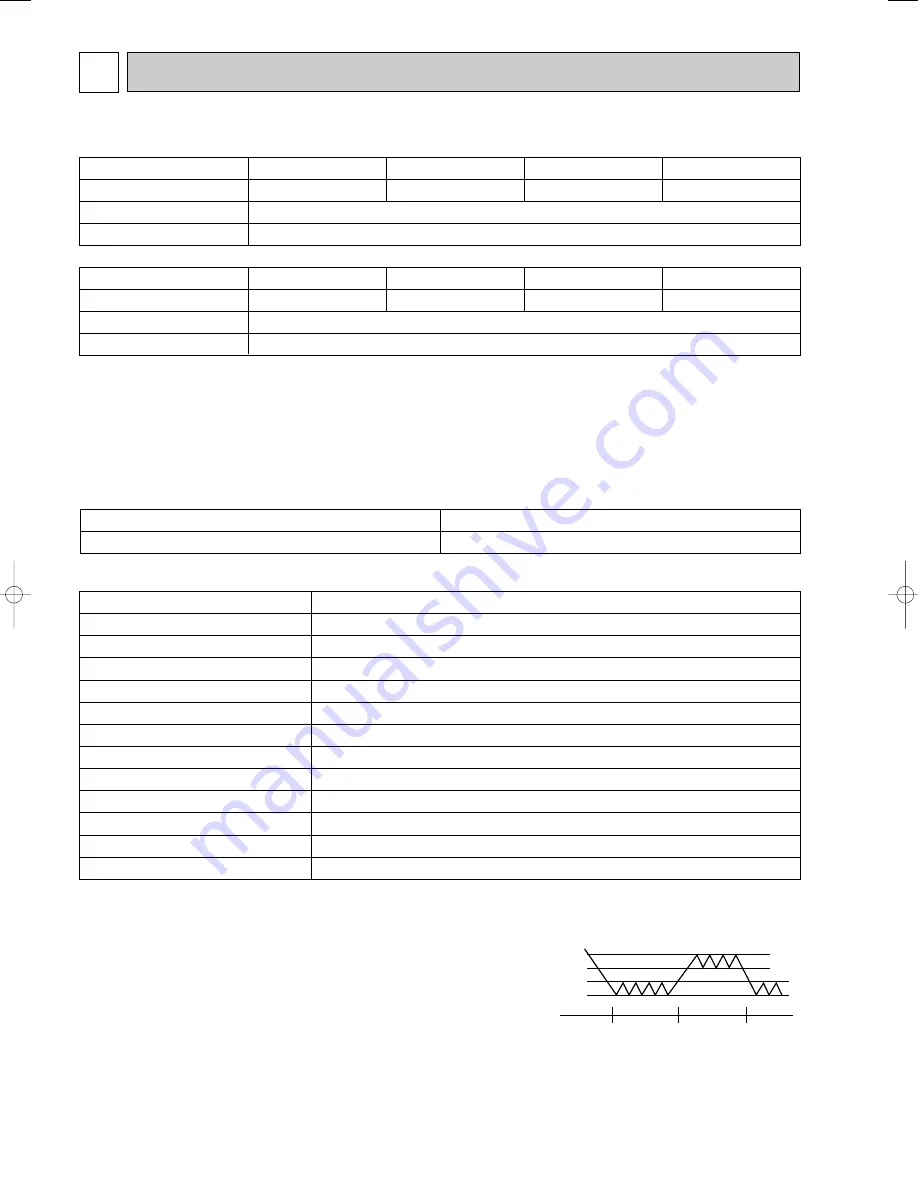
80
14
OPTIONAL PARTS
Note 1. How to connect refrigerant pipes.
Factory supplied optional refrigerant pipings contain refrigerant at the above atmospheric pressures. As long as the
connection takes no more than 5 minutes, no air will enter, and there will be no need for air purging. Remove the blind
caps and make the connections within 5 minutes. After the connections for the indoor and outdoor units are made,
open the stop valve on the outdoor unit to allow refrigerant gas to flow.
If piping length exceeds 5m,an additional charge of refrigerant is needed.
Note 2. The following main parts are contained in the optional refrigerant piping kit.
Heat insulating cover, vinyl tapes, nipples, sleeve and flange (for wall hole).
2-2. Feature of program timer
(1) Daily timer function
Daily timer can be set in 30 minutes units for up to 24 hours.
Each unit can be set for unit ON, unit OFF, or setback operation.
(2) Setback operation (PAC-SC32PTA)
Set back operation is useful for reducing running costs
e.g. At a hotel with a 24-hour system
8:00~23:00 Cooling operation with set temperature at 26°C
23:00~8:00 Setback operation with 2 degrees of setback
As shown in the chart on the right, the set temperature rises 2 degrees
automatically during the setback operation. When the setback operation
ends, normal operation will begin.
(3) Weekly timer function
Daily timer function can apply to each day of the week.
1. REFRIGERANT PIPES
Service Ref. : PKH-2FKA
3
, PKH-2.5FKA
2
, PKH-2.5FKA
3
, PKH-3FKA
2
, PKH-3FKA
3
Part No.
Pipe length
Pipe size O.D.
Connection method
PAC-05FFS-E
5m
Liquid:
{
9.52 Gas:
{
15.88
Indoor unit:Flared Outdoor unit:Flared
PAC-07FFS-E
7m
PAC-10FFS-E
10m
PAC-15FFS-E
15m
2. TIMER
Part No
Model Name
PAC-SC32PTA
Program timer
2-1. Program timer specifications
Parts name
Parts No.
Exterior dimensions (inch)
Installation
Type of clock
Clock accuracy
Display-Time
-Week
-Timer setting unit
Program cycle
Timer setting unit
No. of set points
Power rating
Program timer
PAC-SC32PTA
5-4/32
o
4-23/32
o
23/32 (130
o
120
o
18mm)
Wall mount
Quartz
±
50 second / month at 25
:
Liquid crystal display
Liquid crystal display
Liquid crystal display
24 hours
30 minutes
48 / day
5V DC
±
5% (Suppled by Remote Controller)
28
˚
C
26
˚
C
8:00
Normal
operation
23:00
Setback
operation
8:00
Normal
operation
Service Ref. : PKH-4FKSA
2
, PKH-4FKSA
3
Part No.
Pipe length
Pipe size O.D.
Connection method
PAC-SC51PI-E
5m
Liquid:
{
9.52 Gas:
{
19.05
Indoor unit:Flared Outdoor unit:Flared
PAC-SC52PI-E
7m
PAC-SC53PI-E
10m
PAC-SC54PI-E
15m
OC132--3.qxp 1.11.8 10:44 AM Page 80
Summary of Contents for Mr.SLIM PKH-2.5FKA
Page 85: ......