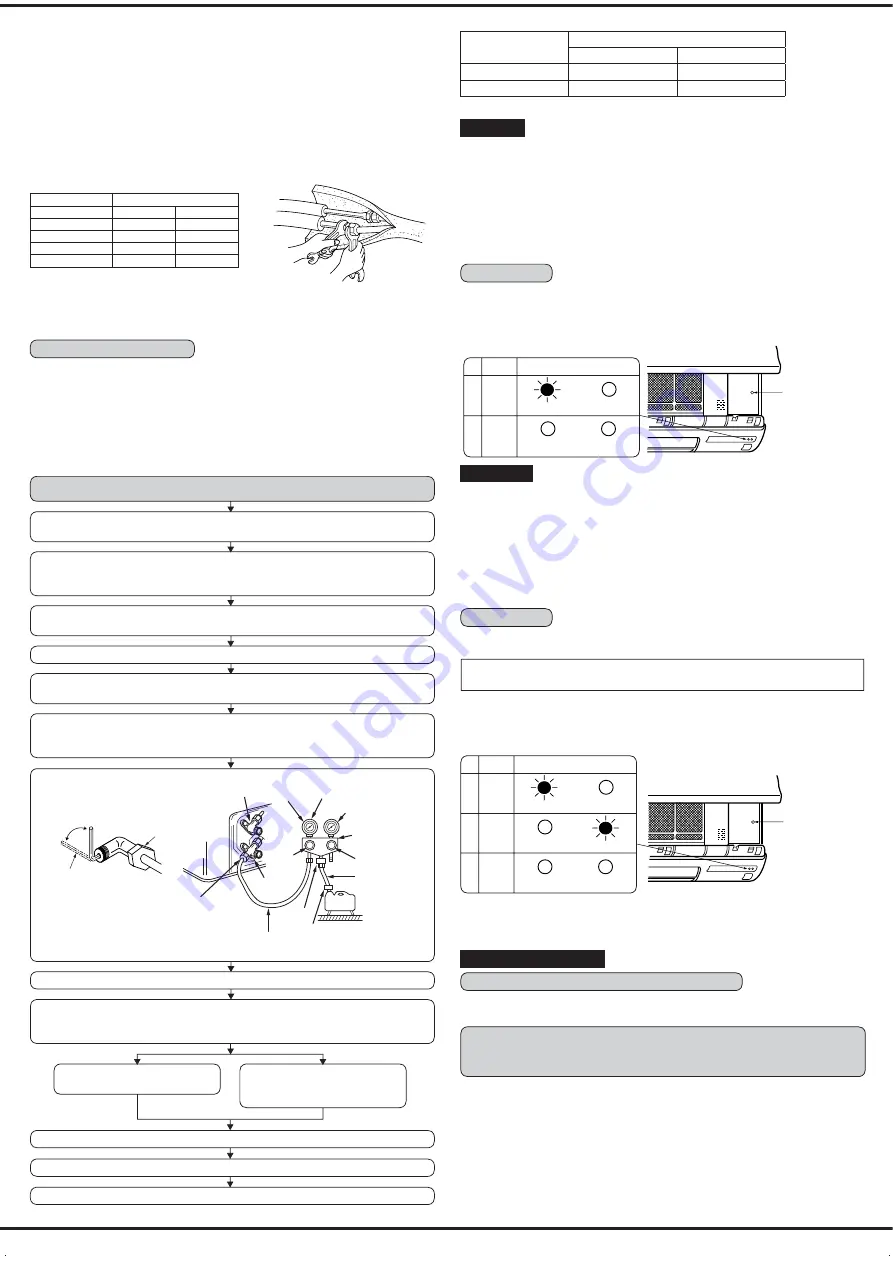
Connect the refrigerant pipes (both liquid pipe and the gas pipe) between the indoor
and the outdoor unit.
PURGING PROCEDURES
Remove the service port cap of the stop valve on the side of the outdoor unit gas pipe.
(The stop valve will not work in it initial state fresh out of the factory (totally closed with
cap on).)
Connect the gauge manifold valve and the vacuum pump to the service port of the
stop valve on the gas pipe side of the outdoor unit.
Run the vacuum pump. (Vacuumize for more than 15 minutes.)
Check the vacuum with the gauge manifold valve, then close the gauge manifold
valve, and stop the vacuum pump.
Leave as it is for one or two minutes. Make sure the pointer gauge manifold valve
remains in the same position. Confi rm that the pressure gauge shows–0.101 Mpa
[Gauge] (–760 mmHg).
Tighten the cap to the service port to obtain the initial status.
Pipe length up to 7 m
No gas charge is needed.
Pipe length exceeding 7 m
Charge the prescribed amount of
gas. (refer to 3)
Remove the gauge manifold valve quickly from the service port of the stop valve.
After refrigerant pipes are connected and evacuated, fully open all stop valves on
both sides of gas pipe and liquid pipe.
Operating without fully opening lowers the performance and this causes trouble.
Retighten the cap.
