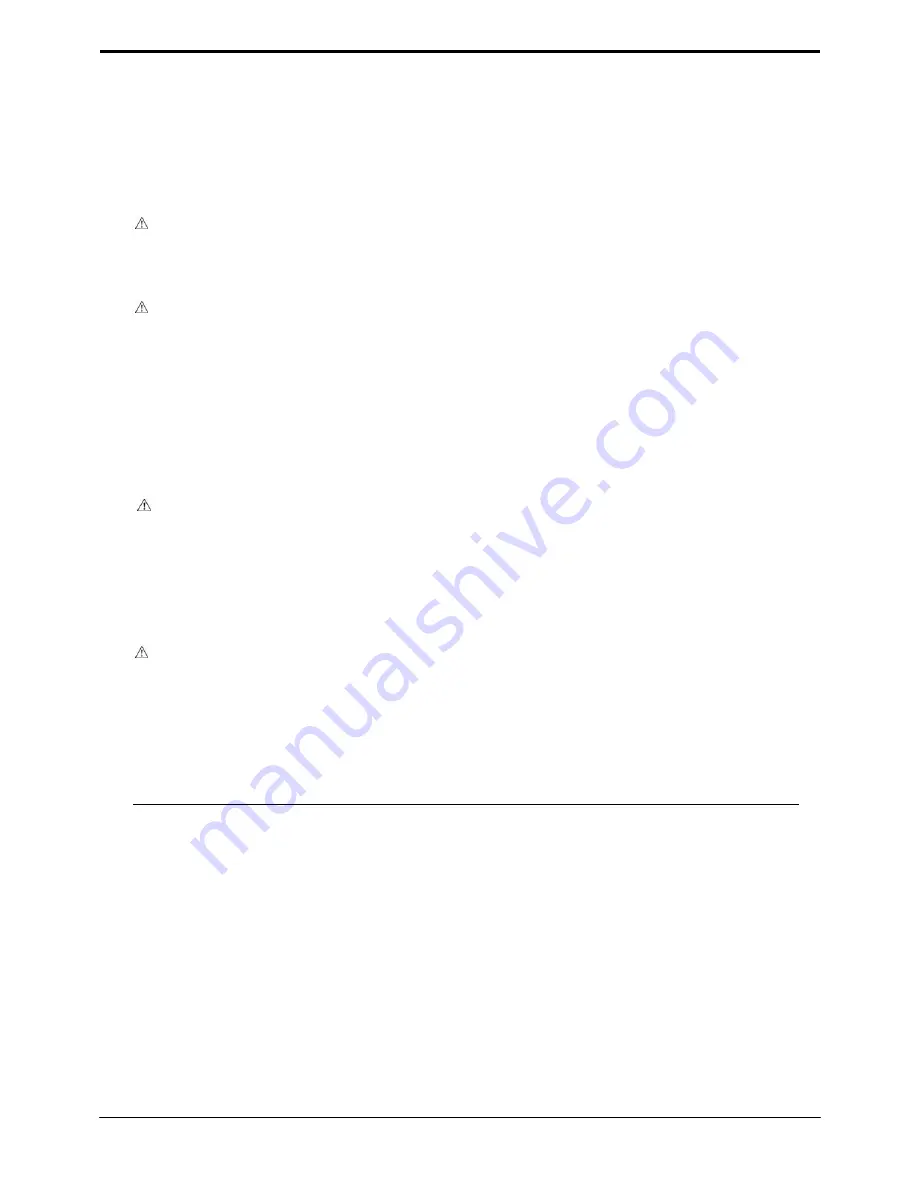
14
[Fig. 7.2.1] (P.6) M A Remote controller
[Fig. 7.2.2] (P.6) M-NET Remote controller
•
DC 9 to 13 V between 1 and 2 (MA remote controller)
•
DC 24 to 30 V between MI and M2 (M-NET remote controller)
[Fig. 7.2.3] (P.6) MA Remote controller
[Fig. 7.2.4]
(P.6) M-NET Remote controller
•
The MA remote controller and the M-NET remote controller cannot be used at the same time or interchangeably.
Note:
Ensure that the wiring is not pinched when fitting the terminal box cover. Pinching the wiring may cut it.
Caution:
Install wiring so that it is not tight and under tension. Wiring under tension may break, or overheat and burn
.
•
Fix power source wiring to control box by using buffer bushing for tensile force. (PG connection or the like.) Connect transmission wiring to
transmission terminal block through the knockout hole of control box using ordinary bushing.
•
After wiring is complete, make sure again that there is no slack on the connections, and attach the cover onto the control box in the reverse
order from removal.
Caution:
Wire the power supply so that no tension is imparted. Otherwise disconnection, heating or fire result.
7.3. Connecting thermistor cable TH1H
8.3.1 Connecting thermistor cables
Pull the end of the wire through the bunch of wires (Thermistor) at the bottom of the controller.
Connect the thermistor to the water temperature terminals T1 and T2 on the terminal block.
When the lead wire is too long, cut it to the appropriate length.
Take proper measures not to miswire.
Note: If using more than one application (under floor heating / under floor cooling / domestic hot water), an ACH1 is required. See manual for set up of
thermistor cables.
Caution:
Do not route the thermistor cables together with power cables.
7.4. Connecting distant signal line
Pull the wires for operation command, for operation signal and error signal through the flushing end glands (Distant signal) at the bottom of the
controller.
Connect each wire to operation command: A1 and A2, to operation signal: D1 and D2, and to error signal: D11 and D12.
Notes:
•
After connecting each wire to the terminal, tighten each nut tightly through which the w ire runs .
•
Check that the bu nch o f wires do n o t come o ff even if they are pulled strongly.
Caution:
•
After the wiring work is completed, mount the inner cover. T ighten the screws.
•
Operation signal cables,
Error
signal cables and Operation command cables must be routed at a distance of at least 20 cm
from all other cables.
•
When Operation signal, Error signal and distant signal are taken out, remove the plug inside the bunch of wires.
•
Wind the supplied tube around the wire according to the size and number of the wire. If the wire comes off the tightened
bunch of wires, wind the insulation tape around the wire to make the wire thicker.
[Fig. 7.4.1] (P.6)
8. Setting switches
8.1. Setting Addresses and Dip Switch Settings
Note: If an ON/OFF volt free signal and heating and cooling signal is needed, an alternative design is possible. Please see ACH1 install
manual for details.
•
In order to increase the output temperature of the water it is necessary to increase the condensing temperature of the Heat Pump. This is
achieved by setting a Dip Switch as follows.
PUMY-P100/125/140YMH, PUMY-P100125140VMH, SW 6-6 to the ON position.
All City Multi P200 and above, SW3-7 to the ON position.
•
When connecting the PQFY to a heat pump with heating and cooling required it is necessary to use a PAR21 in auto mode (See commissioning
for further details) and to set the auto changeover dip switch in the outdoor unit.
PUMY Dip Switch SW2-5
PUHY Dip Switch SW 4-8
•
A separate controller is also required “ACH1”.
•
It is necessary to set the Auto re-start dip switch setting on the PQFY PCB SW 1-9 ON.