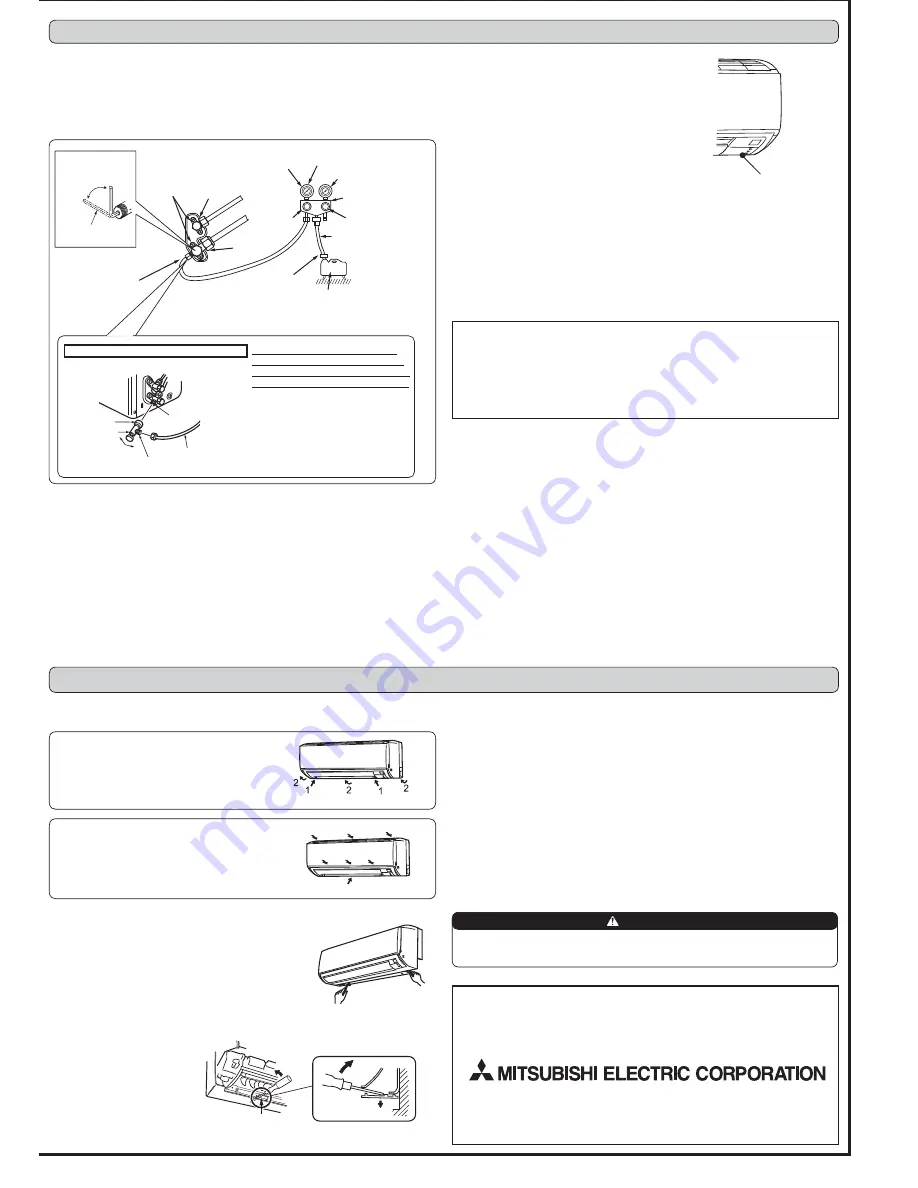
4-1. PURGING PROCEDURES AND LEAK TEST
1) Remove service port cap of stop valve on the side of the outdoor unit gas pipe. (The
stop valve will not work in its initial state fresh out of the factory, totally closed with cap
on.)
2) Connect gauge manifold valve and vacuum pump to service port of stop valve on the
gas pipe side of the outdoor unit.
4-2. TEST RUN
1) Press the E.O. SW once for COOL, and twice for HEAT
operation. Test run will be performed for 30 minutes. If
the upper lamp of the operation indicator blinks every 0.5
seconds, inspect the indoor/outdoor unit connecting wire
(A) for mis-wiring. After the test run, emergency mode
(set temperature 24ºC) will start.
2) To stop operation, press the E.O. SW several times until
all LED lamps turn off. Refer to operating instructions for
details.
Checking the remote (infrared) signal reception
Press the ON/OFF button on the remote controller (4) and
check that an electronic sound is heard from the indoor
unit. Press the ON/OFF button again to turn the air conditioner off.
• Once the compressor stops, the restart preventive device operates so the compressor
will not operate for 3 minutes to protect the air conditioner.
4-3. AUTO RESTART FUNCTION
This product is equipped with an auto restart function. When the power supply is stopped
during operation, such as during blackouts, the function automatically starts operation in
the previous setting once the power supply is resumed. (Refer to the operating instruc-
tions for details.)
5-1. REMOVING AND INSTALLING THE PANEL ASSEMBLY
5-3. PUMPING DOWN
When relocating or disposing of the air conditioner, pump down the system following the
procedure below so that no refrigerant is released into the atmosphere.
1) Connect the gauge manifold valve to the service port of the stop valve on the gas pipe
side of the outdoor unit.
