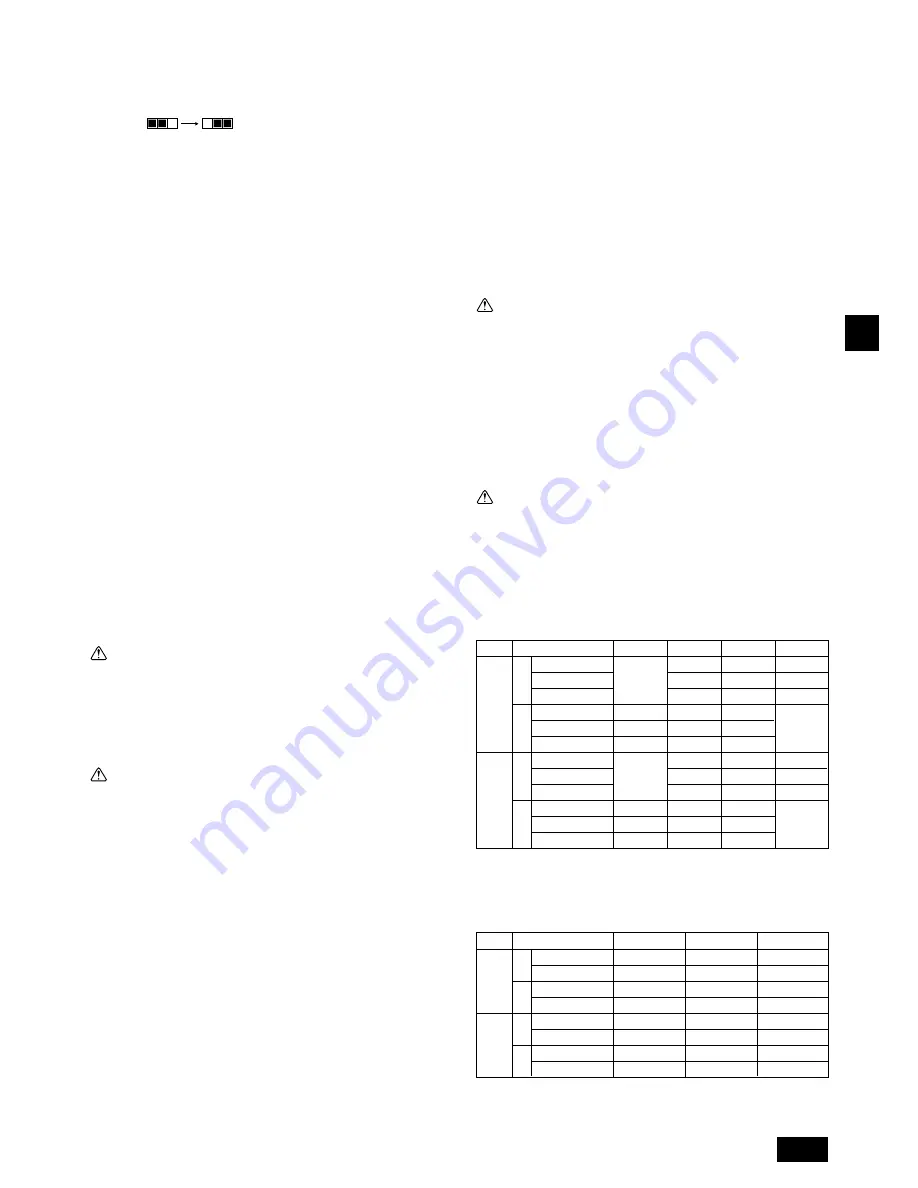
11
GB
D
F
E
I
NL
P
GR
RU
TR
GB
GB
GB
GB
GB
•
Backup operation
Even when the electrical work has not been completed, the fan and the drain
pump can be operated by connecting the jumper (SWE) on the control board
to the ON-side and energizing the terminal block.
SWE
SWE
OFF
ON
OFF
ON
Reconnect the SWE on the control board to the OFF-side upon completion of
all work.
9.2. Connecting remote controller, indoor
and outdoor transmission cables
(Remote contoroller is optionally available.)
•
Connect indoor unit TB5 and outdoor unit TB3. (Non-polarized 2-wire)
The “S” on indoor unit TB5 is a shielding wire connection. For specifications
about the connecting cables, refer to the outdoor unit installation manual.
•
Install a remote controller following the manual supplied with the remote con-
troller.