Leak test
*Close
*Open
*4 to 5 turns
Stop valve
(or the vacuum
pump with
the function
to prevent the
back fl ow)
Gauge manifold
valve (for R410A)
Pressure gauge
(for R410A)
Compound pressure
gauge (for R410A)
-0.101MPa
(-760 mmHg)
Handle
Low
Handle High
Window
Charge hose
(for R410A)
Vacuum
pump
Adapter for
preventing the
back fl ow
Charge hose
(for R410A)
Service port
Stop
valve
EMERGENCY
OPERATION switch
Mode Operation Indicator lamp
1
COOL
(Light)
(Off)
2
STOP
(Off)
(Off)
6-4 PURGING PROCEDURES·LEAK TEST
PROCEDURE
•
Press the EMERGENCY OPERATION switch.
1
Press it once, and after test run for 30 minutes the EMERGENCY COOL MODE starts.
2
Press it once more, and the operation stops.
(The operation mode changes in order of
1
~
2
every time the EMERGENCY
OPERATION switch is pressed.)
MSH type
•
Before performing the test run, recheck any wrong wiring.
Wrong wiring prevents normal operation or results in blown fuse disabling operation.
•
The test run can be started by pressing EMERGENCY OPERATION switch. When
the EMERGENCY OPERATION switch is once pressed, the unit will start the test run
(continuous operation) for 30 minutes.
A thermostat does not work during this time. After 30 minutes the unit will start the
EMERGENCY OPERATION at a fi xed temperature setting of 24°C in COOL MODE or
HEAT MODE.
•
Perform test run in the following procedure.
6-5 TEST RUN
MS type
•
Before performing the test run, recheck any wrong wiring.
Wrong wiring prevents normal operation or results in blown fuse disabling operation.
•
The test run can be started by pressing EMERGENCY OPERATION switch. When
the EMERGENCY OPERATION switch is once pressed, the unit will start the test run
(continuous operation) for 30 minutes.
A thermostat does not work during this time. After 30 minutes the unit will start the
EMERGENCY OPERATION at a fi xed temperature setting of 24°C in COOL MODE or
HEAT MODE.
•
Perform test run in the following procedure.
6-3 PIPE CONNECTION
Note:
Fasten a fl are nut with a torque wrench as specifi ed in the table below.
When fastened too tight, a fl are nut may broken after a long period and cause a leakage
of refrigerant.
1
Indoor unit connection
Connect both liquid and gas pipings to indoor unit.
•
Apply a thin coat of refrigeration oil
J
on the seat surface of pipe.
•
For connection fi rst align the center, then tighten the fi rst 3 to 4 turns of fl are nut.
•
Use tightening torque table below as a guideline for indoor unit side union joint
section, and tighten using two wrenches. Excessive tightening damages the fl are
section.
Pipe diameter
Tightening torque
mm
N·m
kgf·cm
6.35
13.7 to 17.7
140 to 180
9.52
34.3 to 41.2
350 to 420
12.7
49.0 to 56.4
500 to 575
15.88
73.5 to 78.4
750 to 800
2
Outdoor unit connection
Connect pipes to stop valve pipe joint of the outdoor unit in the same manner applied
for indoor unit.
•
For tightening, use a torque wrench or spanner and use the same tightening torque
applied for indoor unit.
INSULATION AND TAPING
1
Cover piping joints with pipe cover.
2
For outdoor unit side, surely insulate every piping including valves.
3
Using piping tape
G
, apply taping starting from the entry of outdoor unit.
•
Stop the end of piping tape
G
with tape (with adhesive agent attached).
•
When piping have to be arranged through above ceiling, closet or where the
temperature and humidity are high, wind additional commercially sold insulation for
prevention of condensation.
Hexagonal wrench
Tightening torque
N·m
kgf·cm
Cap for service port
13.7 to 17.7
140 to 180
Cap for stop valve
19.6 to 29.4
200 to 300
PROCEDURE
•
Press the EMERGENCY OPERATION switch.
1
Press it once, and after test run for 30 minutes the EMERGENCY COOL MODE starts.
If the left side lamp of the operation indicator blinks every 0.5 seconds, inspect the
indoor/outdoor unit connecting wire
A
for mis-wiring.
2
Press it once more, and the EMERGENCY HEAT MODE starts.
3
Press it once more, and the operation stops.
(The operation mode changes in order of
1
~
3
every time the EMERGENCY
OPERATION switch is pressed.)
EMERGENCY
OPERATION switch
Mode Operation Indicator lamp
1
COOL
(Light)
(Off)
2
HEAT
(Off)
(Light)
3
STOP
(Off)
(Off)
•
In starting the heating operation, indoor unit fan may not operate to prevent blowing
cool air. Please wait for a few minutes until the temperature of heat exchanger rises
and warm air blows out.
MS type and MSH type
Checking the remote (infrared) signal reception
Press the ON/OFF button on the remote controller and check that an electronic sound is
heard from the indoor unit. Press the ON/OFF button again to turn the air conditioner off.
If the indoor unit is operated with the remote controller, both the
test run and the emergency operation are released by commands
from the remote controller.
•
Once the compressor stops, the restart preventive device operates so the compressor
will not operate for three minutes to protect the air conditioner.
6-6 EXPLANATION TO THE CUSTOMER
•
Using the OPERATING INSTRUCTIONS, explain the following to the customer, how
to control temperature, how to remove the air fi lters, how to remove or put the remote
controller in the remote controller holder, how to clean, precautions for operation, etc.
•
Recommend the customer to read the OPERATING INSTRUCTIONS carefully.
Stop valve