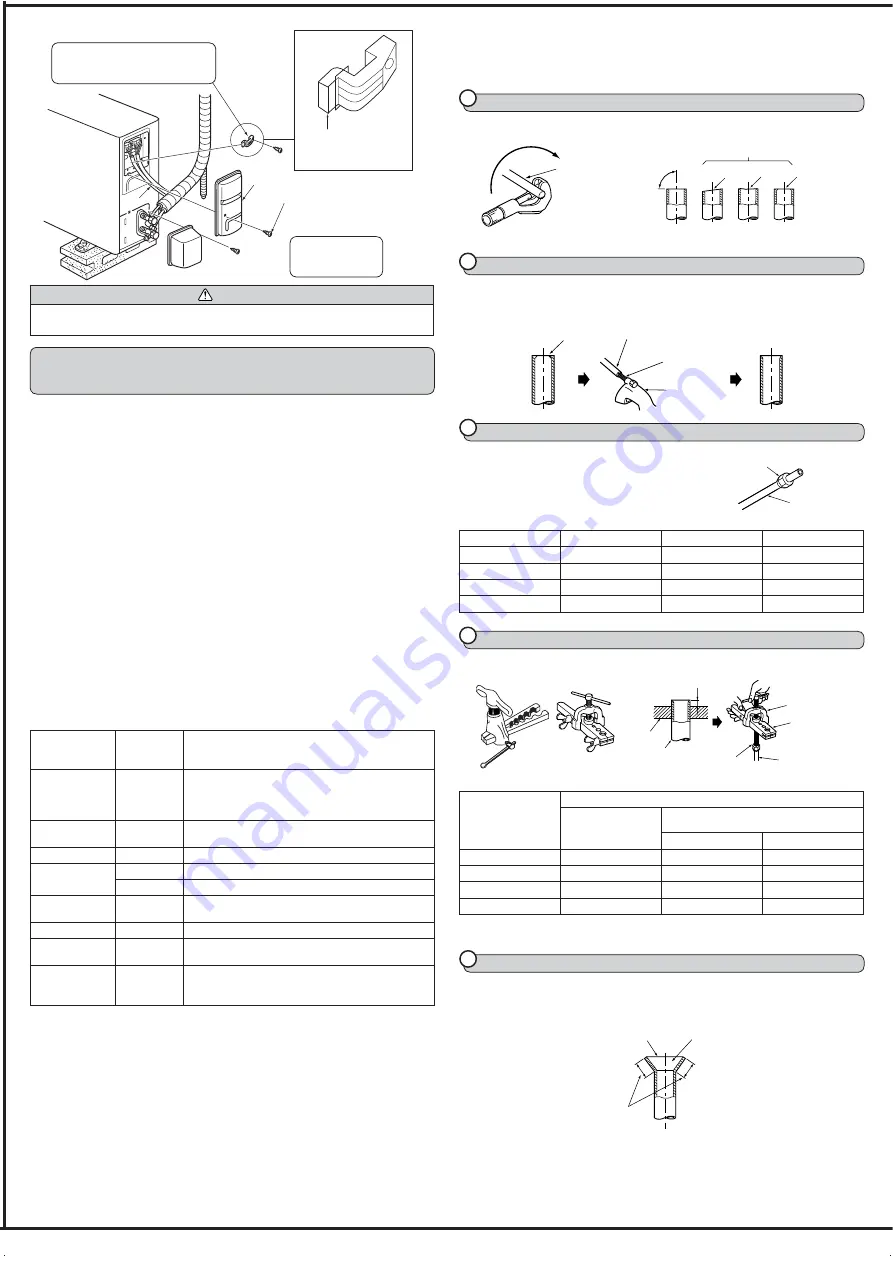
Smooth all around
Even length
all around
Inside is shining without any scratches.
Copper pipe
Good
No good
Tilted
Uneven
Burred
Burr
Copper pipe
Spare
reamer
Pipe
cutter
90
°
Remove two fi xing
screws to open the
service panel.
Service panel
Fixing screws
Be sure to put the left
portion into the square
hole of the service panel.
Be sure to fi x the indoor/outdoor unit
connecting wire
A
and power supply
cord
K
using this cord clamp.