•
Connect the “1” and “2” on indoor unit TB15 to a MA remote controller. (Non-
polarized 2-wire)
•
Connect the “M1” and “M2” on indoor unit TB5 to a M-NET remote controller.
(Non-polarized 2-wire)
•
Connect the remote controller’s transmission cable within 10 m using a 0.75 mm
2
core cable. If the distance is more than 10 m, use a 1.25 mm
2
junction cable.
[Fig. 9.2.1]
(P.4) MA Remote controller
[Fig. 9.2.2]
(P.4) M-NET Remote controller
A
Terminal block for indoor transmission cable
B
Terminal block for outdoor transmission cable
C
Remote controller
•
DC 9 to 13 V between 1 and 2 (MA remote controller)
•
DC 24 to 30 V between M1 and M2 (M-NET remote controller)
[Fig. 9.2.3]
(P.4) MA Remote controller
[Fig. 9.2.4]
(P.4) M-NET Remote controller
A
Non-polarized
B
Upper level (TB15)
C
Remote Controller
D
Lower level (TB5)
•
The MA remote controller and the M-NET remote controller cannot be used at
the same time or interchangeably.
Note:
Ensure that the wiring is not pinched when fitting the terminal box cover.
Pinching the wiring may cut it.
Caution:
Install wiring so that it is not tight and under tension. Wiring under tension
may break, or overheat and burn.
•
Fix power source wiring to control box by using buffer bushing for tensile force.
(PG connection or the like.) Connect transmission wiring to transmission ter-
minal block through the knockout hole of control box using ordinary bushing.
•
After wiring is complete, make sure again that there is no slack on the connec-
tions, and attach the cover onto the control box in the reverse order removal.
Caution:
Wire the power supply so that no tension is imparted. Otherwise disconnec-
tion, heating or fire result.
9.3. Connecting electrical connections
Verify that the model name on the operating instructions on the cover of the control
box is the same as the model name on the nameplate.
Step 1
Remove the screws holding the terminal box cover in place.
•
Type 80 · 140 (2 screws)
Fig.1
•
Type 200 · 250 (3 screws)
Fig.2
[Fig. 9.3.1] (P. 4)
Fig.1
Fig.2
A
Screws
B
Terminal box cover
C
Control box cover
D
Control box
Note:
Ensure that the wiring is not pinched when fitting the terminal box cover.
Pinching the wiring may cut it.
Caution:
Install wiring so that it is not tight and under tension. Wiring under tension
may break, or overheat and burn.
•
Fix power source wiring to control box by using buffer bushing for tensile force.
(PG connection or the like.) Connect transmission wiring to transmission ter-
minal block through the knockout hole of control box using ordinary bushing.
•
After wiring is complete, make sure again that there is no slack on the connec-
tions, and attach the cover onto the control box in the reverse order removal.
[Fig. 9.3.2] (P. 4)
A
To prevent external tensile force from applying to the wiring connection section of
power source terminal block use buffer bushing like PG connection or the like.
B
Power source wiring
C
Tensile force
D
Use ordinary bushing
E
Transmission wiring
Caution:
Wire the power supply so that no tension is imparted. Otherwise disconnec-
tion, heating or fire result.
9.4. Selecting the static pressure
Type 80 · 140
The external static pressure can be changed over as required. For the selection of
the static pressure, insert an attachment between the connector of the motor lead
wire and the control box.
The relationship among the attachment, voltage and the external static pressure is
shown below.
Red
White
Blue
Attachment
50
Hz
60
Hz
50
Hz
60
Hz
80
140
Red
White
Blue
Red
White
Blue
Red
White
Blue
208 V
–
170
85
35
–
170
85
35
Type
220 V
190
115
40
190
115
40
190
115
50
190
115
50
230 V
210
130
50
220
130
50
220
130
60
220
130
60
240 V
220
170
80
–
240
170
100
–
Type 200 · 250
The external static pressure can be changed over as required.
For the selection of static pressure, replace the connector of the motor lead wire
by the connector (blue) inside the control box for insertion.
The relationship among the connector, voltage and the external static pressure is
shown below.
Connector
Type
380 V
400 V
415 V
White
Blue
White
Blue
White
Blue
White
Blue
200
140
200
140
190
110
190
110
210
150
210
150
200
120
200
120
220
160
220
160
210
130
210
130
50
Hz
60
Hz
50
Hz
60
Hz
200
250
(Unit: Pa)
(Unit: Pa)
WT04313X06_en.p65
2012.8.22, 3:58 PM
11