orange
ON
OFF
2
A
Circuit diagram example (Demand
function)
B
On-site arrangement
C
External input adapter (PAC-SC36NA)
D
Outdoor unit control board
E
Max. 10 m
8.2. Demand function (on-site modifi cation) (Fig. 8-2)
By performing the following modifi cation, energy consumption can be reduced to 0
–100% of the normal consumption.
The demand function will be activated when a commercially available timer or the
contact input of an ON/OFF switch is added to the CNDM connector (option) on the
control board of the outdoor unit.
1
Complete the circuit as shown when using the external input adapter
(PAC-SC36NA). (Option)
2
By setting SW 7-1 and SW 7-2 on the control board of the outdoor unit, the ener-
gy consumption (compared to the normal consumption) can be limited as shown
below.
SW7-1
SW7-2
Energy consumption (SW2 ON)
OFF
OFF
0% (Stop)
ON
OFF
50%
OFF
ON
75%
Red
A
B
C
D
E
SW2
CNDM
3
1
Brown
Orange
Fig. 8-2