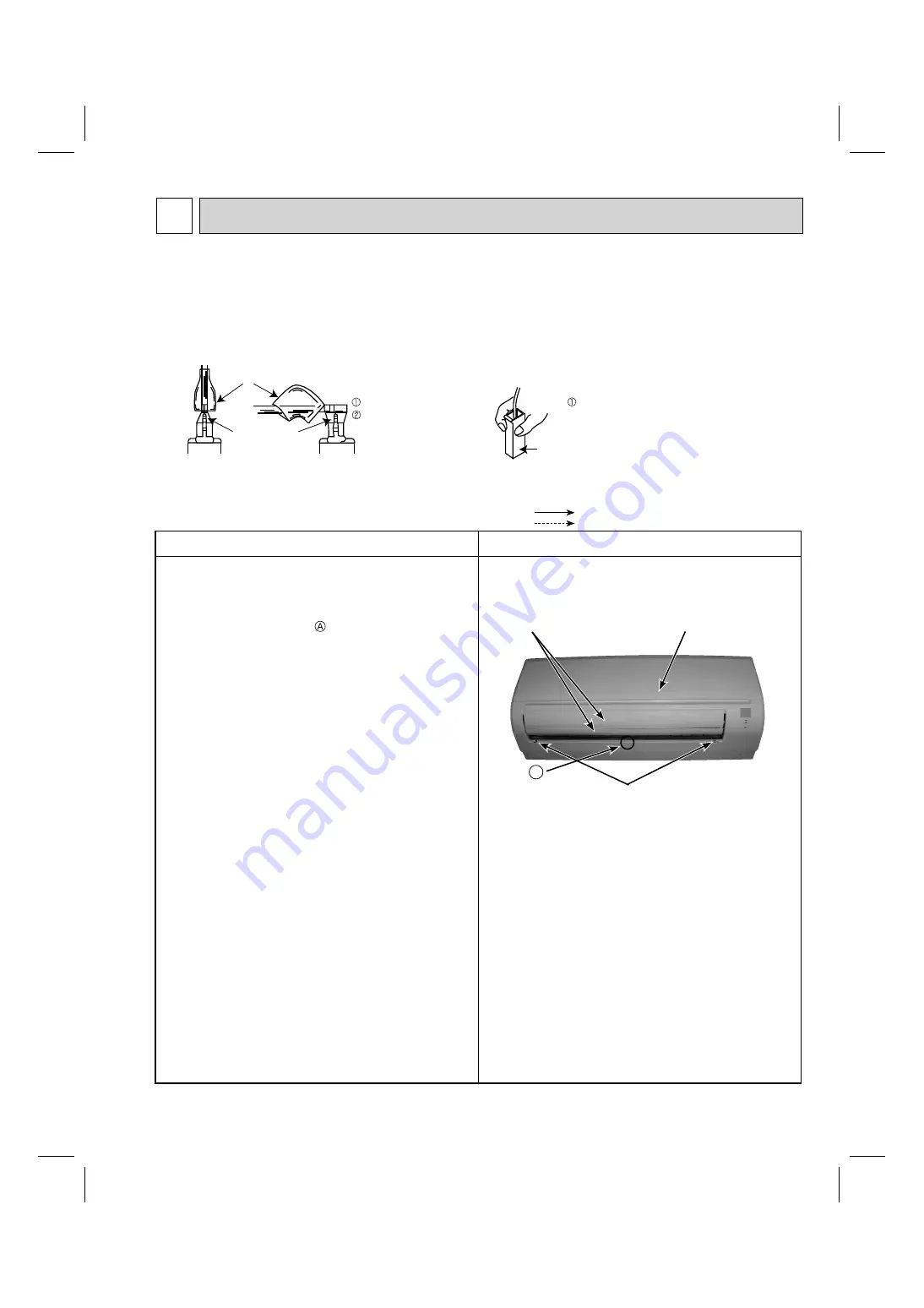
10-1. MSZ-JP09WA MSZ-JP12WA
NOTE:
Turn OFF the power supply before disassembly.
OPERATING PROCEDURE
PHOTOS/FIGURES
1. Removing the panel
(1) Remove the horizontal vanes.
(2) Remove the screw caps of the panel. Remove the
screws of the panel.
(3) Unhook the lower part ( ) of the panel.
(4) Hold the lower part of both ends of the panel and pull
it
slightly toward you, and then remove the panel by
pushing it upward.
Photo 1
27
Screws of the panel
Front panel
Horizontal vanes
A
(1) Slide the sleeve and check if there is a locking lever or not.
(2) The terminal with this connector shown below
has the locking mechanism.
Slide the sleeve.
Pull the terminal while
pushing the locking
lever.
Hold the sleeve, and
pull out the terminal
slowly.
Connector
Sleeve
Locking lever
<Detaching method of the terminal with locking mechanism>
The terminal which has the locking mechanism can be detached as shown below.
There are 2 types of terminals with locking mechanisms.
The terminal without locking mechanism can be detached by pulling it out.
Check the shape of the terminal before detaching.
DISASSEMBLY INSTRUCTIONS
10
: Indicates the visible parts in the photos/
fi
gures.
: Indicates the invisible parts in the photos/
fi
gures.
OBH820