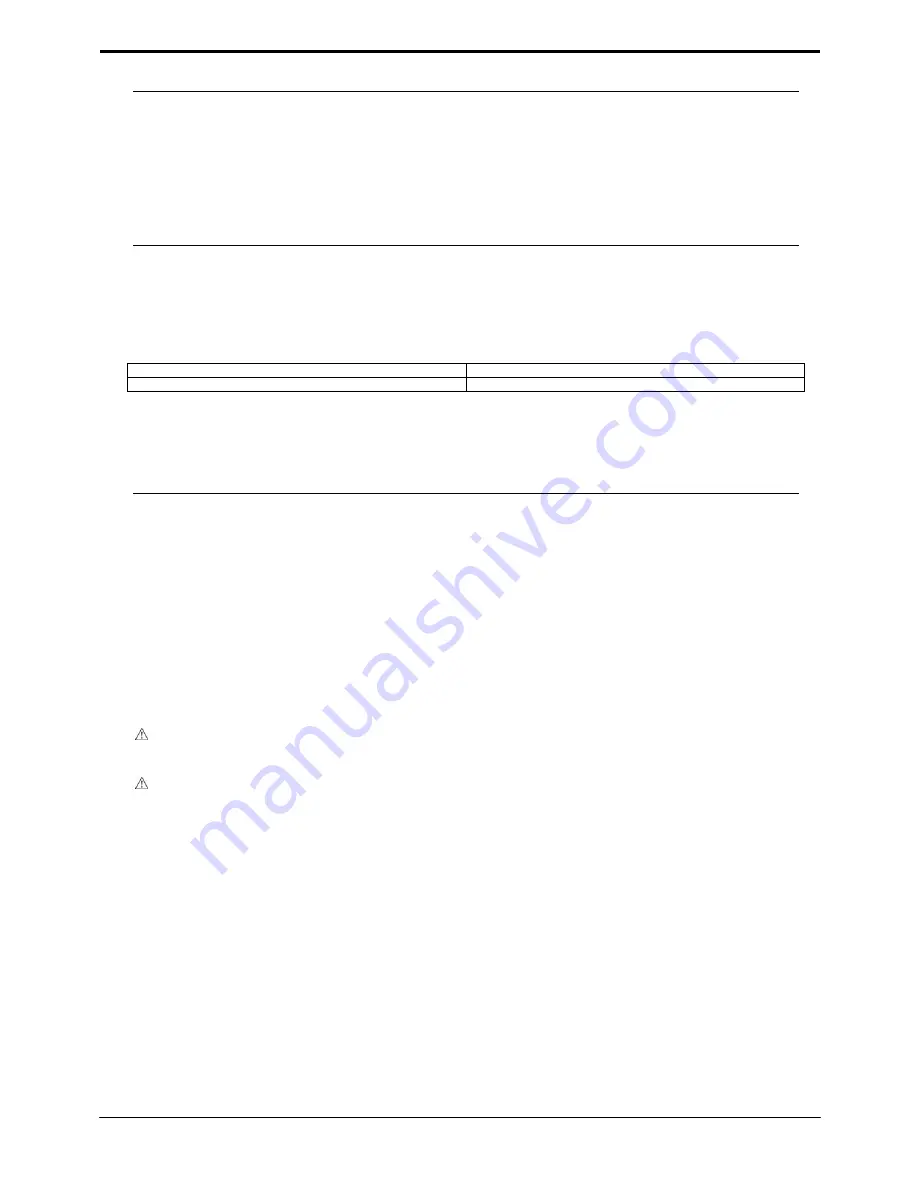
10
3. Selecting an installation site
•
Avoid locations in direct sunlight.
•
Avoid locations exposed to steam or oil vapour.
•
Avoid locations where combustible gas may leak, settle or be generated.
•
Avoid installation near machines emitting high-frequency waves.
•
Avoid places where acidic solutions are frequently handled.
•
Avoid places where sulphur-based or other sprays are frequently used.
•
Avoid areas of high humidity (when cooling operation is required)
•
Install inside in a water proof housing (field Supplied)
4. Refrigerant pipe specifications
•
To avoid dew formation, provide sufficient anti-sweating and insulating work to the refrigerant pipes.
•
When using commercially available refrigerant pipes, be sure to wind commercially available insulating material (with a heat-resisting
temperature of more than 100 °C and thickness given below) onto both liquid and gas pipes. Be also sure to wind commercially available insulating
material (with a form polyethylene's specific gravity of 0.03 and thickness given below) onto all pipes which pass through rooms.
The below thicknesses of insulating material should be used for the refrigerant piping.
Pipe Size
Insulation thickness
6.4 mm to 25.4 mm
More than 10 mm
•
If the unit is used on a particularly high building and under conditions of high temperature and humidity, it is necessary to insulate to a greater
thickness than that given in the table above.
•
If there are insulation manufacturer’s specifications these should be followed.
5. Connecting refrigerant pipes
5.1. Refrigerant piping work
Piping work must be done in accordance with the installation manuals for both outdoor unit and where applicable the BC controller.
•
Heat Pump Series, PUMY-P100/125/140YMH, PUMY-P100/125/140VMH, PUHY-P200/250/300/350/400/500/650YGM-A are designed to
operate in a system with two refrigerant pipes one liquid and one gas connecting from the outdoor unit to the indoor unit.
•
R2 Series, PURY-P200/250/300/350/400/500/650YGM-A are designed to operate in a system where the refrigerant pipe from an outdoor unit
is received by BC controller and branches at the BC controller to connect between indoor units, again liquid and gas.
•
For constraints on pipe length and allowable difference of elevation, refer to the outdoor unit manual.
Cautions on refrigerant piping
Be sure to use non-oxidative brazing to ensure that no fo reign matter or moisture enter into th e pipe.
Be sure to apply refrigerating machine oil over the flare connection seating surface and tighten the connection using a double
spanner.
Provide a metal brace to support the refrigerant pipe so that no load is imported to the indoor unit and pipe. This metal
brace should be provided 50 mm away from the indoor unit's flare connection.
Warning:
When installing and moving the unit, do not charge it with refrigerant other than the refrigerant specified on the unit.
- Mixing of a different refrigerant, air, etc. may cause the refrigerant cycle to malfunction and result in severe damage.
Caution:
•
Use refrigerant piping made of C1220 (CU-DHP) phosphorus deoxidized copper as specified in the JIS H3300 "Copper and copper
alloy seamless pipes and tubes". In addition, be sure that the inner and outer surfaces of the pipes are clean and free of
hazardous sulphur, oxides, dust/dirt, shaving particles, oils, mo isture, o r any other contaminant.
•
Never use existing refrigerant piping.
- The large amount of chlorine in conventional refrigerant and refrigerator oil in the existing piping will cause the new refrigerant to
deteriorate.
•
Store the piping to be used during installation indoors and keep both e nds of the p iping sealed until just before
brazing.
- If dust, dirt, or water gets into the refrigerant cycle, the oil will deteriorate and the compressor may fail.
•
Use ester oil, ether oil or alkylbenzene (small amount) as the refrigerator o il to coat flares and flange connections. (For models
using R410A or R407C)
-
The refrigerant used in the unit is highly hygroscopic and mixes with water and will degrade the refrigerator oil.
Cautions on water piping and connection.
Ensure that all water piping and the connection to the unit is in accordance with the relevant government guidelines and legislation.
Ensure that sufficient allowance has been made for the expansion of the water in the design of the water piping.
Ensure that national Legionella legislation has been strictly adhered to at all times for the system design.
Ensure that sufficient pressure relief has been allowed for in the design of the water circuit.