2) Fully close the stop valve on the liquid pipe side of the outdoor unit.
3) Close the stop valve on the gas pipe side of the outdoor unit almost completely so that
it can be easily closed fully when the pressure gauge shows 0 MPa [Gauge] (0 kgf/
cm
2
).
4) Start the emergency COOL operation.
To start the emergency operation in COOL mode, disconnect the power supply plug
and/or turn off the breaker. After 15 seconds, connect the power supply plug and/or
turn on the breaker, and then press the E.O. SW once. (The emergency COOL
operation can be performed continuously for up to 30 minutes.)
5) Fully close the stop valve on the gas pipe side of the outdoor unit when the pressure
gauge shows 0.05 to 0 MPa [Gauge] (approx. 0.5 to 0 kgf/cm
2
).
6) Stop the emergency COOL operation.
Press the E.O. SW twice to stop the operation.
5-2. REMOVING THE INDOOR UNIT
Remove the bottom of the indoor unit from the installation
plate.
When releasing the corner part, release both left and right
bottom corner part of indoor unit and pull it downward and
forward as shown in the figure on the right.
If the above method cannot be used
Remove the panel and insert hexagonal wrenches and right as shown in the figure below,
then push unit is lowered and the hooks are released.
Removal procedure
1) Remove the 2 screws which fix the panel assem-
bly.
2) Remove the panel assembly. Be sure to remove
its bottom end first.
Installation procedure
1) Install the panel assembly following the removal
procedure in reverse.
2) Be sure to press the positions as indicated by the
arrows in order to attach the assembly completely
to the unit.
Stop valve for
GAS
Stop valve cap
(Torque 19.6 to
29.4 N•m, 200
to 300 kgf▪cm)
Vacuum pump (or the vacuum
pump with the function to
prevent the back flow)
Gauge manifold valve
(for R410A)
Compound pressure gauge
(for R410A)
-0.101MPa
(-760 mmHg)
Handle
Low
Handle High
Adapter for pre-
venting the back
flow
Charge hose
(for R410A)
*Close
*Open
Hexagonal wrench
Precautions when using the control valve
When attaching the control valve
to the service port, valve core may
deform or loosen if excess pressure
is applied. This may cause gas leak.
Service port
Charge hose
Body
Close
Open
Control valve
A
When attaching the control valve to
the service port, make sure that the
valve core is in closed position, and
then tighten part A. Do not tighten
part A or turn the body when valve
core is in open position.
Service port cap
(Torque 13.7 to
17.7 N•m, 140 to
180 kgf•cm)
*4 to 5 turns
3) Run the vacuum pump. (Vacuumize for more than 15 minutes.)
4) Check the vacuum with gauge manifold valve, then close gauge manifold valve, and
stop the vacuum pump.
5) Leave as it is for one or two minutes. Make sure pointer gauge manifold valve remains
in the same position. Confirm that pressure gauge shows –0.101 Mpa [Gauge] (–760
mmHg).
6) Remove gauge manifold valve quickly from service port of stop valve.
7) After refrigerant pipes are connected and evacuated, fully open all stop valves on both
sides of gas pipe and liquid pipe. Operating without fully opening lowers the perform-
ance and this causes trouble.
8) Refer to 1-3., and charge the prescribed amount of refrigerant if needed. Be sure to
charge slowly with liquid refrigerant. Otherwise, composition of the refrigerant in the
system may be changed and affect performance of the air conditioner.
9) Tighten cap of service port to obtain the initial status.
10) Leak test
Stop valve
for LIQUID
Caution:
• After test run or remote signal reception check, turn off the unit with the E.O. SW or
the remote controller before turning off the power supply. Not doing so will cause the
unit to start operation automatically when power supply is resumed.
To the user
• After installing the unit, make sure to explain the user about auto restart function.
• If auto restart function is unnecessary, it can be deactivated. Consult the service
representative to deactivate the function. Refer to the service manual for details.
Push
Lower
Square hole
4. PURGING PROCEDURES, LEAK TEST, AND TEST RUN
Pressure gauge
(for R410A)
5. RELOCATION AND MAINTENANCE
Emergency
operation switch
(E.O. SW)
HEAD OFFICE: TOKYO BLDG., 2-7-3, MARUNOUCHI, CHIYODA-KU, TOKYO
100-8310, JAPAN
AUTHORIZED REPRESENTATIVE IN EU:
MITSUBISHI ELECTRIC EUROPE B.V.
HARMAN HOUSE, 1 GEORGE STREET, UXBRIDGE, MIDDLESEX UB8 1QQ, U.K.
This product is designed and intended for use in the residential, commercial and
light-industrial environment.
The product at hand is based on • Low Voltage Directive 2006/95/EC
the following EU regulations:
• Electromagnetic Compatibility Directive 2004/108/
EC
4-4. EXPLANATION TO THE USER
• Using the OPERATING INSTRUCTIONS, explain to the user how to use the air condi-
tioner (how to use the remote controller, how to remove the air filters, how to remove
or put the remote controller in the remote controller holder, how to clean, precautions
for operation, etc.)
• Recommend the user to read the OPERATING INSTRUCTIONS carefully.
When pumping down the refrigerant, stop the compressor before disconnecting
the refrigerant pipes. The compressor may burst if air etc. get into it.
WARNING