Valve cover
WARNING
Be sure to attach the service panel of the outdoor unit securely. If it is not attached
correctly, it could result in a fi re or an electric shock due to dust, water, etc.
6. INDOOR/OUTDOOR UNIT CONNECTION
FINISHING AND TEST RUN
INSTALLATION INFORMATION FOR THE AIR CONDITION-
ER WITH R410A REFRIGERANT
•
This room air conditioner adopts an HFC refrigerant (R410A) which will never destroy
the ozone layer.
•
Pay particular attention to the following points, though the basic installation proce-
dure is same as that for R22 air conditioners.
1
As R410A has a working pressure approx. 1.6 times as high as that of R22, some
special tools and piping parts / materials are required. (Refer to the table below.)
2
Take suffi cient care not to allow water and other contaminations to enter the
R410A refrigerant during storage and installation, since it is more susceptible to
contaminations than R22.
3
For refrigerant piping, use clean, pressure-proof parts / materials specifi cally de-
signed for R410A. (Refer to 2. Refrigerant piping.)
4
Composition change may occur in R410A since it is a mixed refrigerant. When
charging, charge liquid refrigerant to prevent composition change.
6-1 Tools dedicated for the air conditioner with R410A
refrigerant
The following tools are required for R410A refrigerant. Some R22 tools can be substi-
tuted for R410A tools.
The diameter of the service port on the stop valve in outdoor unit has been changed to
prevent any other refrigerant being charged into the unit. (Cap size has been changed
from 7/16 UNF with 20 threads to 1/2 UNF with 20 threads.)
R410A tools
Can R22
tools be
used?
Description
Gauge manifold
No
R410A has high pressures beyond the measurement range
of existing gauges.
Port diameters have been changed to prevent any other
refrigerant from being charged into the unit.
Charge hose
No
Hose material and cap size have been changed to improve
the pressure resistance.
Gas leak detector
No
Dedicated for HFC refrigerant.
Torque wrench
Yes
1/4
No
1/2 and 5/8
Flare tool
Yes
Clamp bar hole has been enlarged to reinforce the spring
strength in the tool.
Flare gauge
New
Provided for fl aring work (to be used with R22 fl are tool).
Description
New
Provided to prevent the back fl ow of oil. This adapter
enables you to use existing vacuum pumps.
Electronic scale
for refrigerant
charging
New
It is diffi cult to measure R410A with a charging cylinder
because the refrigerant bubbles due to high pressure and
high-speed vaporization.
No: Not substitutable for R410A Yes: Substitutable for R410A
6-2 FLARING WORK
•
Main cause of gas leakage is defect in fl aring work.
Carry out correct fl aring work in the following procedure.
1 Pipe cutting
• Cut the copper pipe correctly with pipe cutter.
2 Burrs removal
• Completely remove all burrs from the cut cross section of pipe.
• Put the end of the copper pipe to downward direction as you remove burrs in order to
avoid to let burrs drop in the piping.
3 Putting nut on
• Remove
fl are nuts attached to indoor and outdoor
units, then put them on pipe having completed
burr removal.
(not possible to put them on after fl aring work)
• Flare nut for R410A pipe differs from R22 pipe.
Refer to the following table for detail.
mm
inch
R410A
R22
ø6.35
1/4
17
17
ø9.52
3/8
22
22
ø12.7
1/2
26
24
ø15.88
5/8
29
27
4 Flaring work
• Carry
out
fl aring work using fl aring tool as shown below.
Outside diameter
A (mm)
Flare tool for
R410A clutch type
Conventional fl are tool
Clutch type
Wing nut type
ø6.35 mm
0 to 0.5
1.0 to 1.5
1.5 to 2.0
ø9.52 mm
0 to 0.5
1.0 to 1.5
1.5 to 2.0
ø12.7 mm
0 to 0.5
1.0 to 1.5
2.0 to 2.5
ø15.88 mm
0 to 0.5
1.0 to 1.5
2.0 to 2.5
• Firmly hold copper pipe in a die in the dimension shown in the table above.
5 Check
• Compare
the
fl ared work with fi gure below.
• If
fl are is noted to be defective, cut off the fl ared section and do fl aring work again.
Flare nut
Copper pipe
A
Die
Copper pipe
Flare nut
Die
Copper pipe
York
Flaring tool
Wing nut type
Clutch type