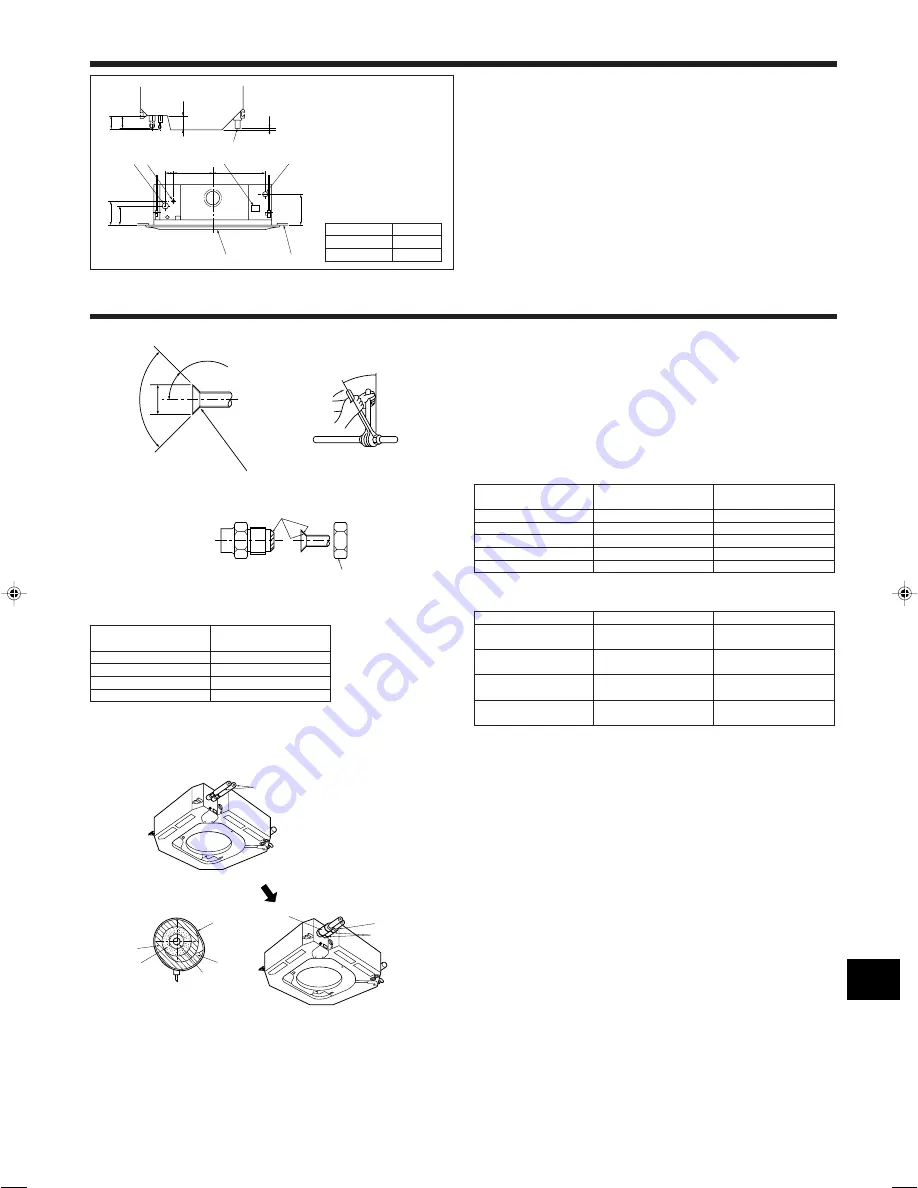
5
4. Installing the pipes
4.1. Refrigerant and drainage piping locations of indoor
unit
The figure marked with * in the drawing represent the dimensions of the main unit
excluding those of the optional multi function casement. (Fig. 4-1)
A
Drain pipe
B
Ceiling
C
Grille
D
Refrigerant pipe (liquid)
E
Refrigerant pipe (gas)
F
Water supply inlet
G
Main unit
• When the optional multi-functional casement is installed, add 135 mm to the di-
mensions marked on the figure.
(mm)
Models
A
RP3
80
RP4, 5, 6
84
16
89
A
98
G
A
∗
170
∗
140
∗
190
60
286
374
A
F
D
E
B
C
Fig. 4-1
5. Refrigerant piping work
5.1. Connecting pipes (Fig. 5-1)
• When commercially available copper pipes are used, wrap liquid and gas pipes
with commercially available insulation materials (heat-resistant to 100 °C or more,
thickness of 12 mm or more).
• The indoor parts of the drain pipe should be wrapped with polyethylene foam insu-
lation materials (specific gravity of 0.03, thickness of 9 mm or more).
• Apply thin layer of refrigerant oil to pipe and joint seating surface before tightening
flare nut.
• Use two wrenches to tighten piping connections.
• Use refrigerant piping insulation provided to insulate indoor unit connections. Insu-
late carefully.
A
Flare cutting dimensions
Copper pipe O.D.
Flare dimensions
(mm)
øA dimensions (mm)
ø6.35
8.7 - 9.1
ø9.52
12.8 - 13.2
ø12.7
16.2 - 16.6
ø15.88
19.3 - 19.7
B
Flare nut tightening torque
Copper pipe O.D.
Flare nut O.D.
Tightening torque
(mm)
(mm)
(N·m)
ø6.35
17
14 - 18
ø9.52
22
34 - 42
ø12.7
26
49 - 61
ø15.88
29
68 - 82
ø15.88
36
100 - 120
Indoor unit (Liquid)
Indoor unit (Gas)
Outdoor unit (Liquid)
Outdoor unit (Gas)
RP3
Flare nut attached to
indoor liquid valve
Flare nut attached to
indoor gas valve
Flare nut attached to
outdoor liquid valve
Flare nut attached to
outdoor gas valve
RP4-6
Flare nut attached to
indoor liquid valve
* Flare nut in outdoor
unit accessories
Flare nut attached to
outdoor liquid valve
Flare nut attached to
outdoor gas valve
* In case that the flare nut attached to indoor gas valve is used, gas leakage or even
pipe extraction will occur.
90
°
±
0.5
°
ø
A
R0.4~R0.8
A
45
°±
2
°
B
C
D
Fig. 5-1
B
D
E
A
C
F
J
H
I
B
,
C
F
G
Fig. 5-2
A
Refrigerant pipe and insulating ma-
terial
B
Pipe cover (large)
C
Pipe cover (small)
D
Refrigerant pipe (gas)
E
Refrigerant pipe (liquid)
F
Band
G
Cross-sectional view of connection
H
Pipe
I
Insulating material
J
Squeeze
C
Apply refrigerating machine oil over the entire flare seat surface.
D
Use the flare nuts as follows.
5.2. Indoor unit (Fig. 5-2)
Heat insulation for refrigerant pipes:
1
Wrap the enclosed large-sized pipe cover around the gas pipe, making sure that
the end of the pipe cover touches the side of the unit.
2
Wrap the enclosed small-sized pipe cover around the liquid pipe, making sure
that the end of the pipe cover touches the side of the unit.
3
Secure both ends of each pipe cover with the enclosed bands. (Attach the bands
20 mm from the ends of the pipe cover.)
• After connecting the refrigerant piping to the indoor unit, be sure to test the pipe
connections for gas leakage with nitrogen gas. (Check that there is no refrigerant
leakage from the refrigerant piping to the indoor unit.)
5.3. For twin/triple combination
Refer to the outdoor unit installation manual.